Product Gallery

ROOF FRAME
High quality standard required for this die for aluminium part.

TUNNEL
Technical complexity due to the springback related to part feasibility
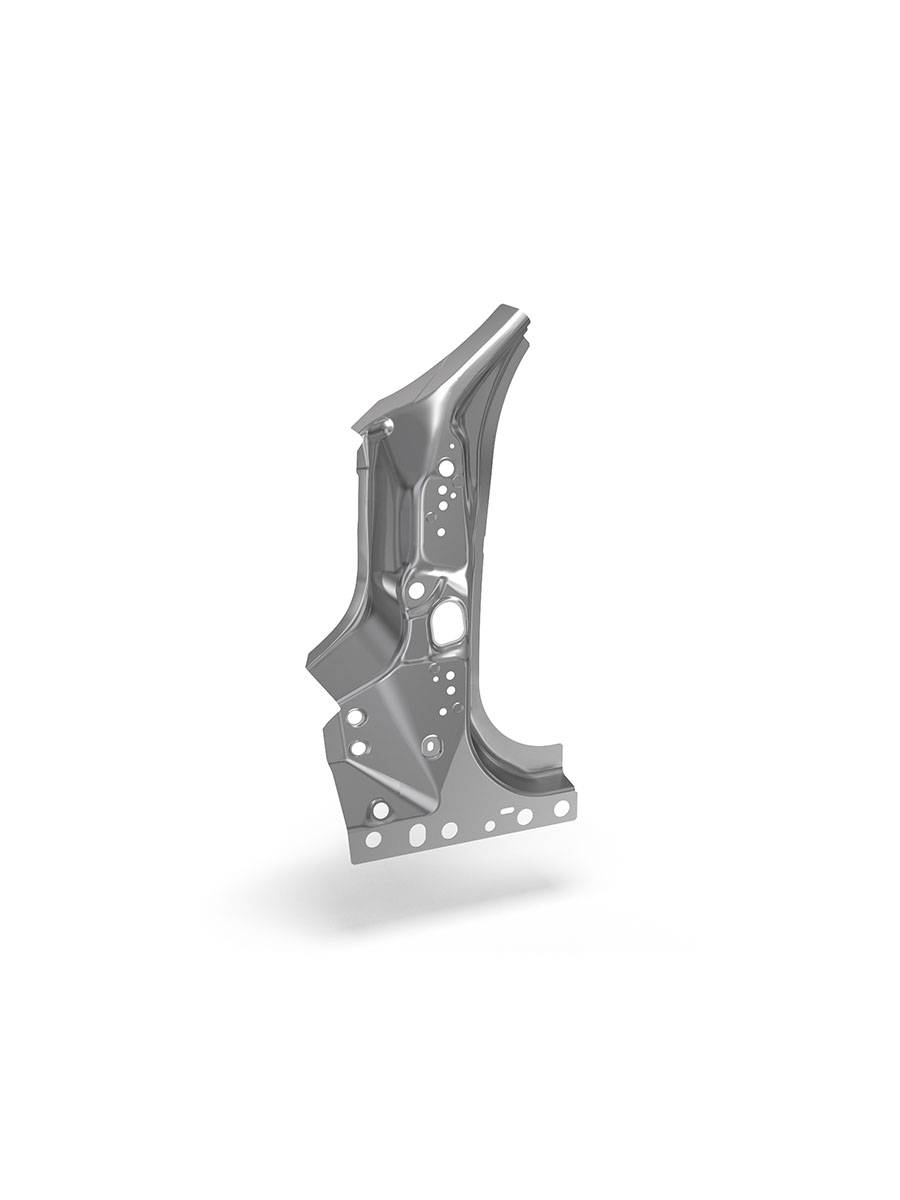
A-PILLAR
Complex feasibility, patches can be added
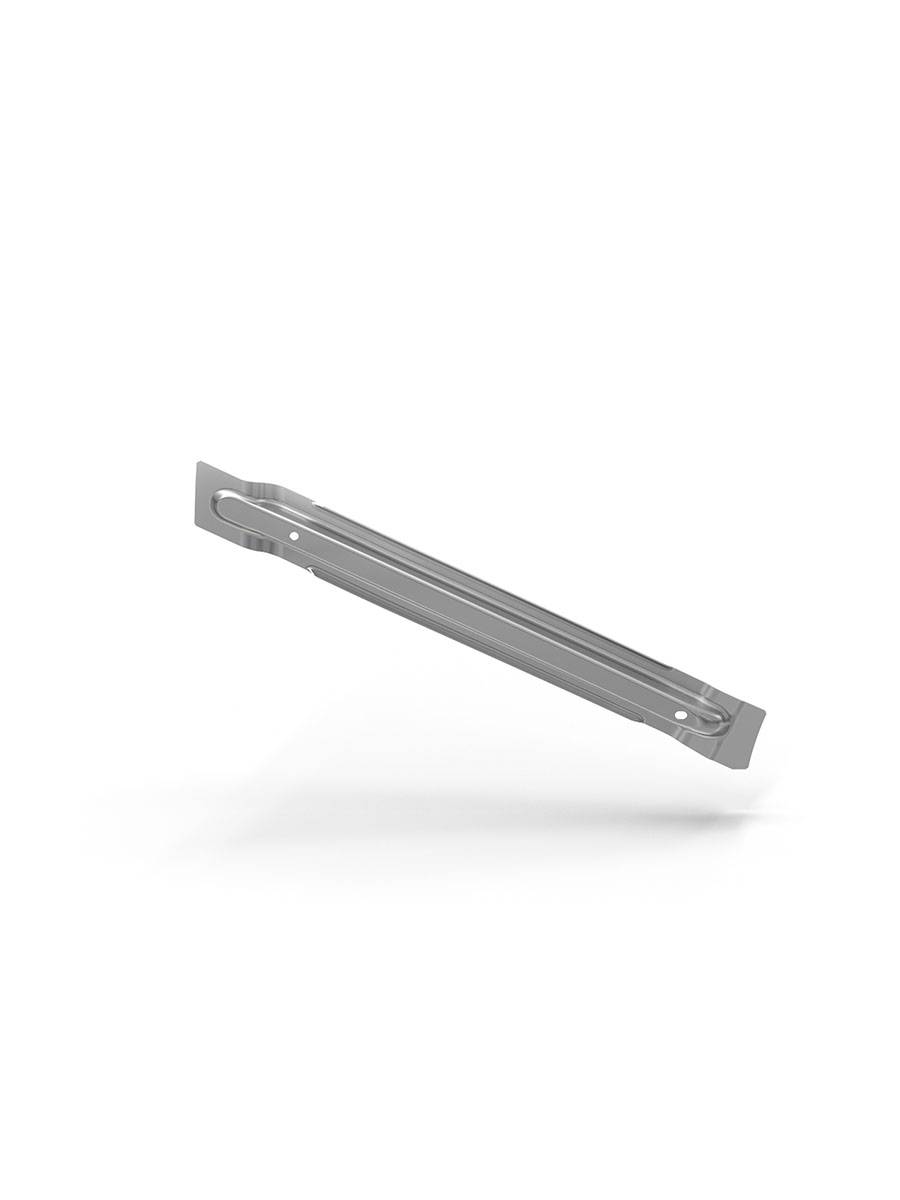
DOOR IMPACT BEAM
Simultaneous forming and piercing of the part
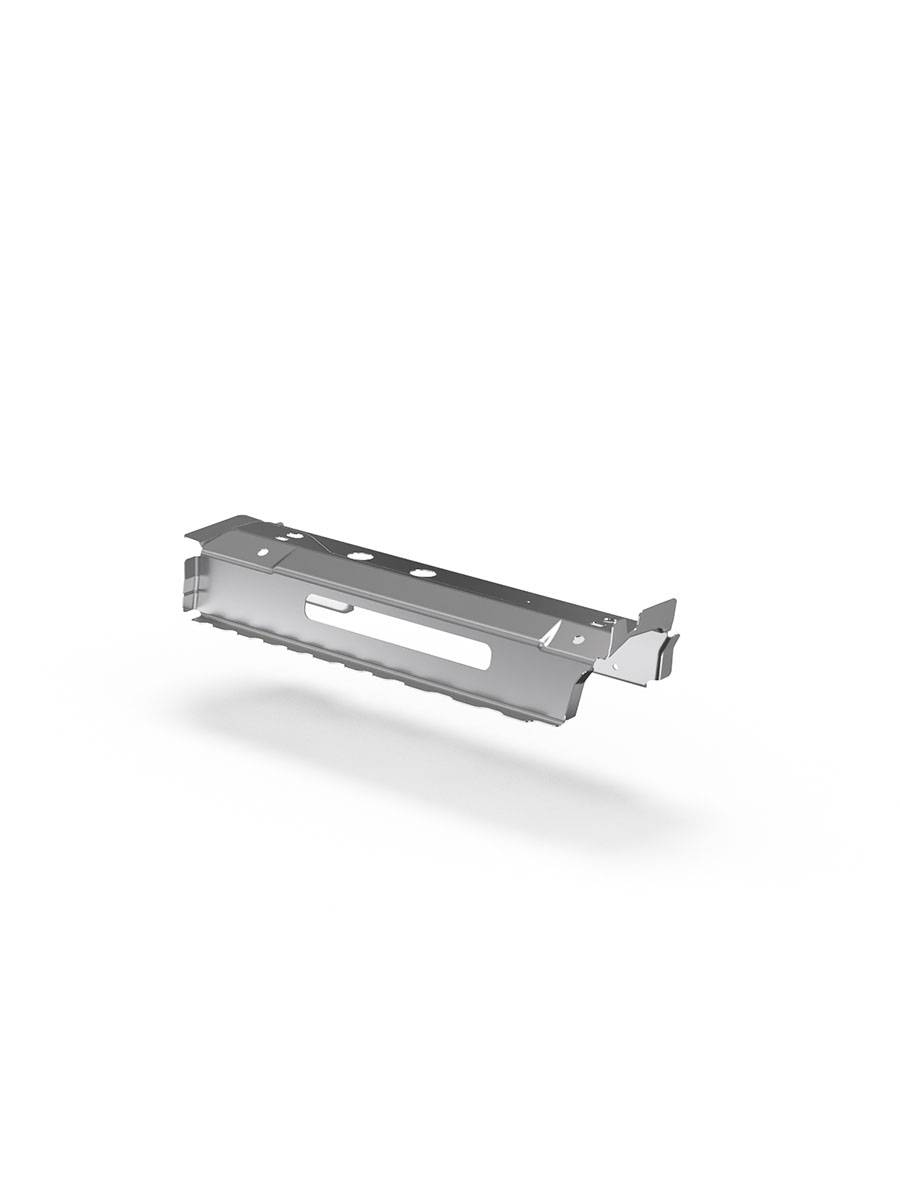
UNDER-SEAT CROSSMEMBER
Part in Ultra-high resistance metal sheet DP1000.
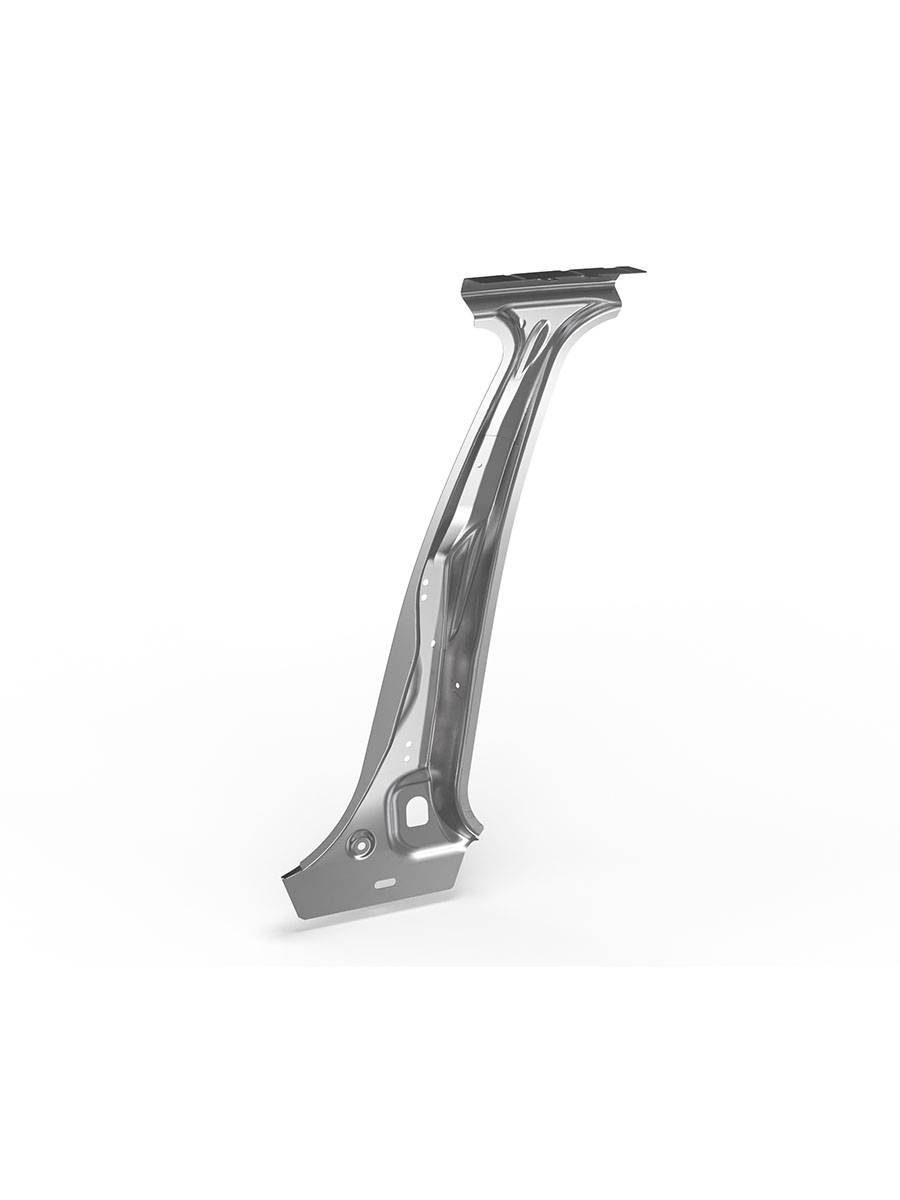
B-PILLAR
Complex feasibility, further technologies can be combined: Tailor Welded Blank TWB, Tailor Rolled Blank TRB, Soft Zone
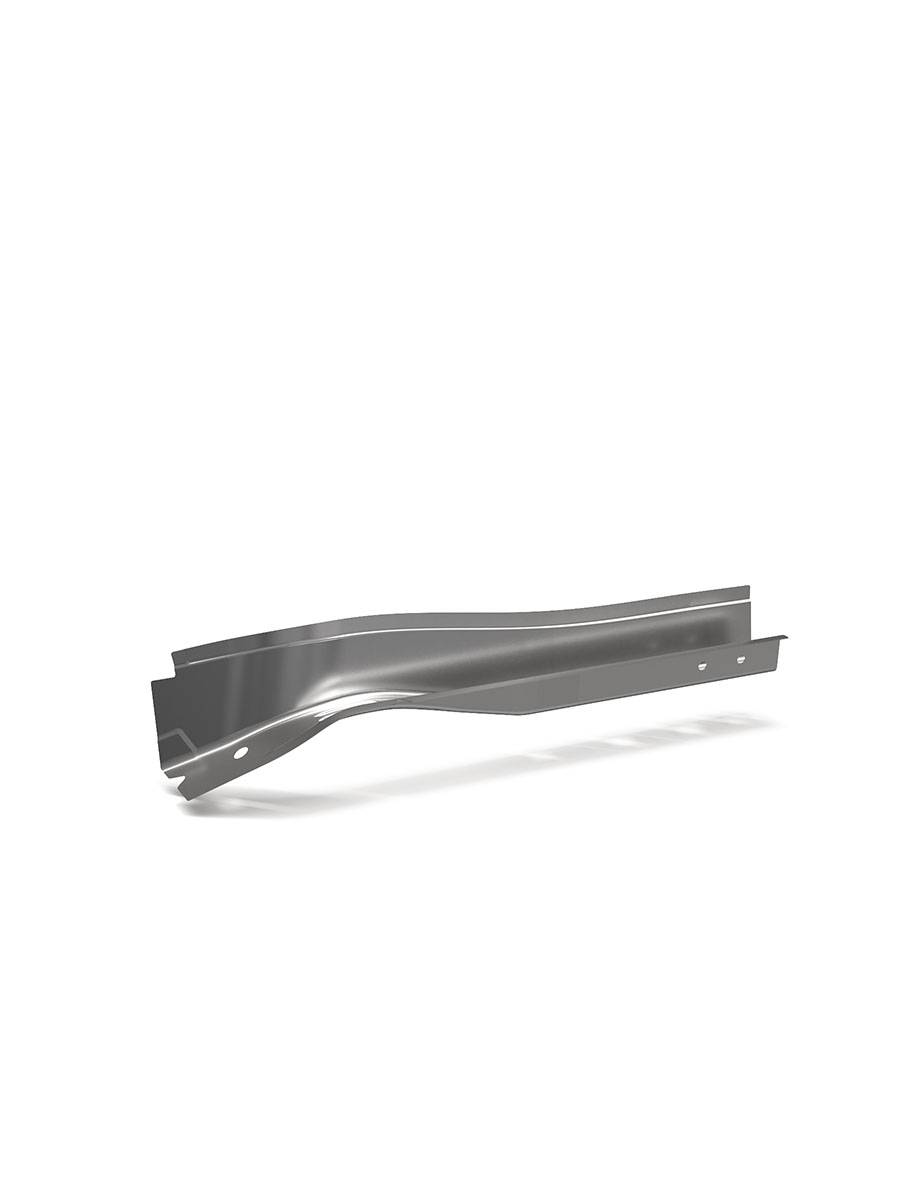
REAR SIDE MEMBER
Multiple technologies can be combined: Tailor Welded Blank TWB, Tailor Rolled Blank TRB
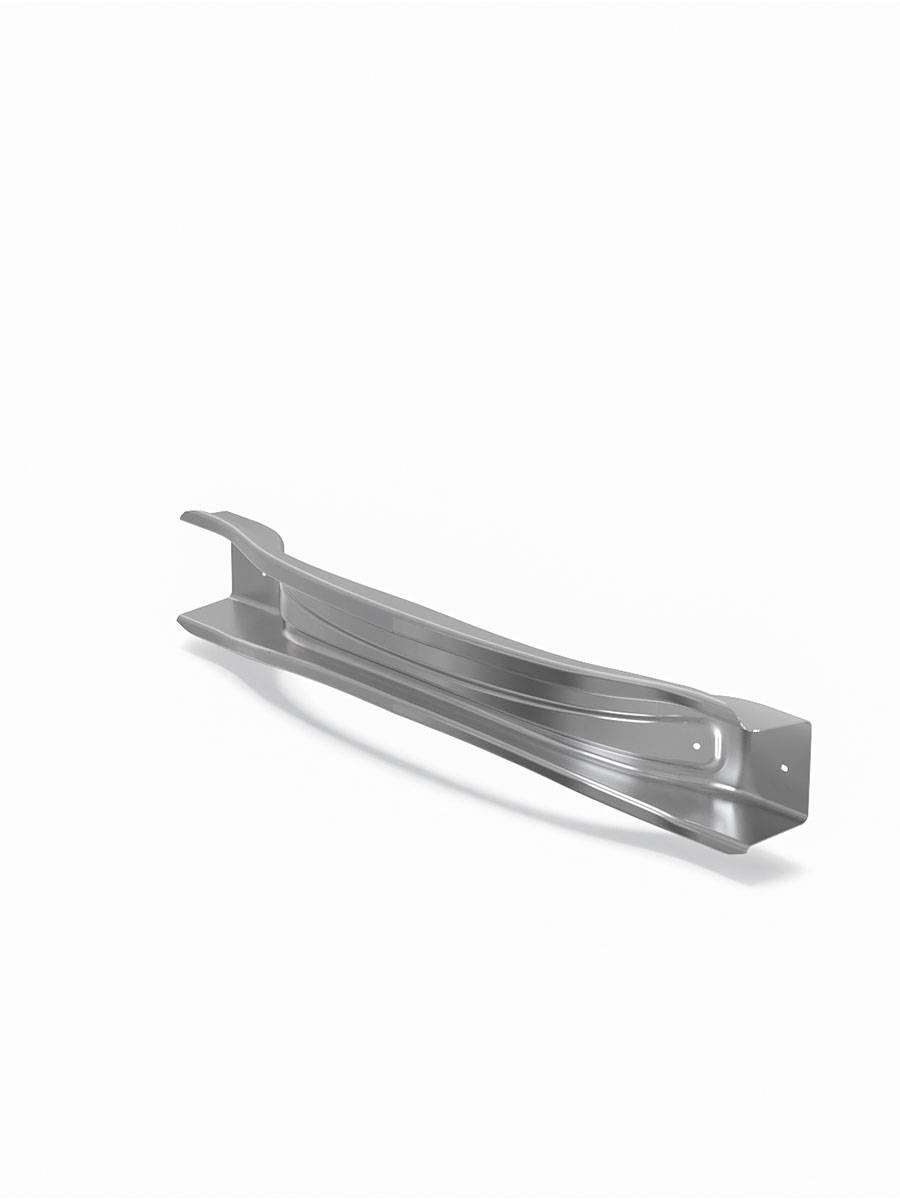
BUMPER
Complex feasibility and predeveloped trim.
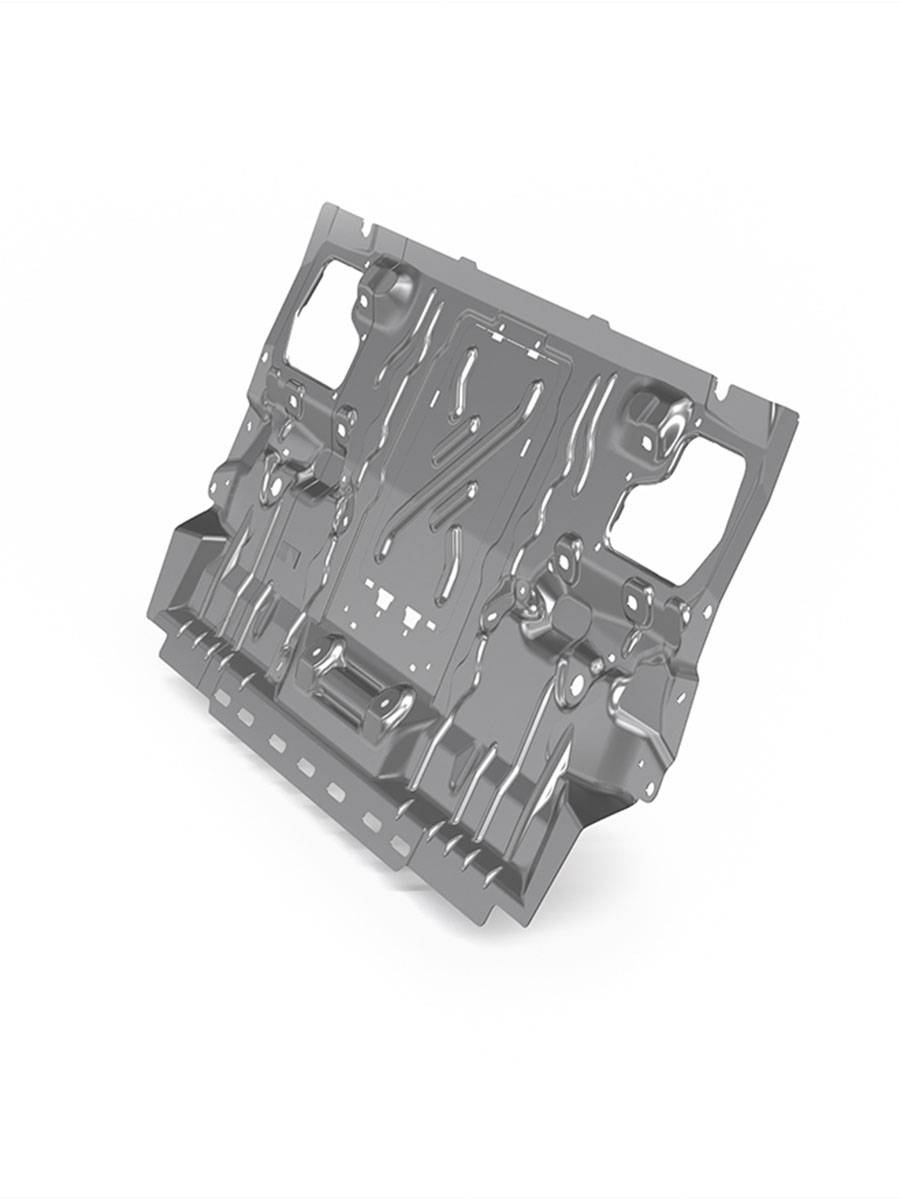
REAR SEAT REINFORCEMENT
Part in TWB. Complex die due to part modularity: interchangeable trimming to implement ski box.
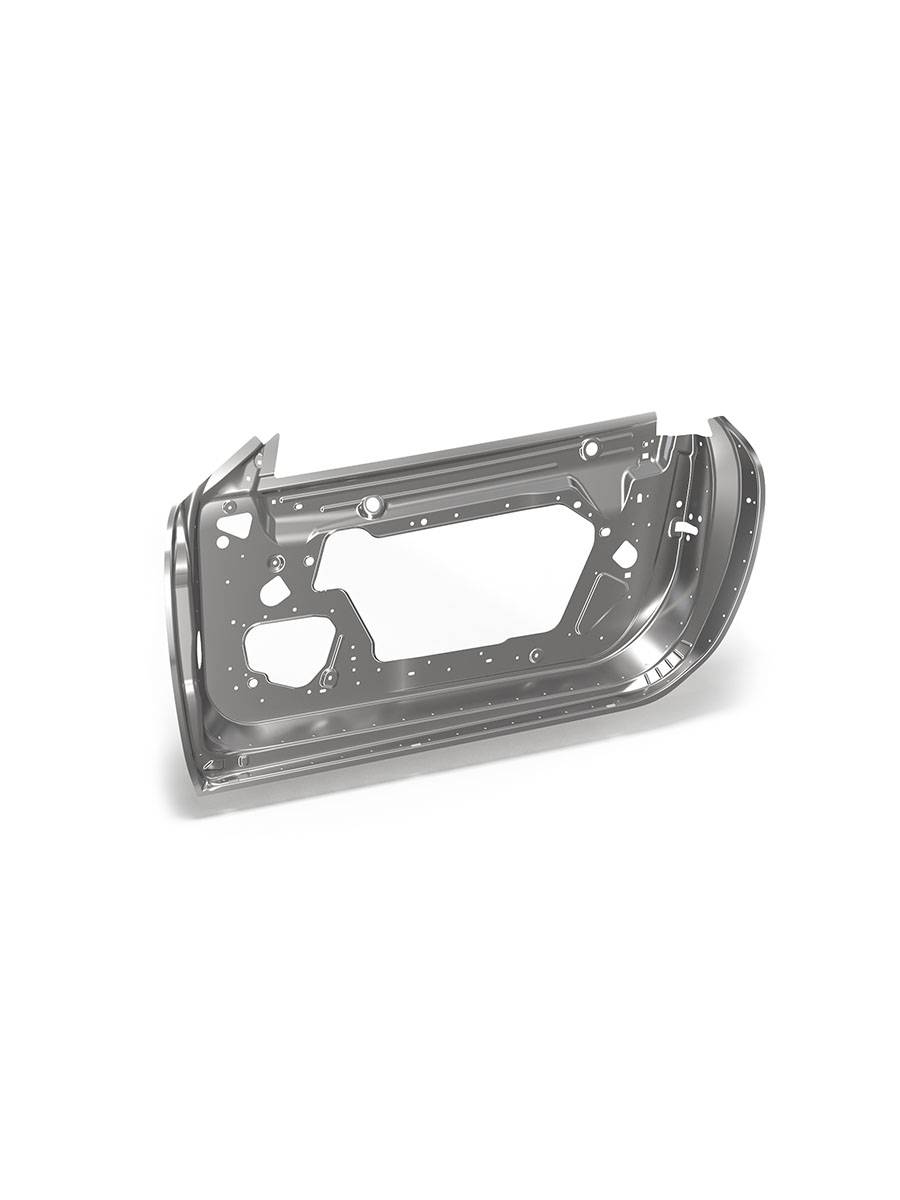
FRONT DOOR FRAME
High quality standard required for this die for aluminium inner frame combined with outer skin.
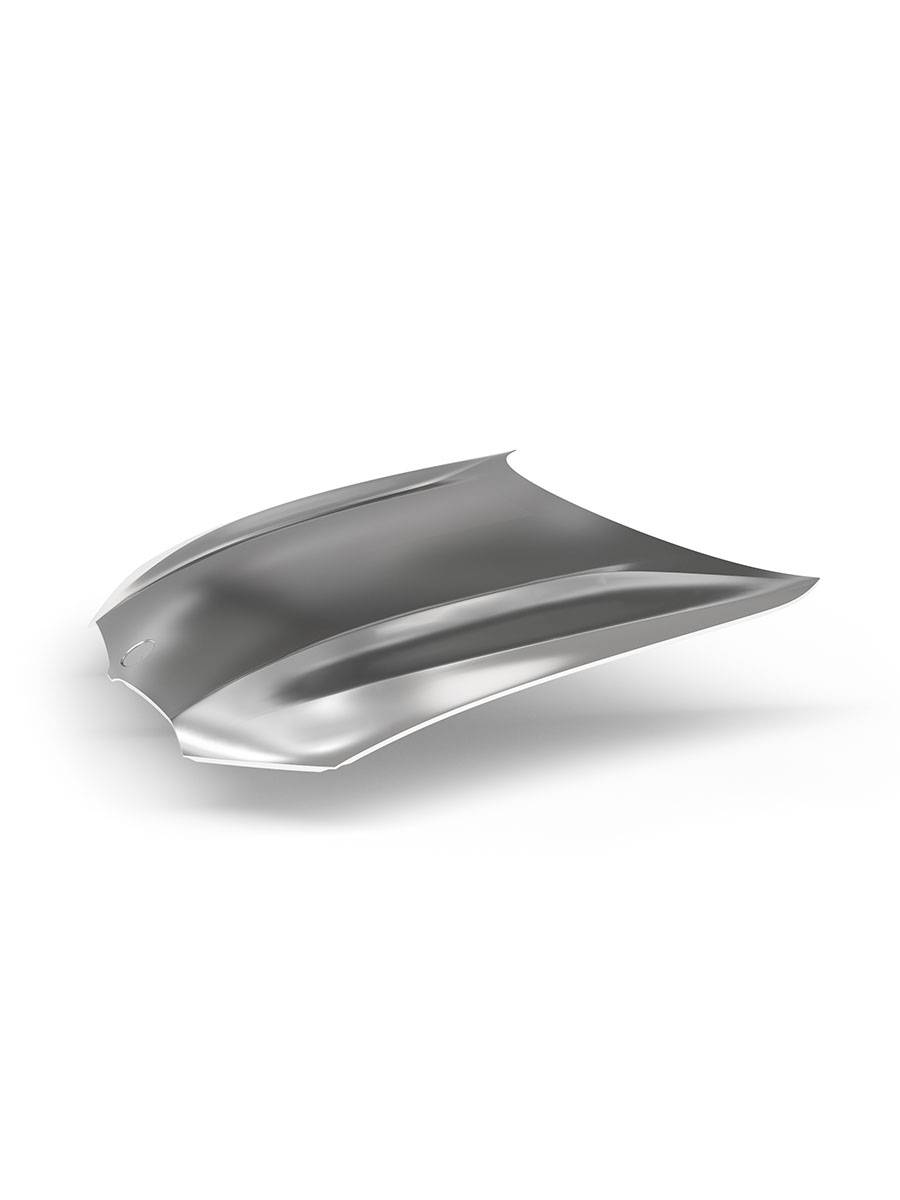
FRONT HOOD PANEL
High quality standard required for this die for outer skin in aluminum sheet.
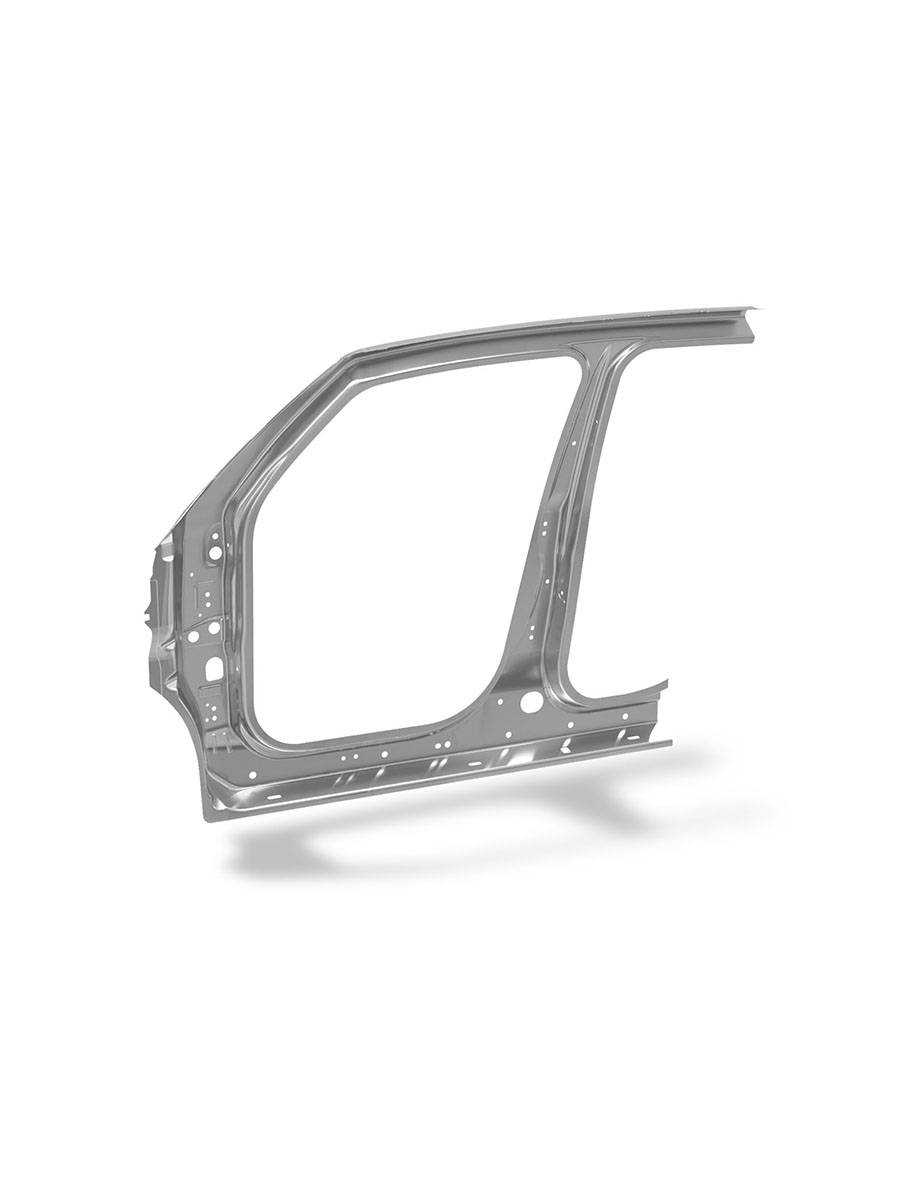
DOOR RING
Outstanding die with major technological impact combining all side parts in only one part.
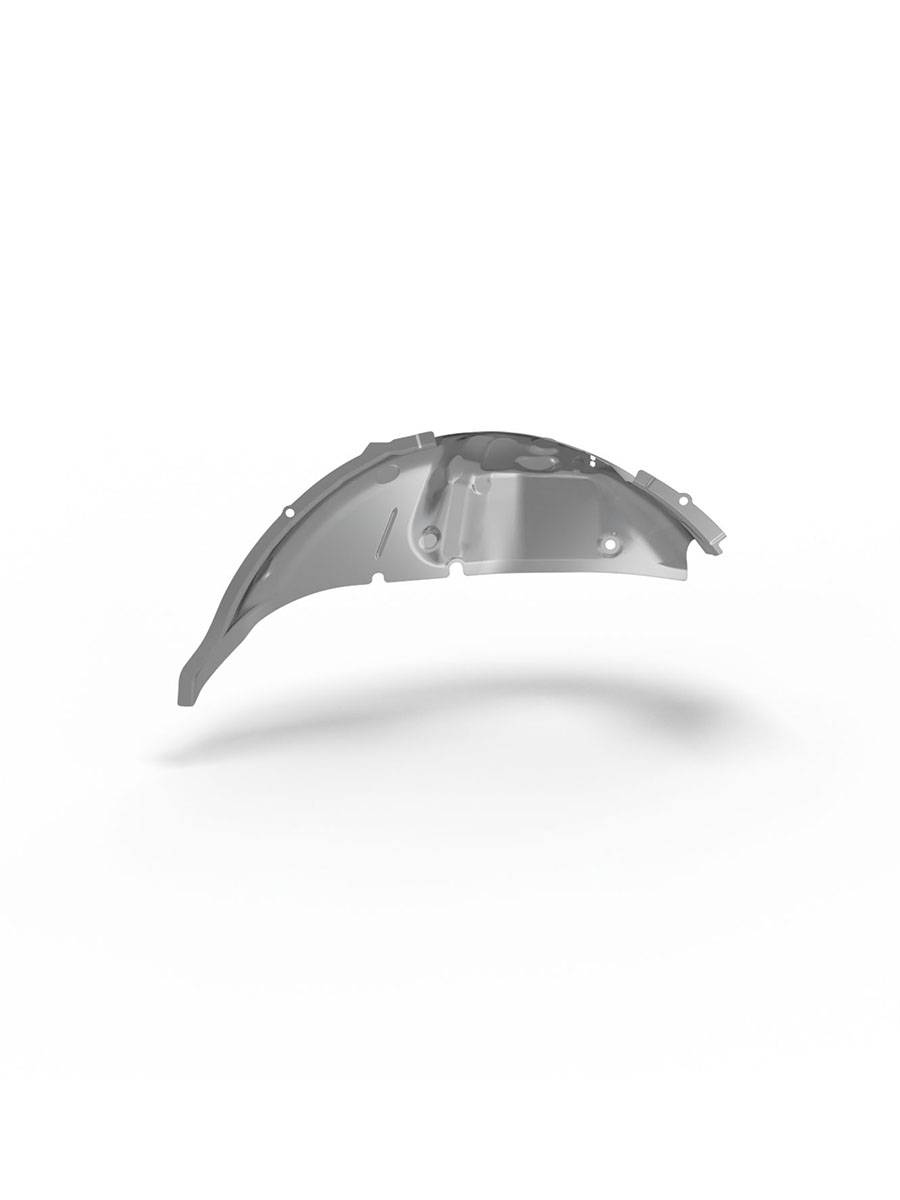
WHEEL ARCH REAR
High quality standard required for this die
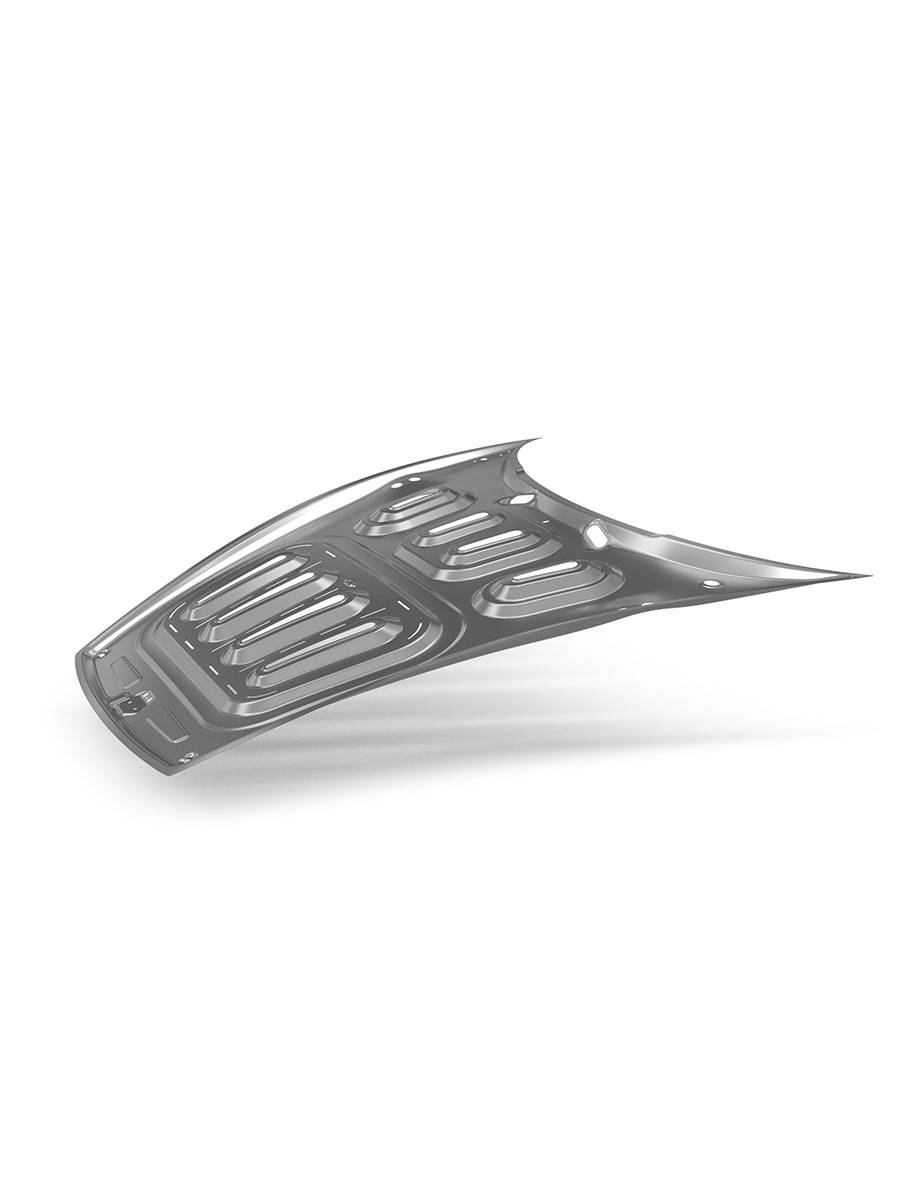
FRONT HOOD FRAME
High quality standard required for this die.
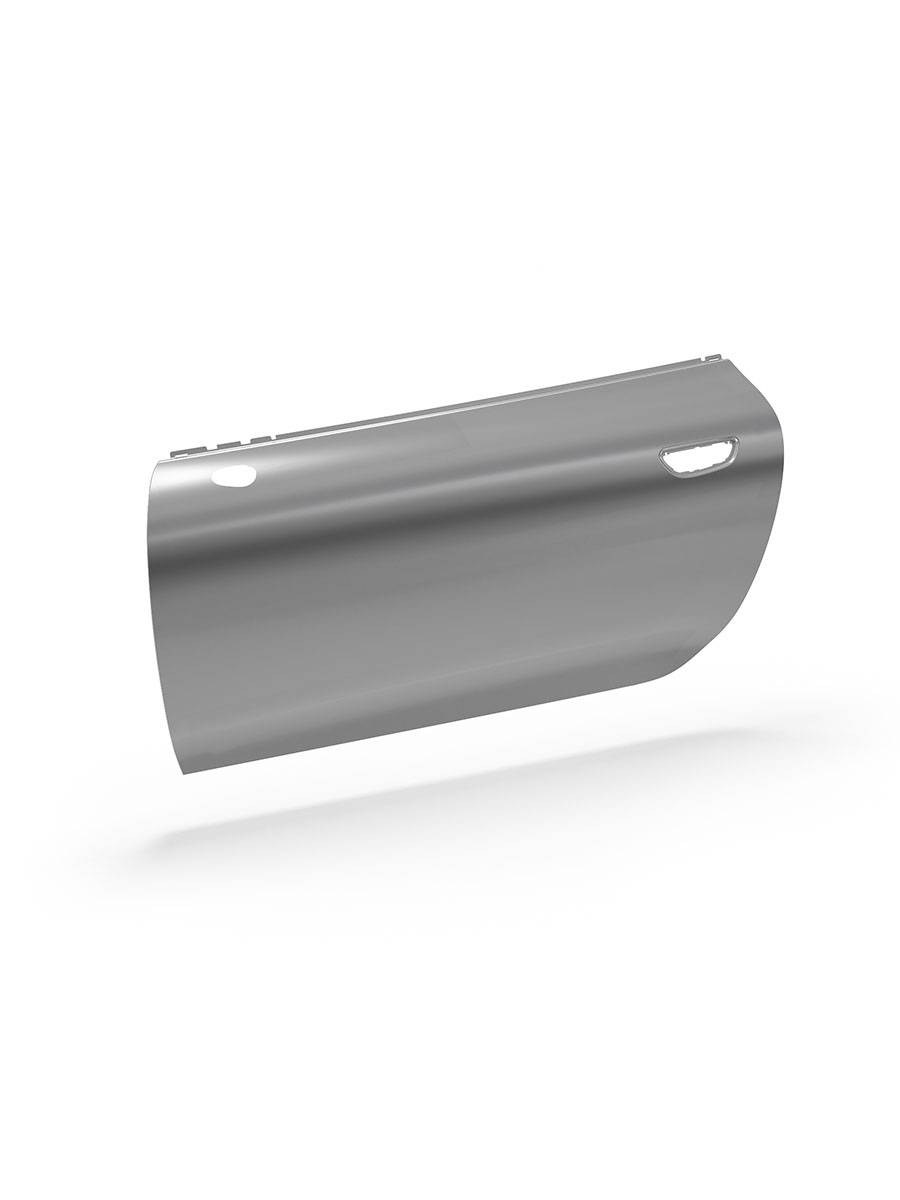
DOOR PANEL
Outer skin in aluminium sheet, high quality standard required for this die.
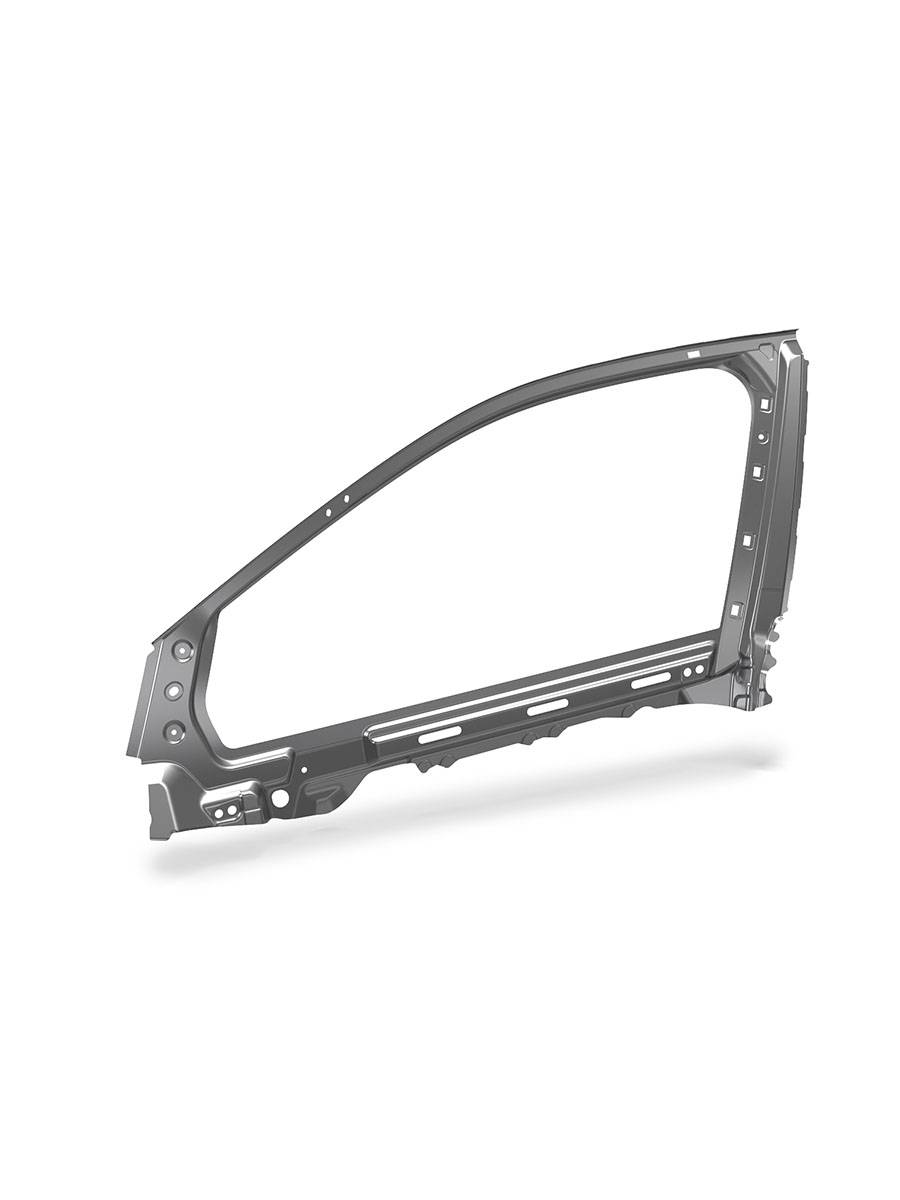
FRONT WINDOW FRAME
Part stamping is complex due to insert/insertion of standard part and nuts.
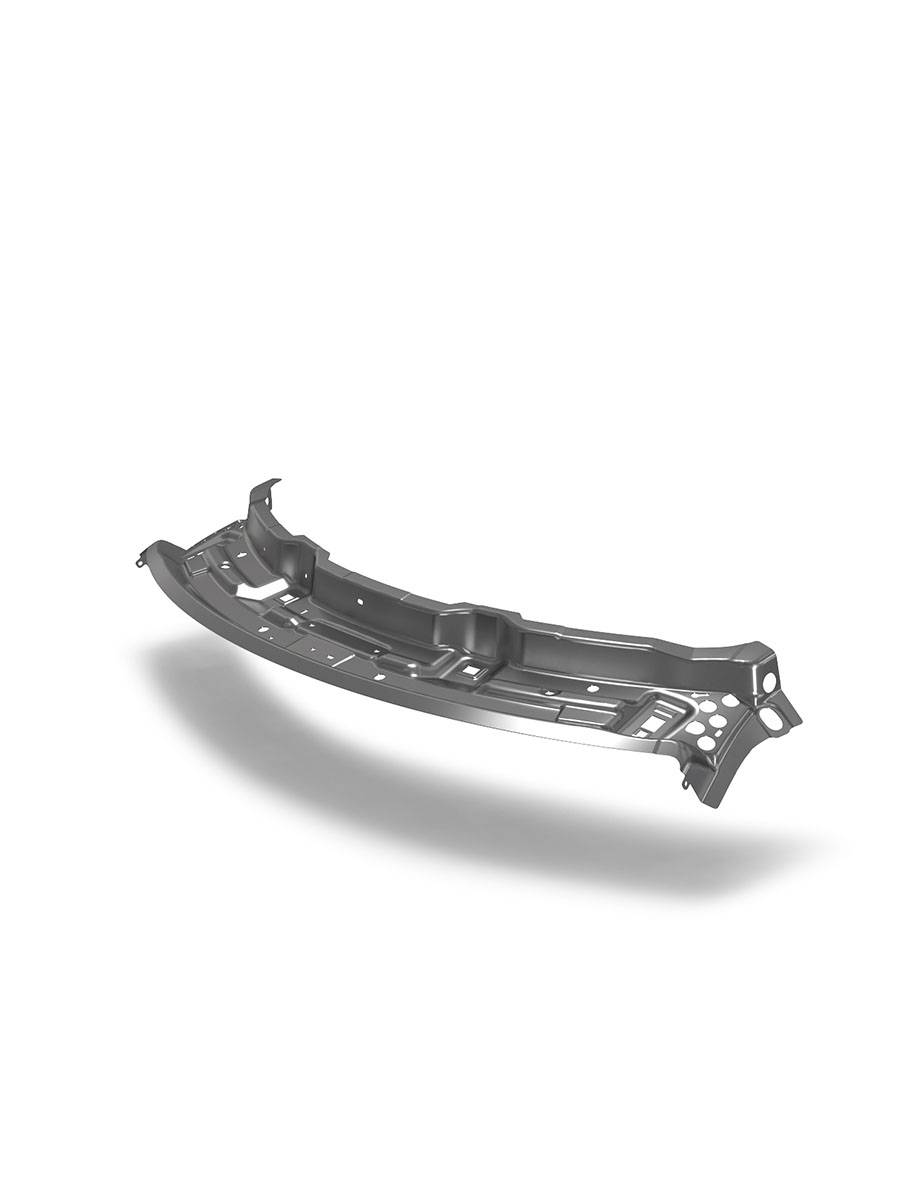
WINDSHIELD REINFORCEMENT
Complex geometry due to the different materials stamped like TWB, TRB, co-stamping with carbon parts.
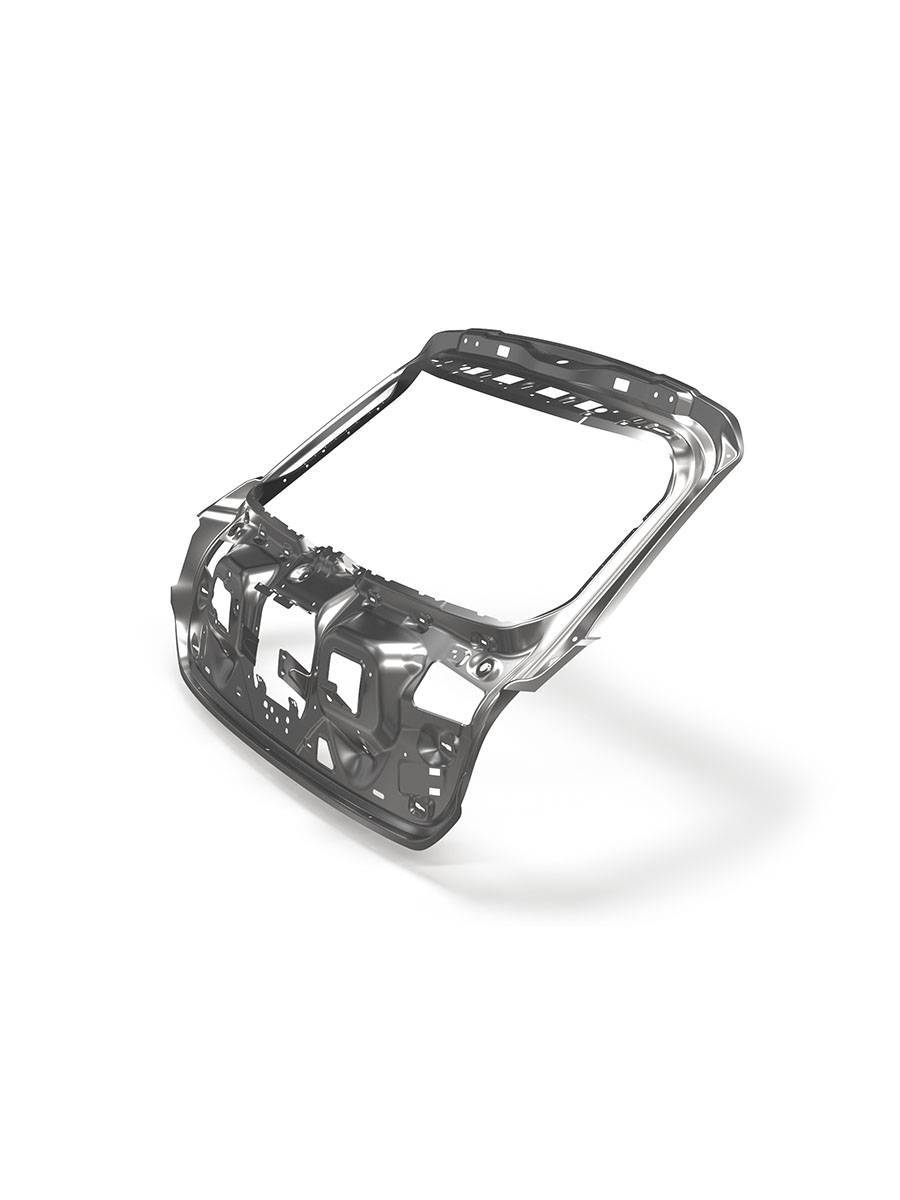
TRUNK FRAME
High quality standard required for this die for aluminium outer skin.
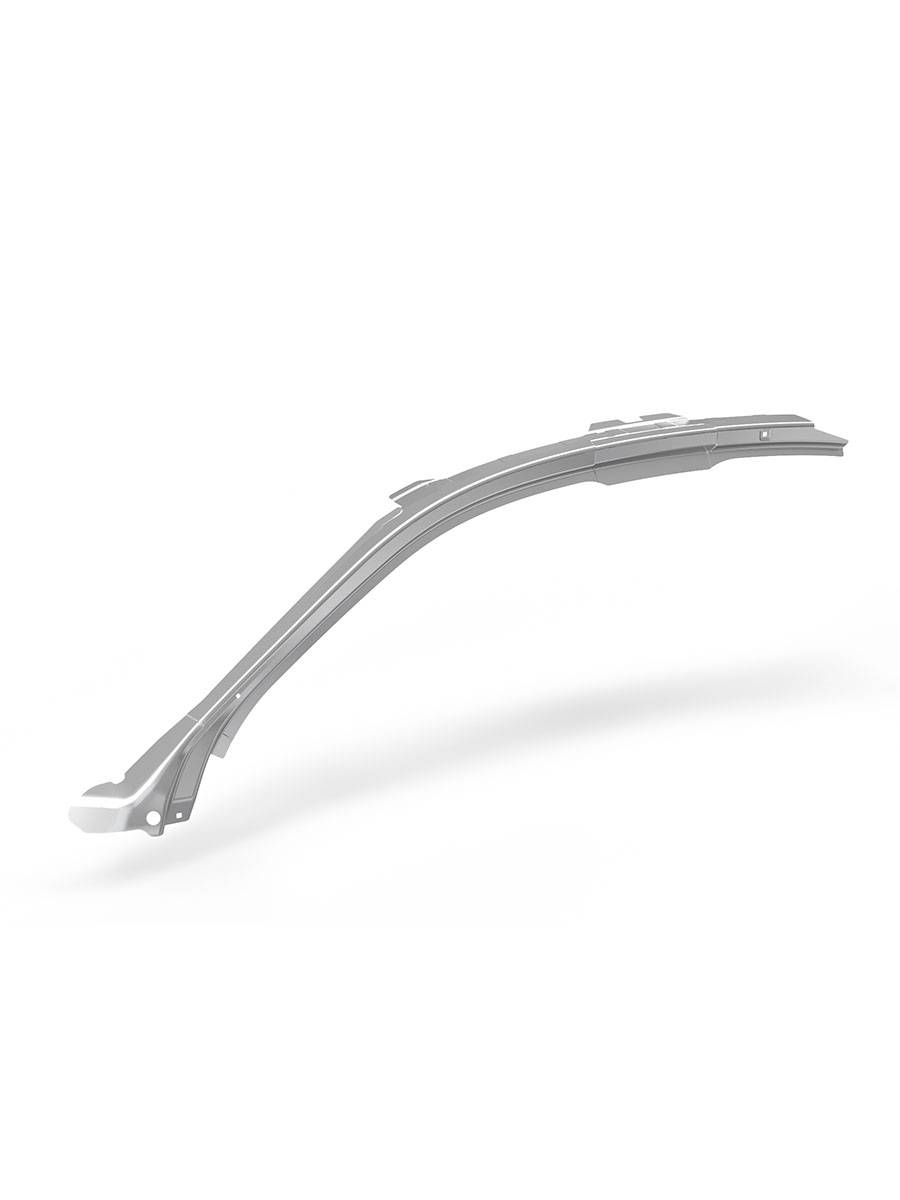
ROOFRAIL REINFOCEMENT
Complex feasibility, Optimization of production with 70% edges definition on the blank
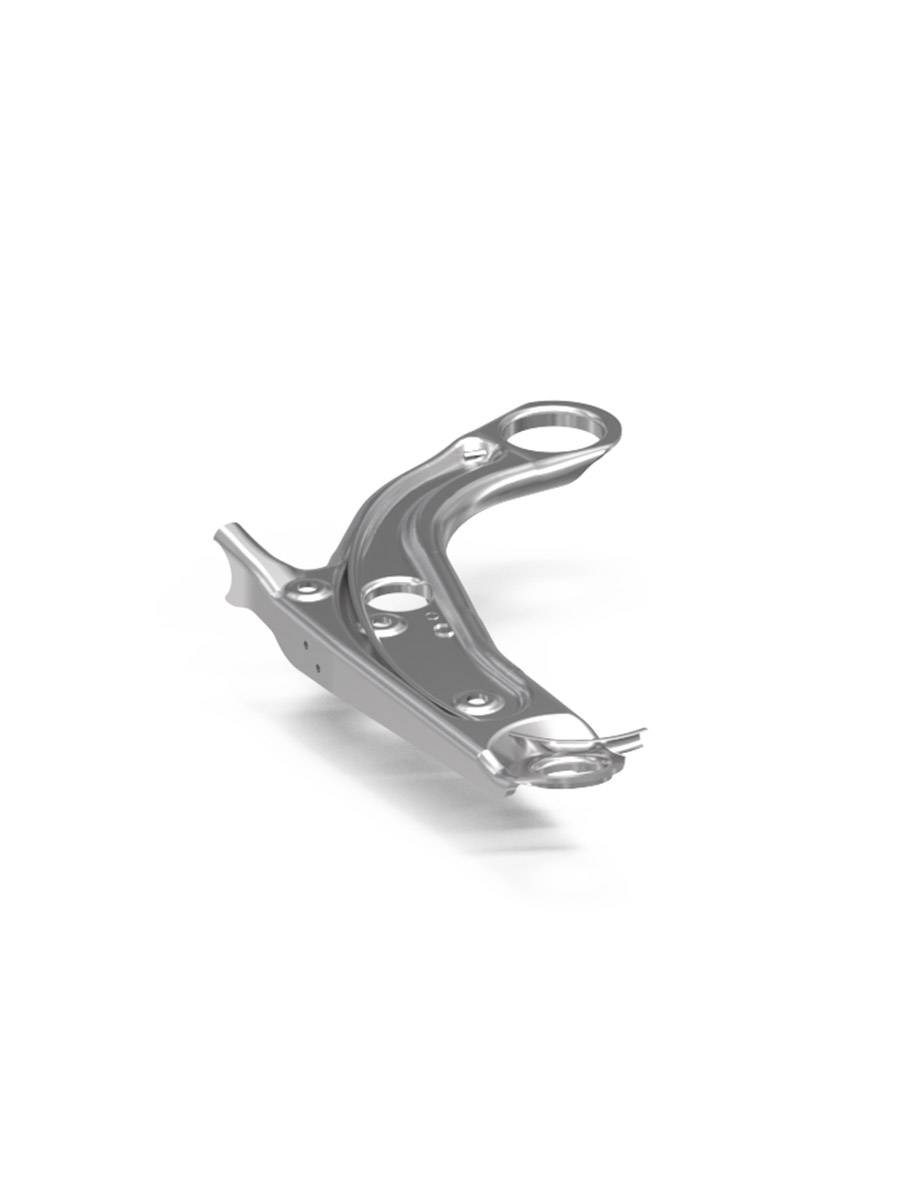
CONTROL ARM
From die casting part to cold formed part. Technical complexity to reach the safety and geometrical standards the OEMs ask.

TUNNEL
Technical complexity due to the springback related to part feasibility
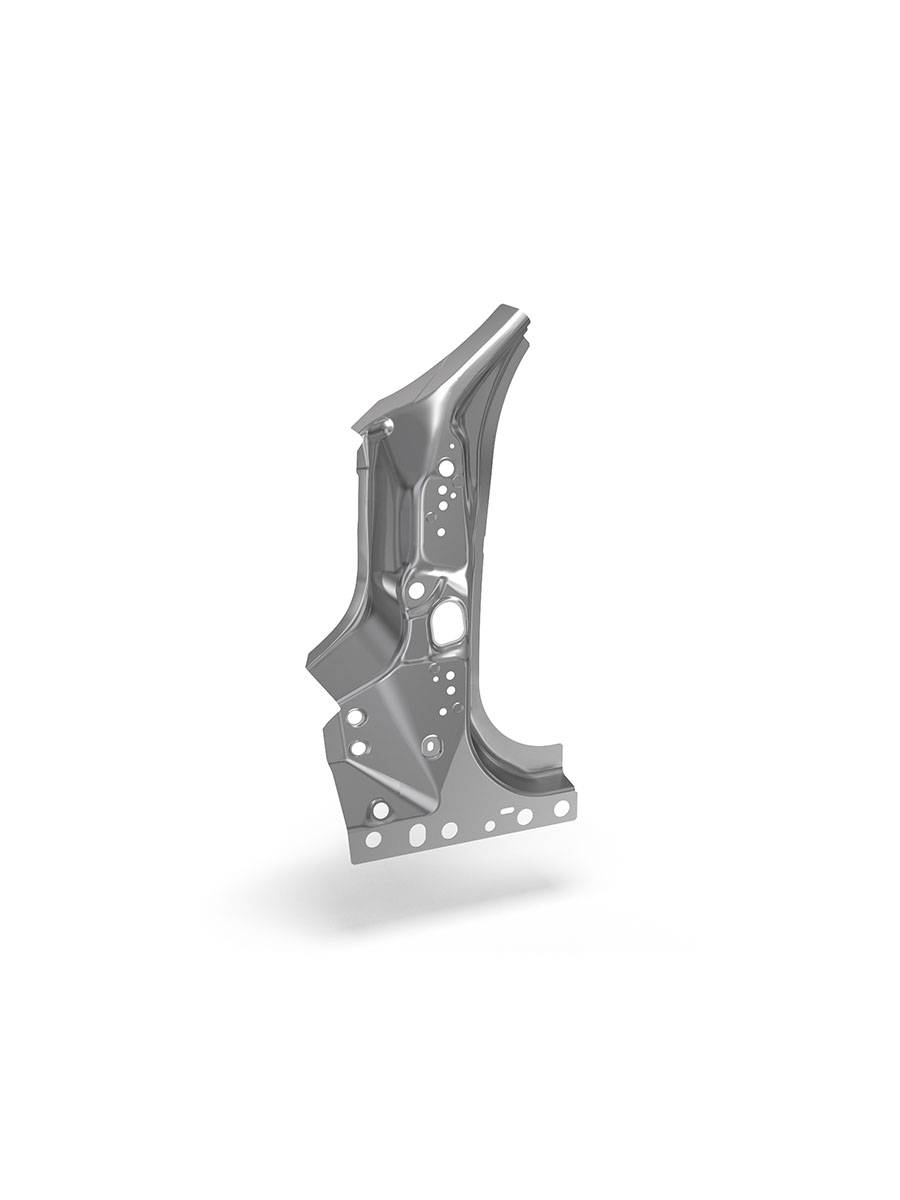
A-PILLAR
Complex feasibility, patches can be added
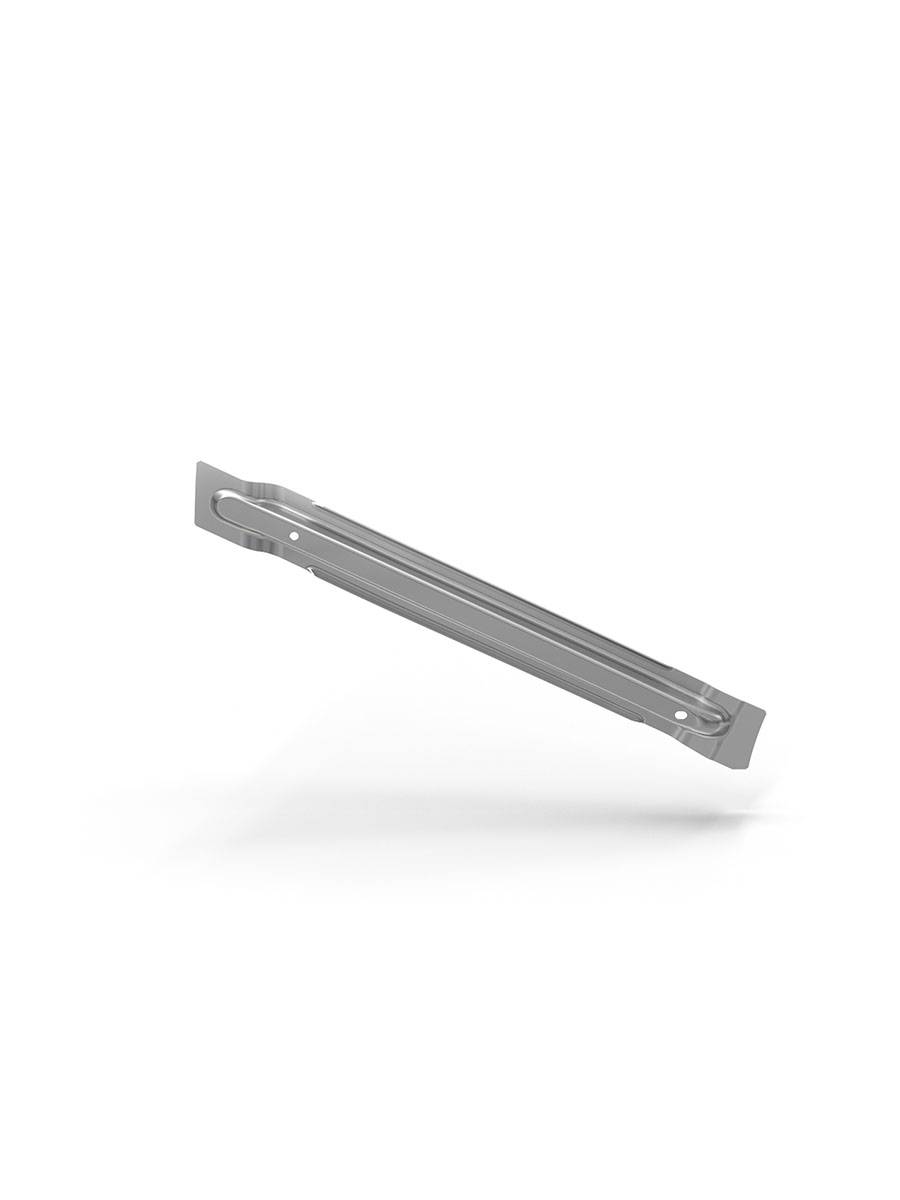
DOOR IMPACT BEAM
Simultaneous forming and piercing of the part
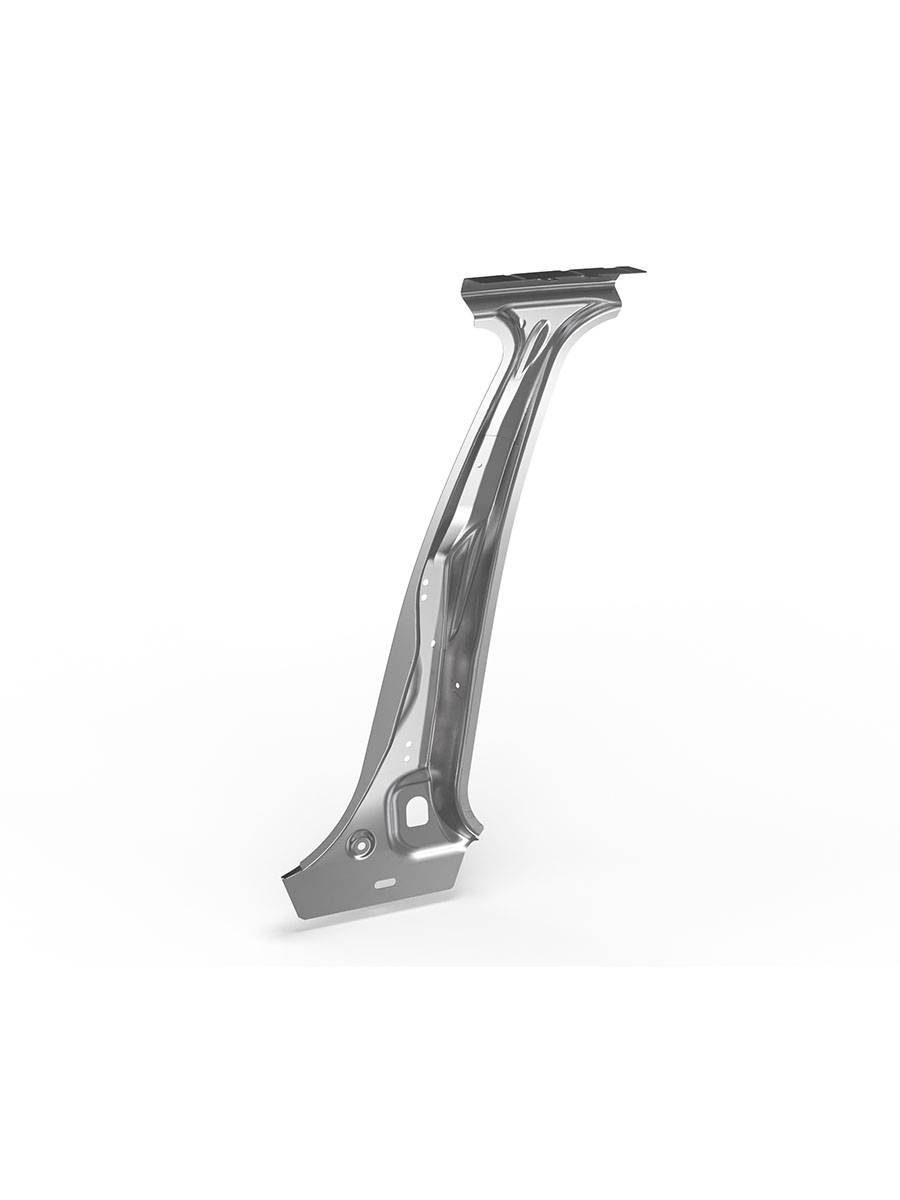
B-PILLAR
Complex feasibility, further technologies can be combined: Tailor Welded Blank TWB, Tailor Rolled Blank TRB, Soft Zone
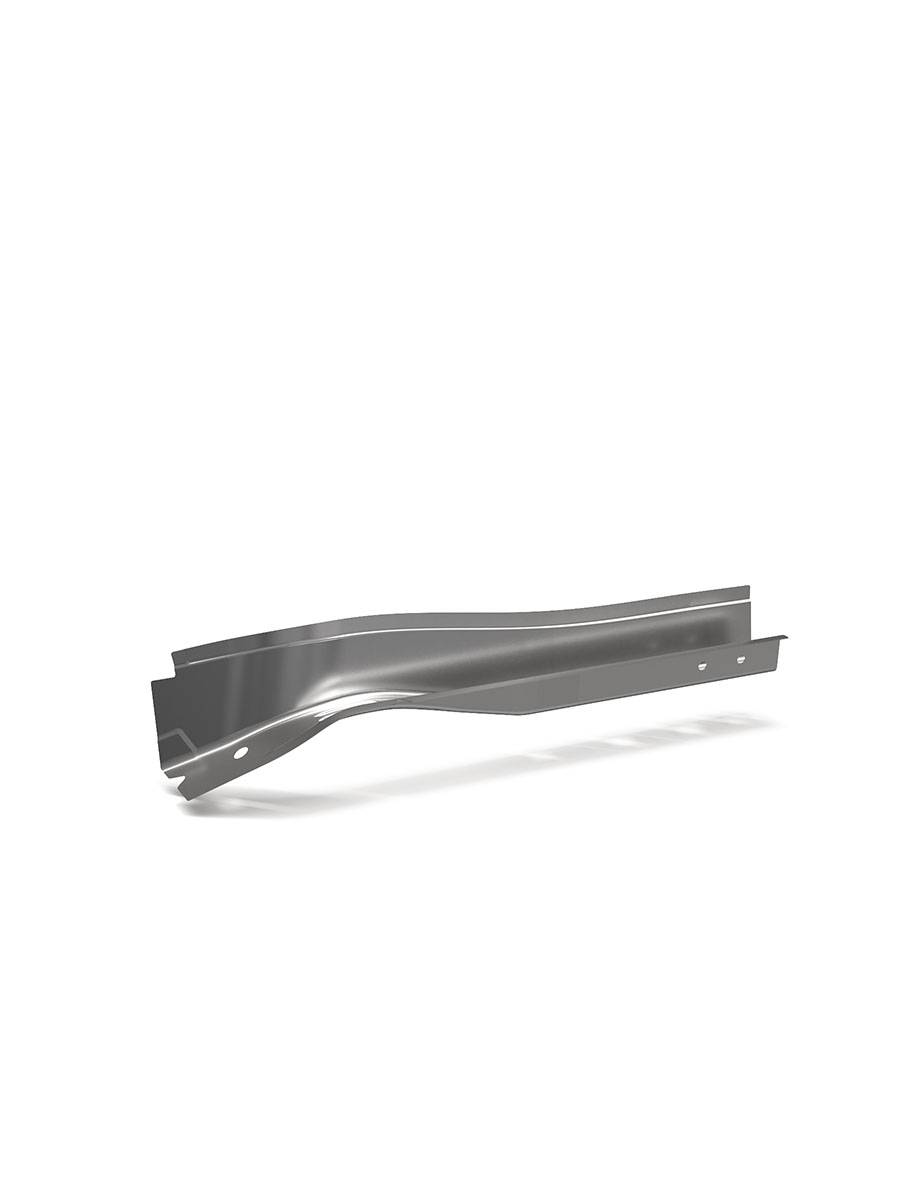
REAR SIDE MEMBER
Multiple technologies can be combined: Tailor Welded Blank TWB, Tailor Rolled Blank TRB
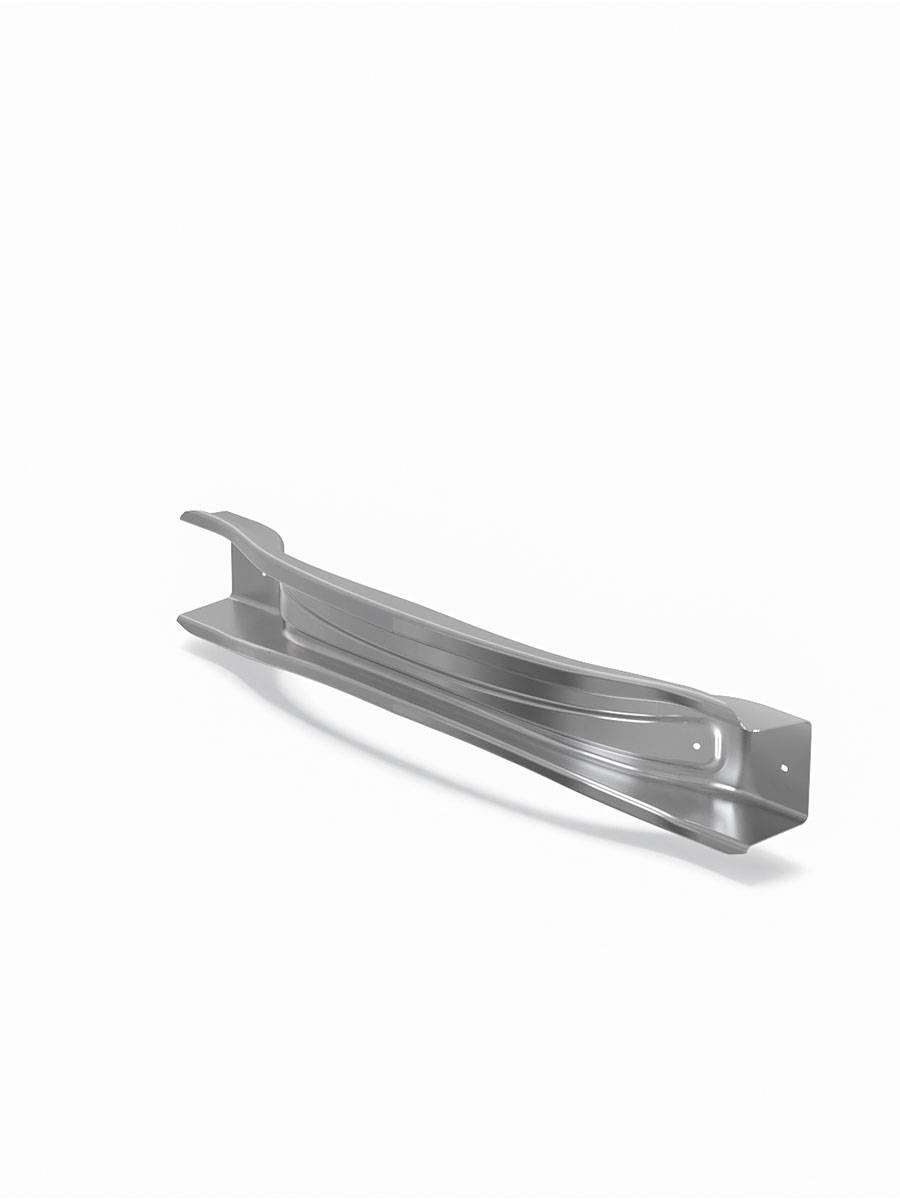
BUMPER
Complex feasibility and predeveloped trim.
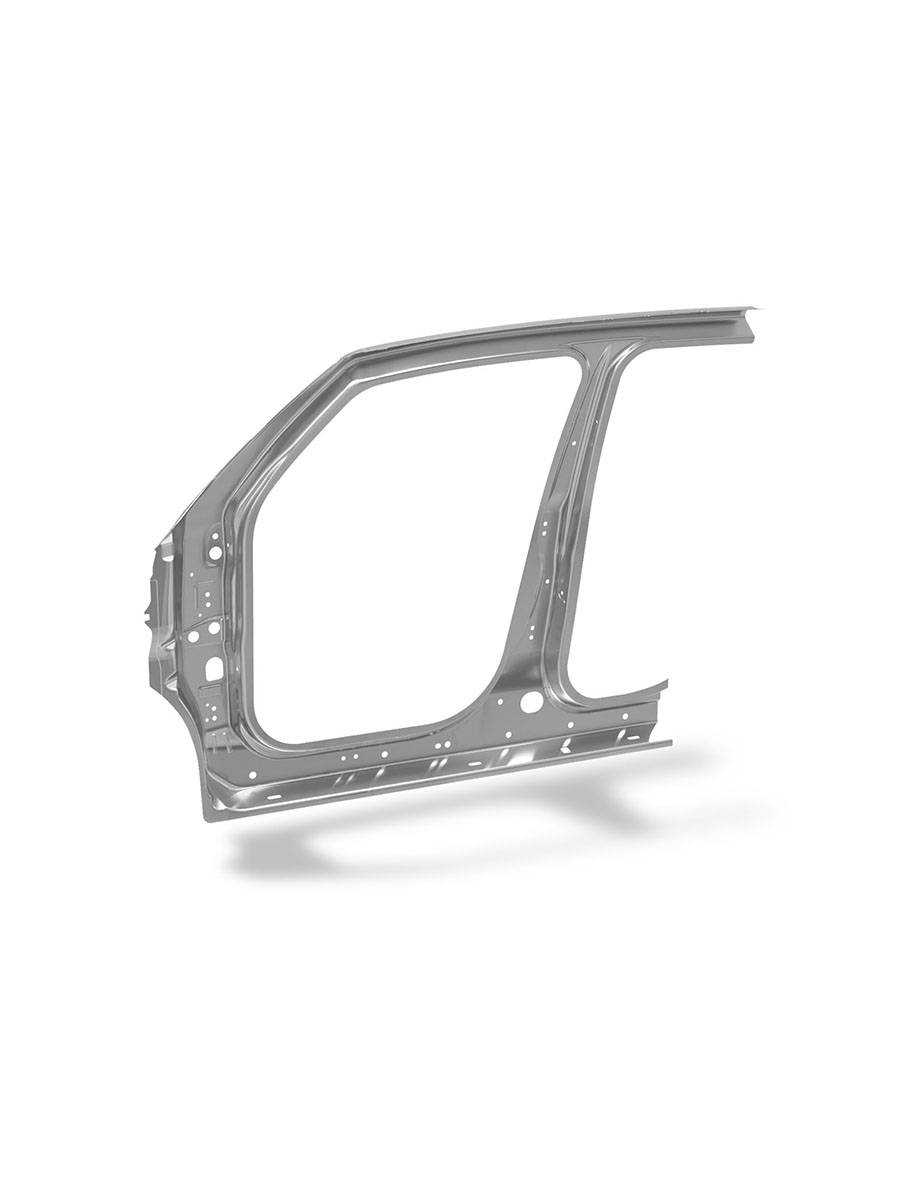
DOOR RING
Outstanding die with major technological impact combining all side parts in only one part.
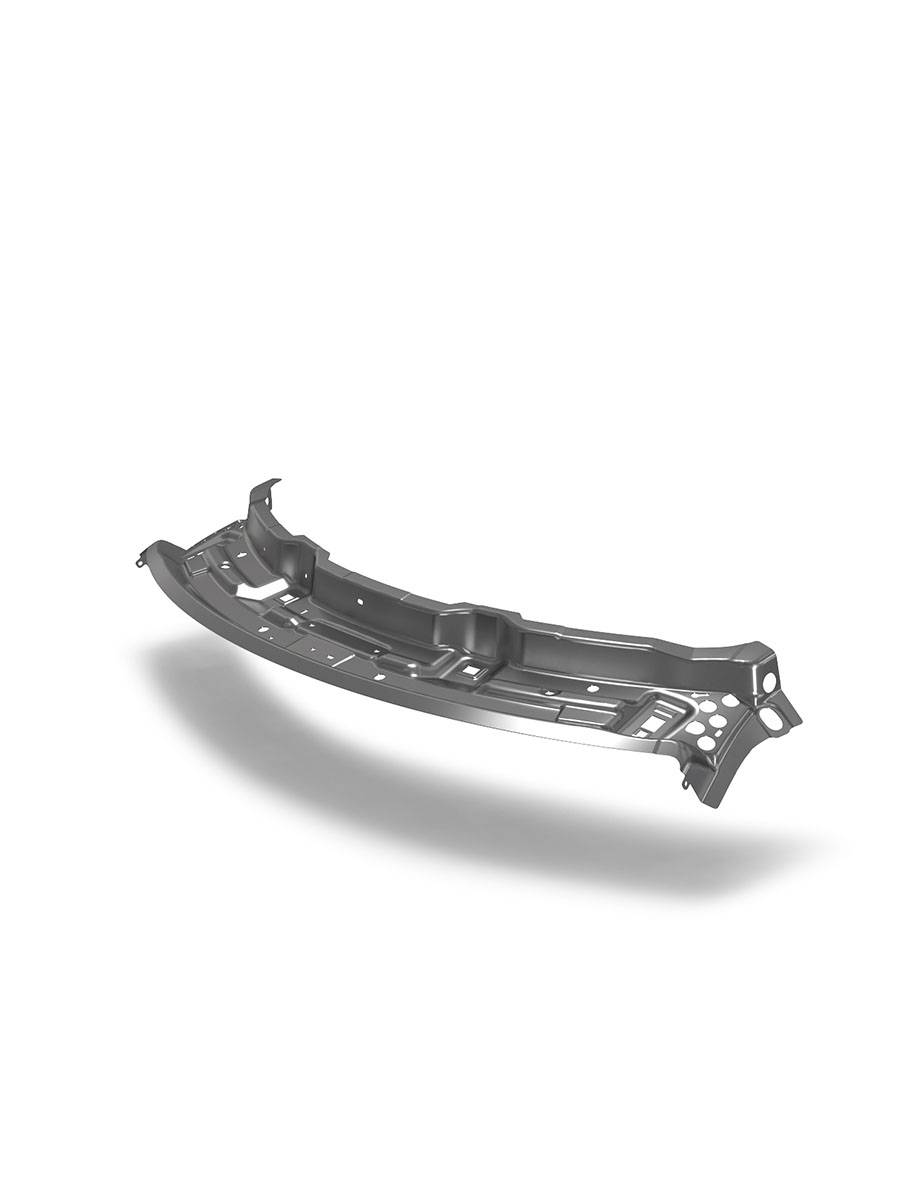
WINDSHIELD REINFORCEMENT
Complex geometry due to the different materials stamped like TWB, TRB, co-stamping with carbon parts.
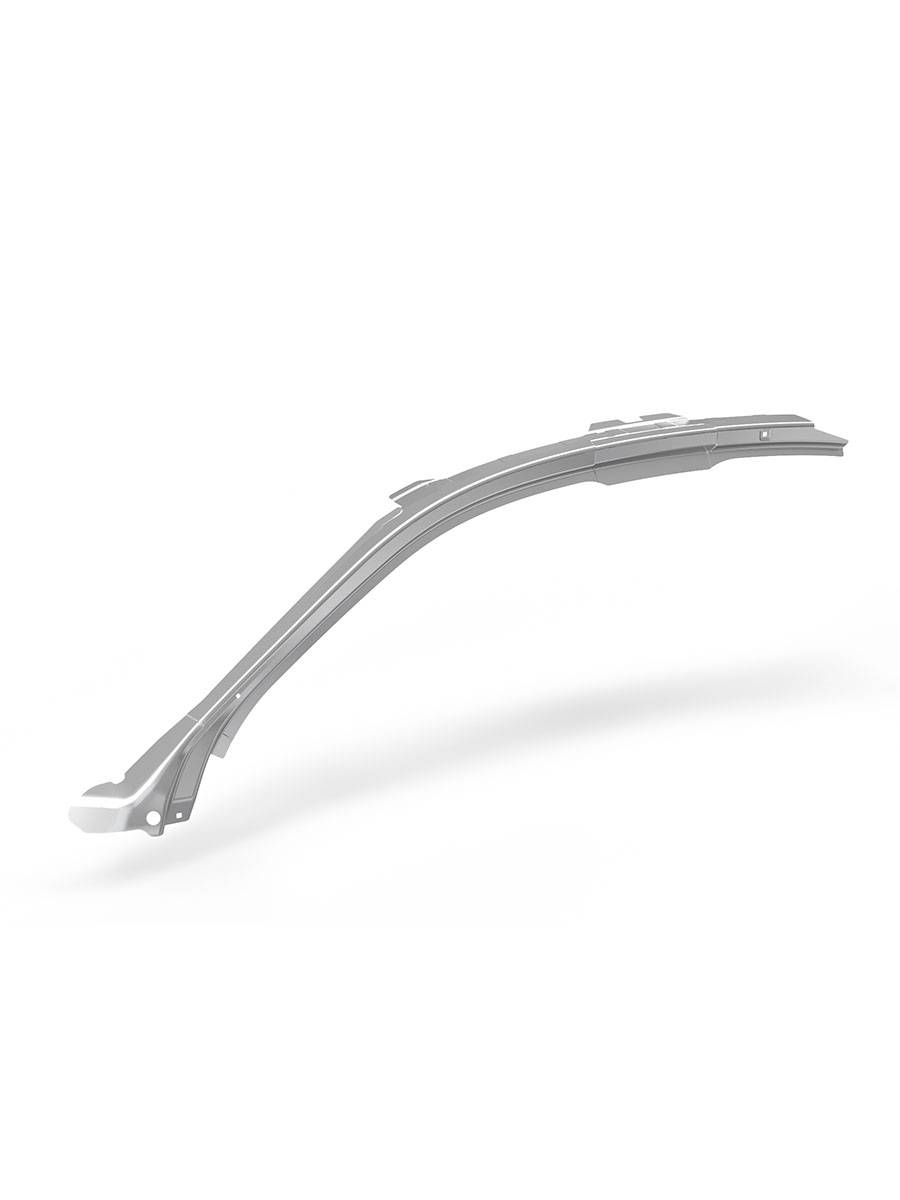
ROOFRAIL REINFOCEMENT
Complex feasibility, Optimization of production with 70% edges definition on the blank
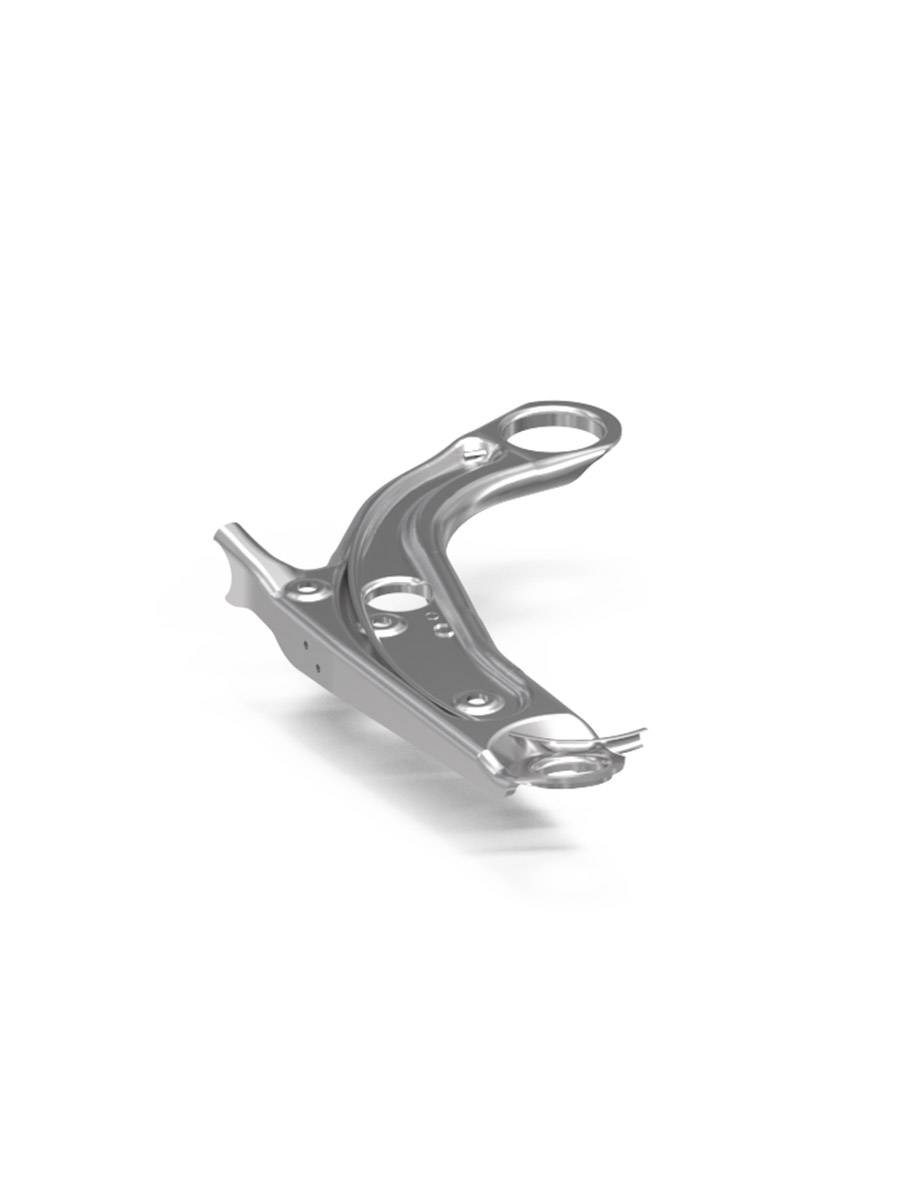
CONTROL ARM
From die casting part to cold formed part. Technical complexity to reach the safety and geometrical standards the OEMs ask.

ROOF FRAME
High quality standard required for this die for aluminium part.
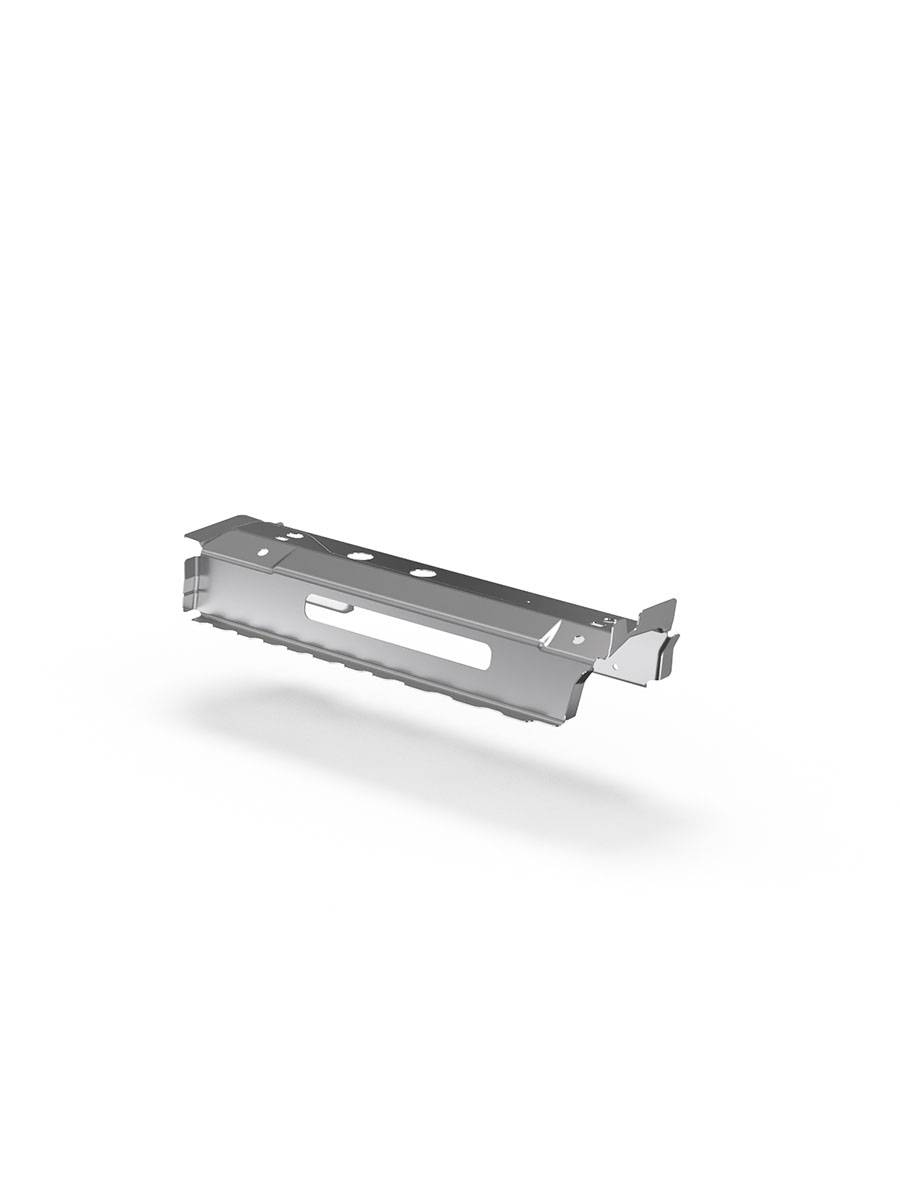
UNDER-SEAT CROSSMEMBER
Part in Ultra-high resistance metal sheet DP1000.
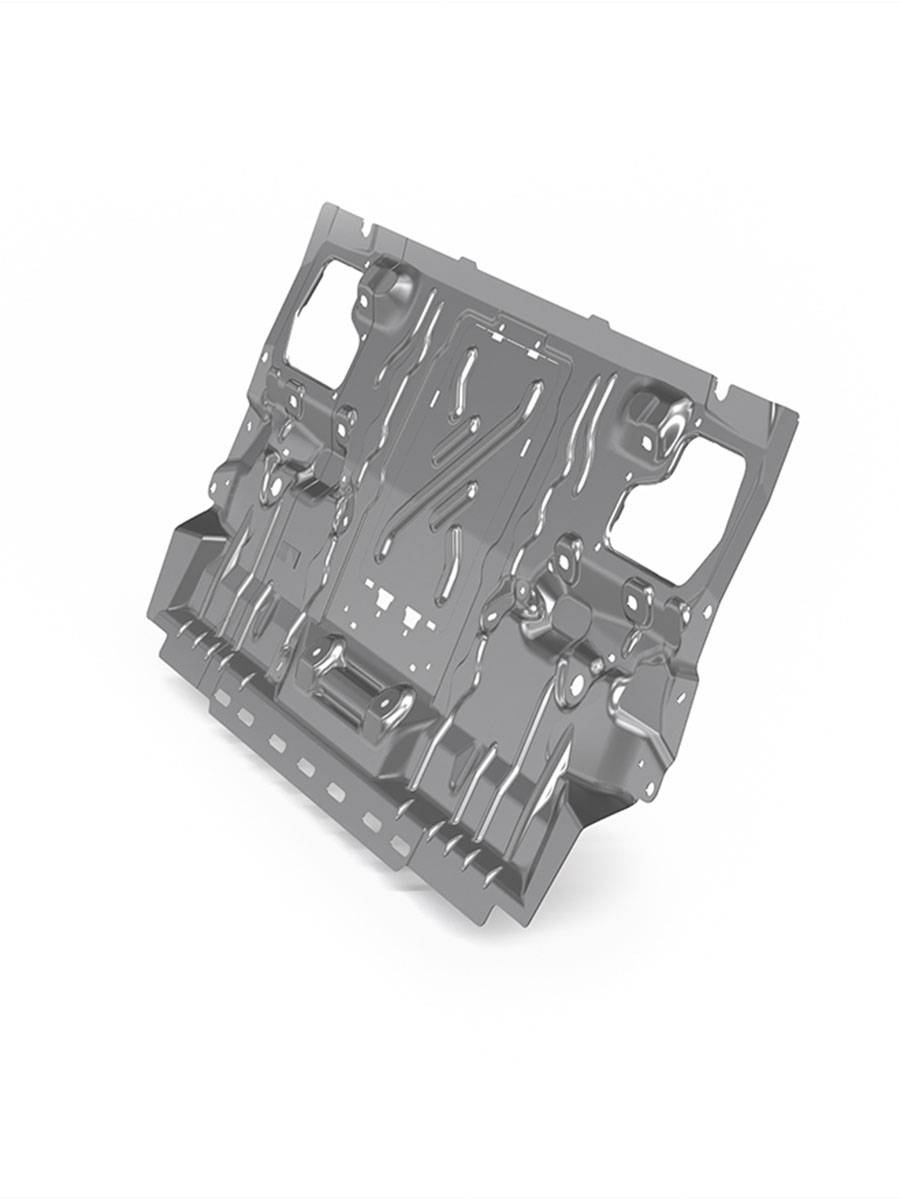
REAR SEAT REINFORCEMENT
Part in TWB. Complex die due to part modularity: interchangeable trimming to implement ski box.
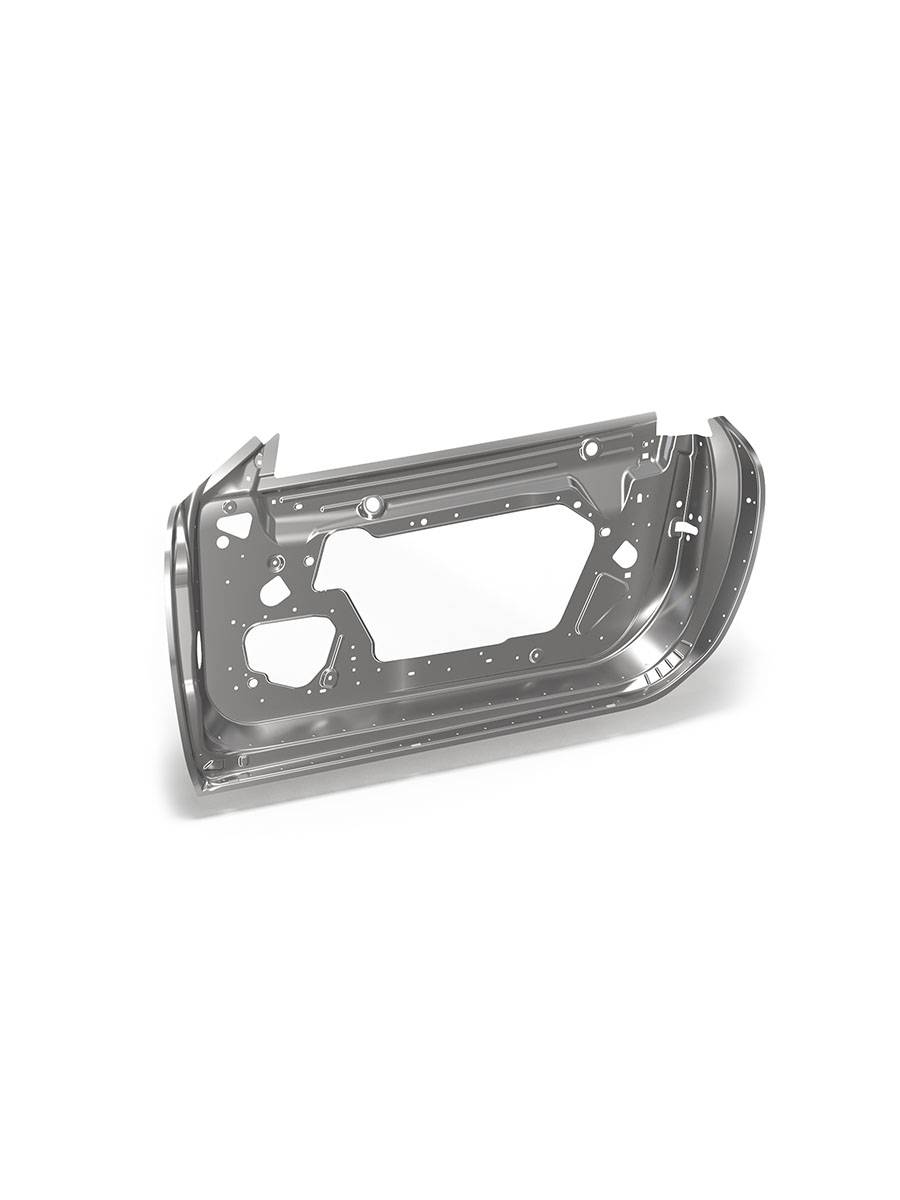
FRONT DOOR FRAME
High quality standard required for this die for aluminium inner frame combined with outer skin.
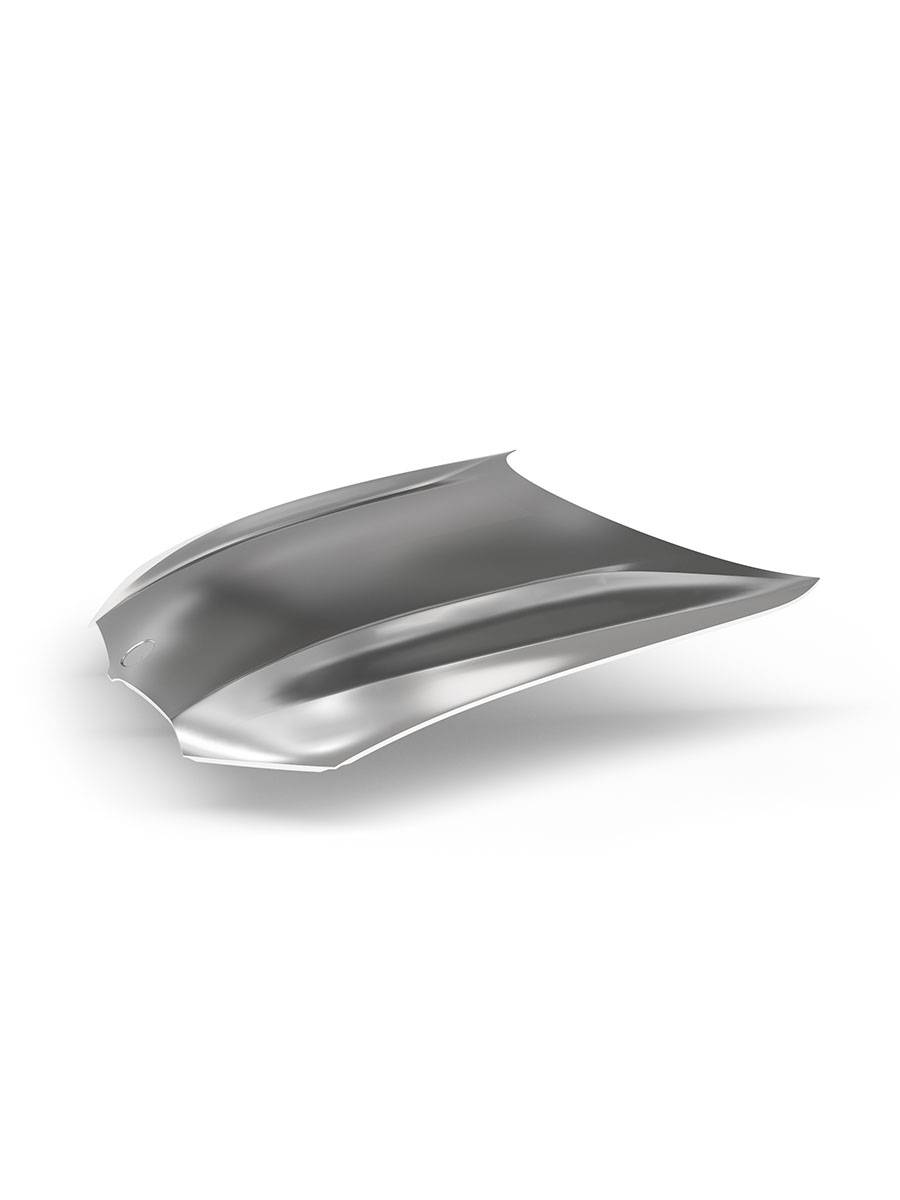
FRONT HOOD PANEL
High quality standard required for this die for outer skin in aluminium sheet.
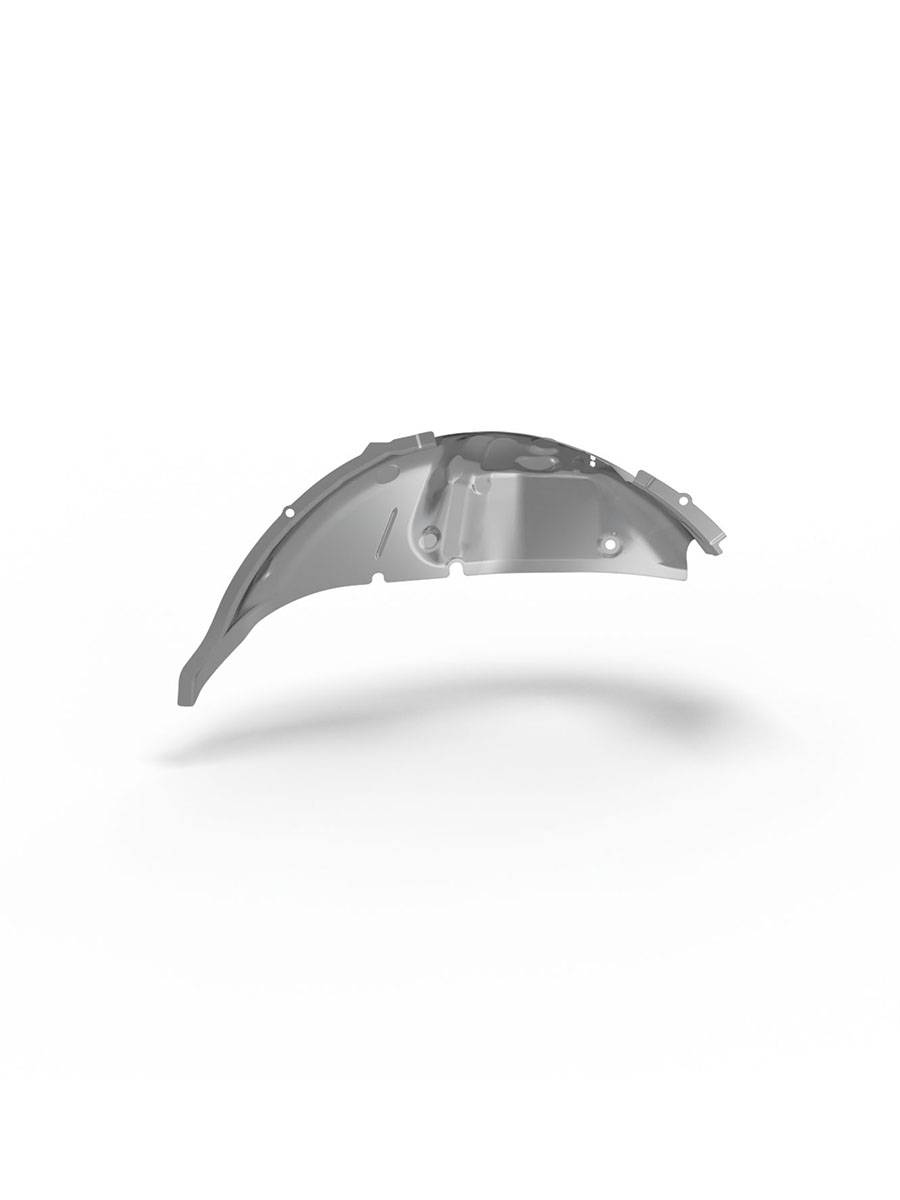
WHEEL ARCH REAR
High quality standard required for this die
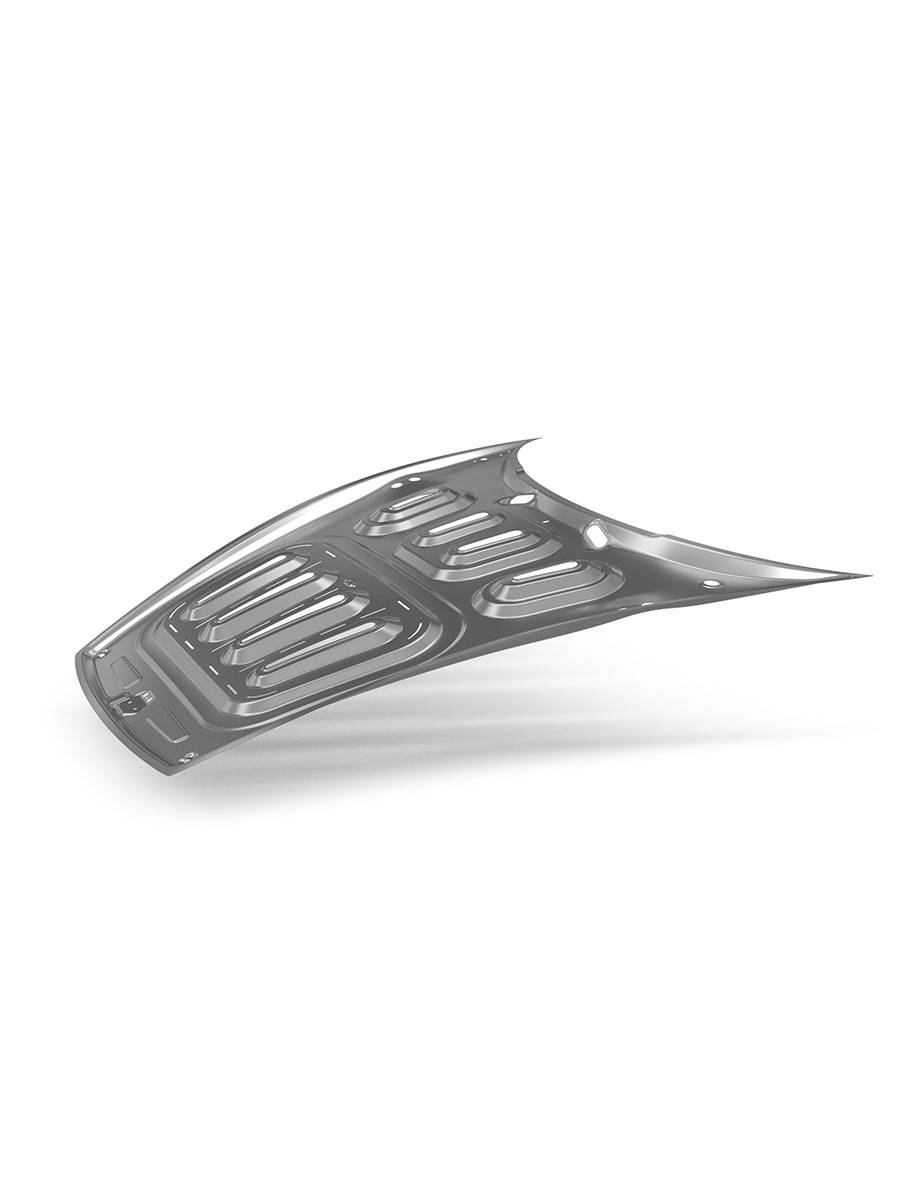
FRONT HOOD FRAME
High quality standard required for this die.
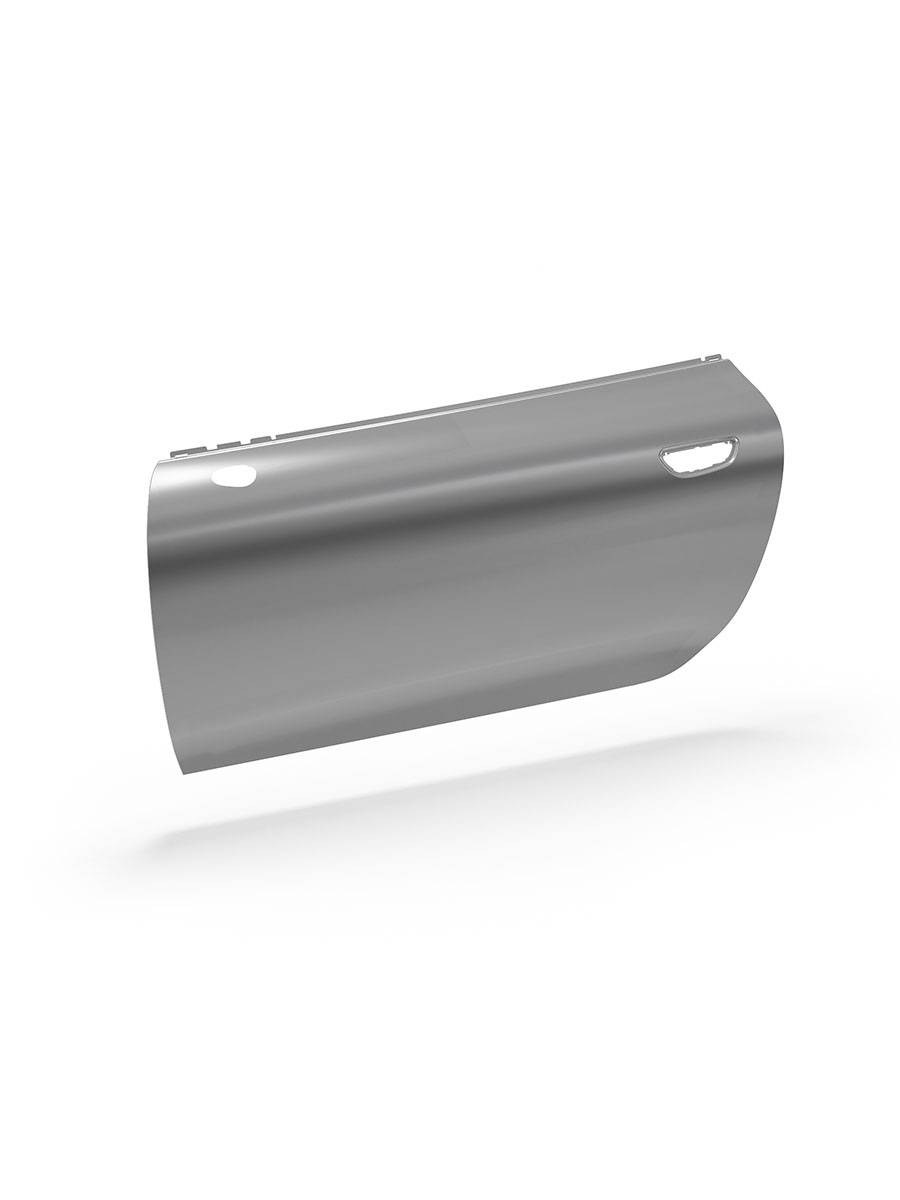
DOOR PANEL
Outer skin in aluminium sheet, high quality standard required for this die.
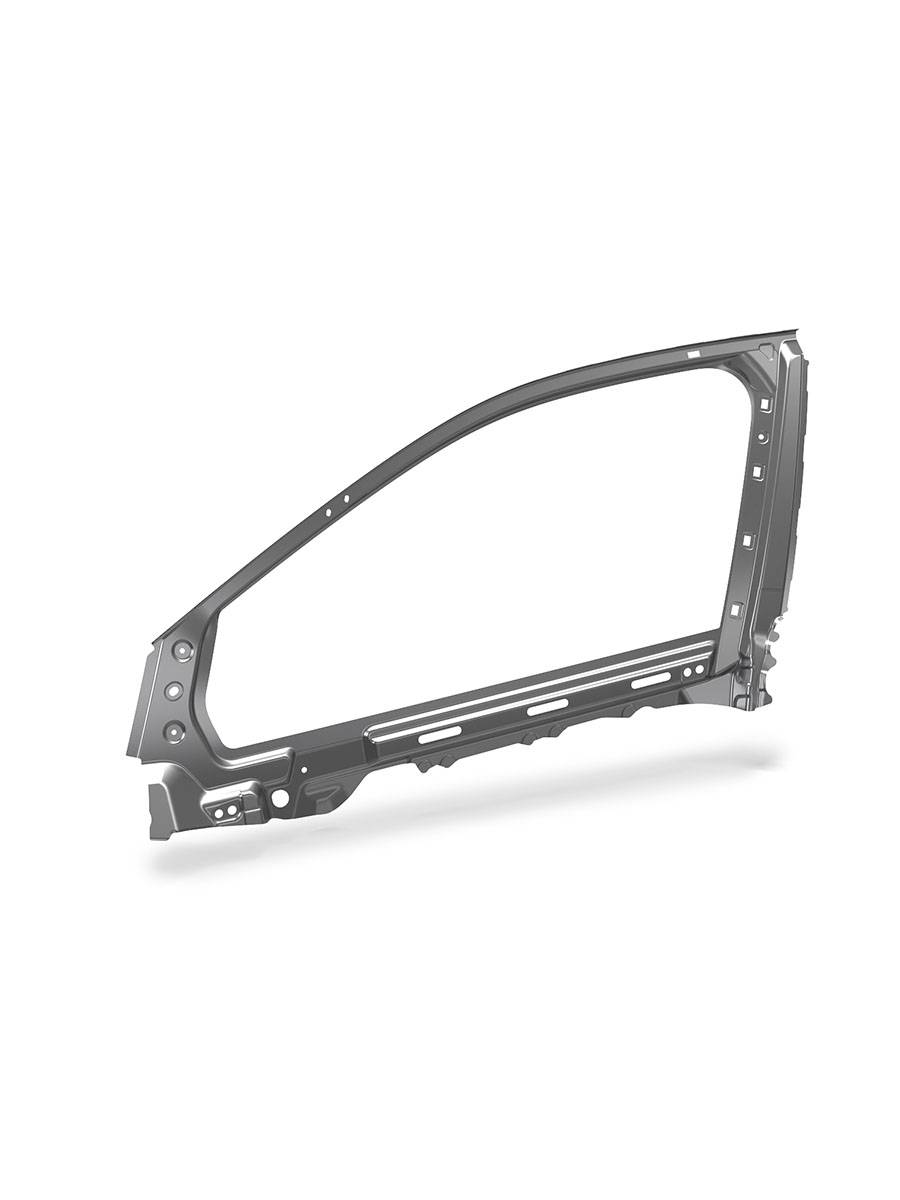
FRONT WINDOW FRAME
Part stamping is complex due to insert/insertion of standard part and nuts.
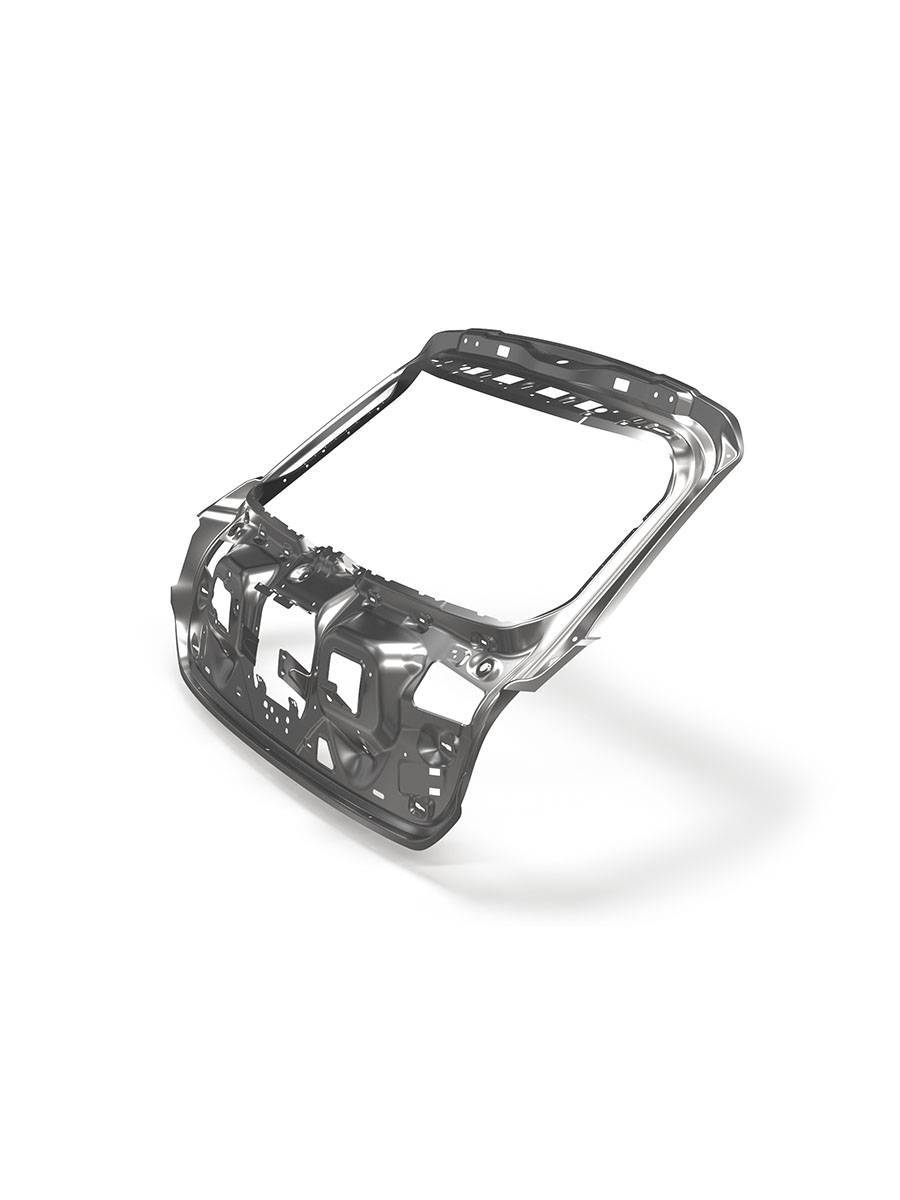
TRUNK FRAME
High quality standard required for this die for aluminium outer skin.