Solutions
DIES FOR COLD FORMING
METAL UNDER CONTROL FOR OVER 30 YEARS
Cold forming represents tradition here in Susta. This activity has enabled us to finalize important projects for many world car manufacturers. Metal sheet is a part of the DNA of the Company, which combines the deep knowledge of its characteristics and potentiality with the proven technical expertise of metal work through processes as cutting, drawing, piercing and flanging.
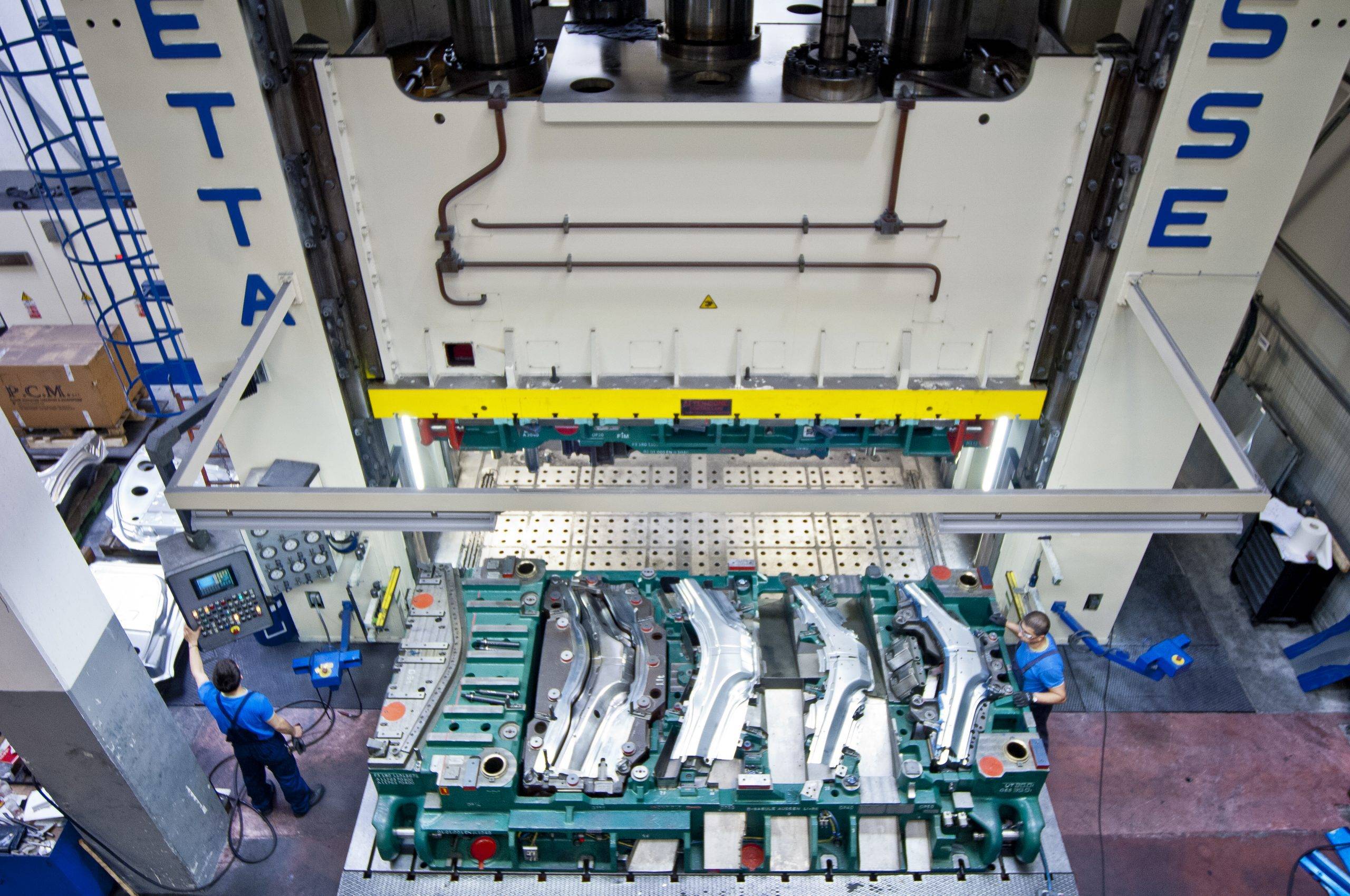
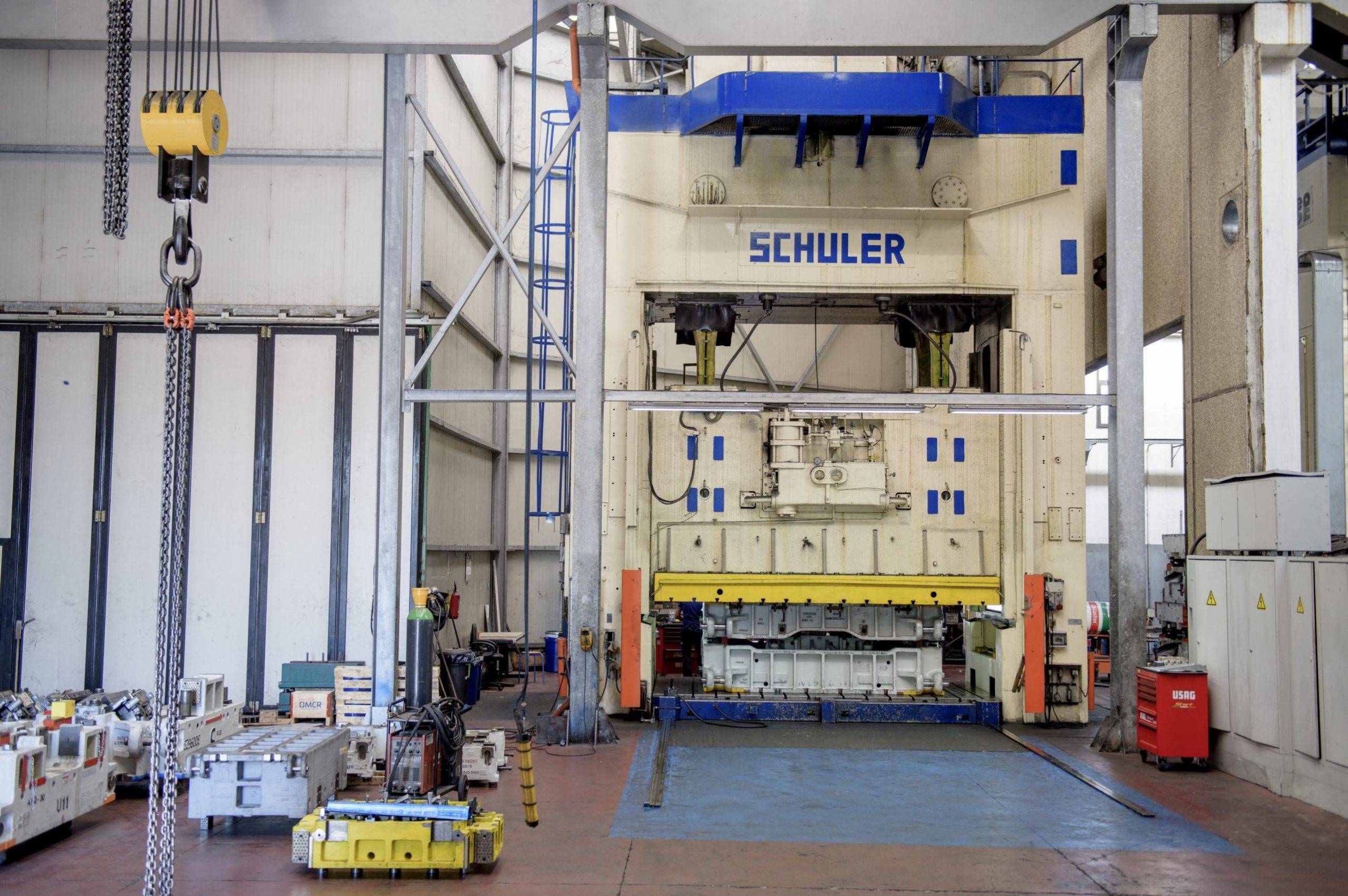
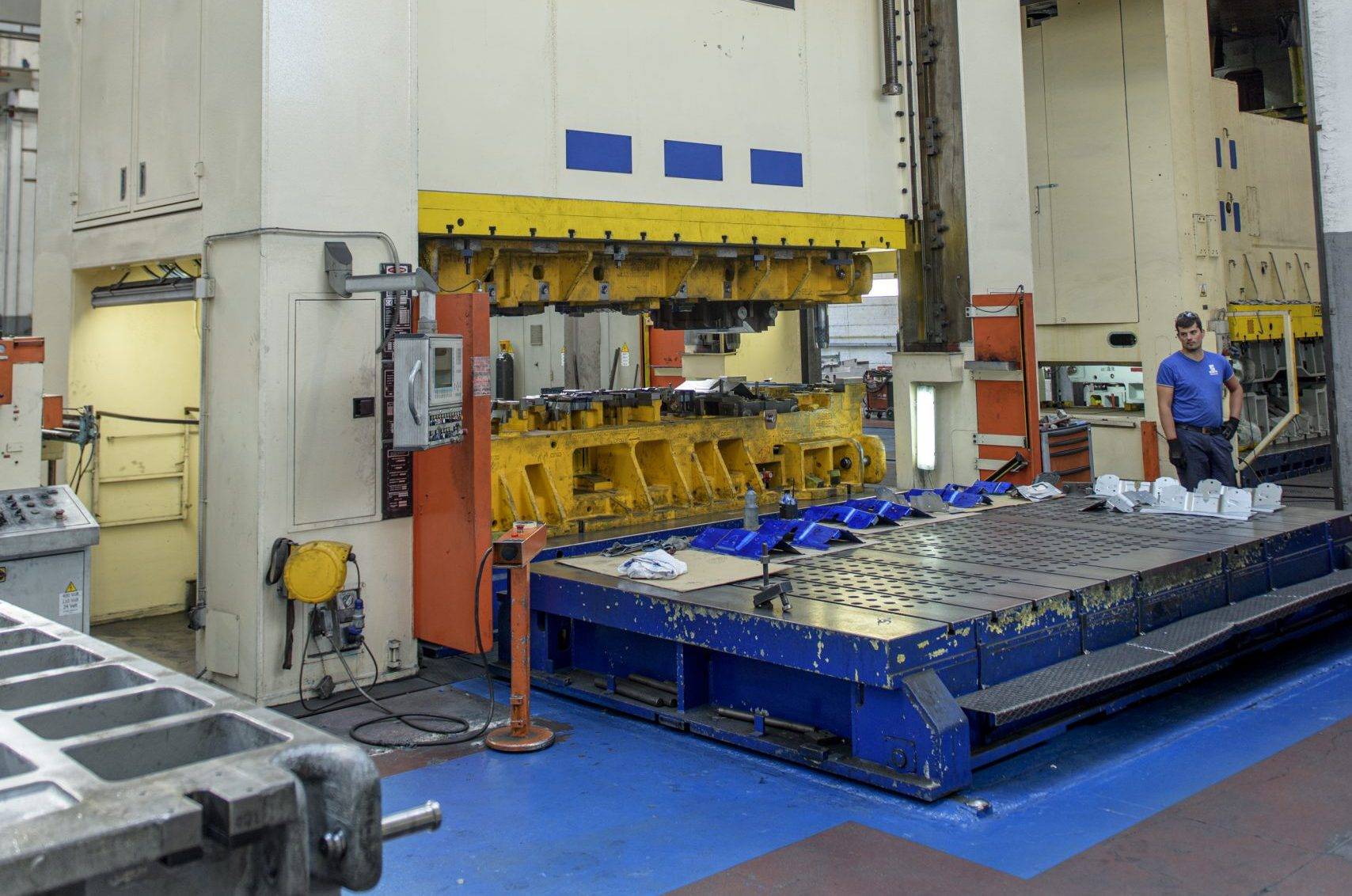

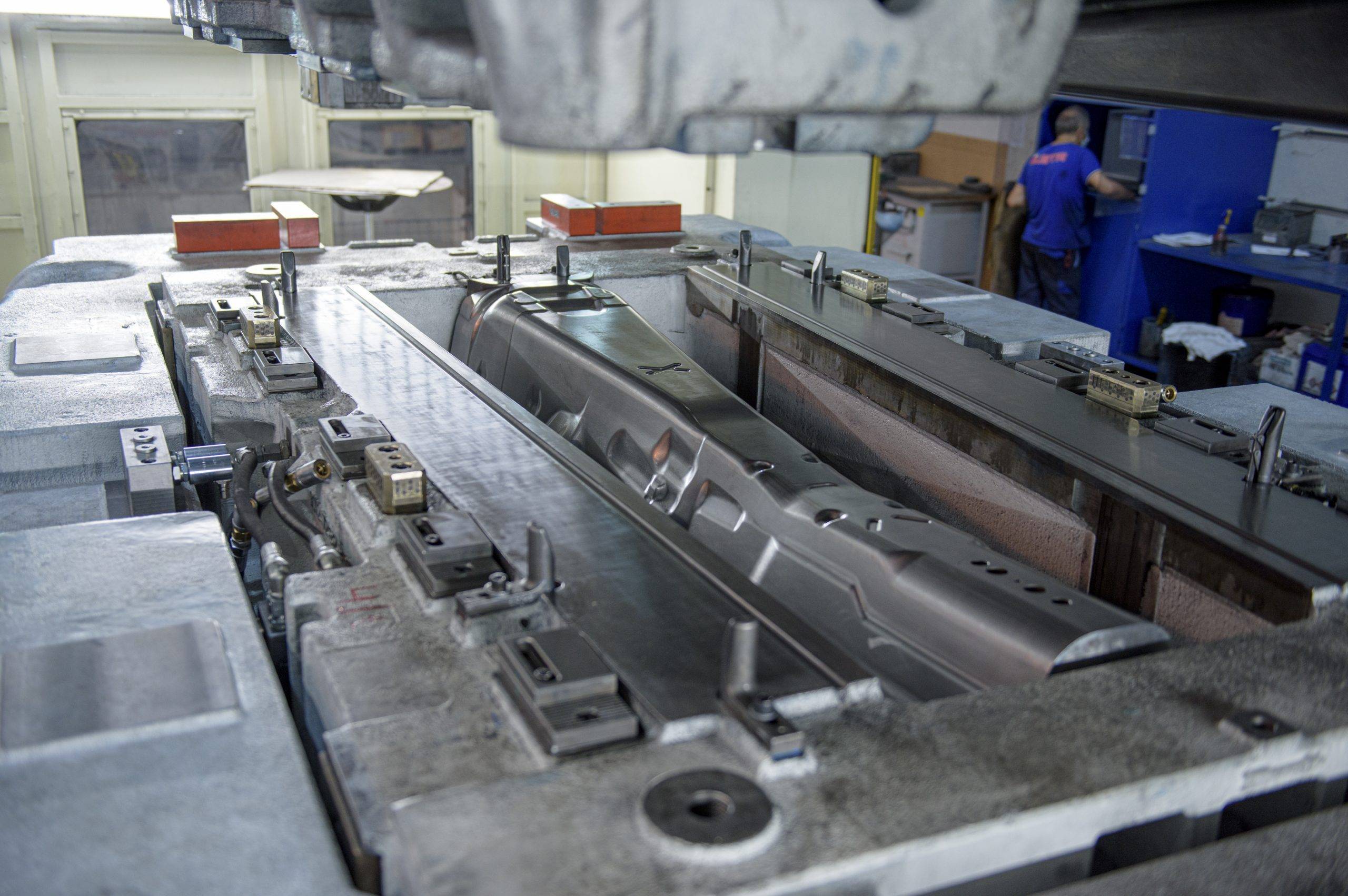
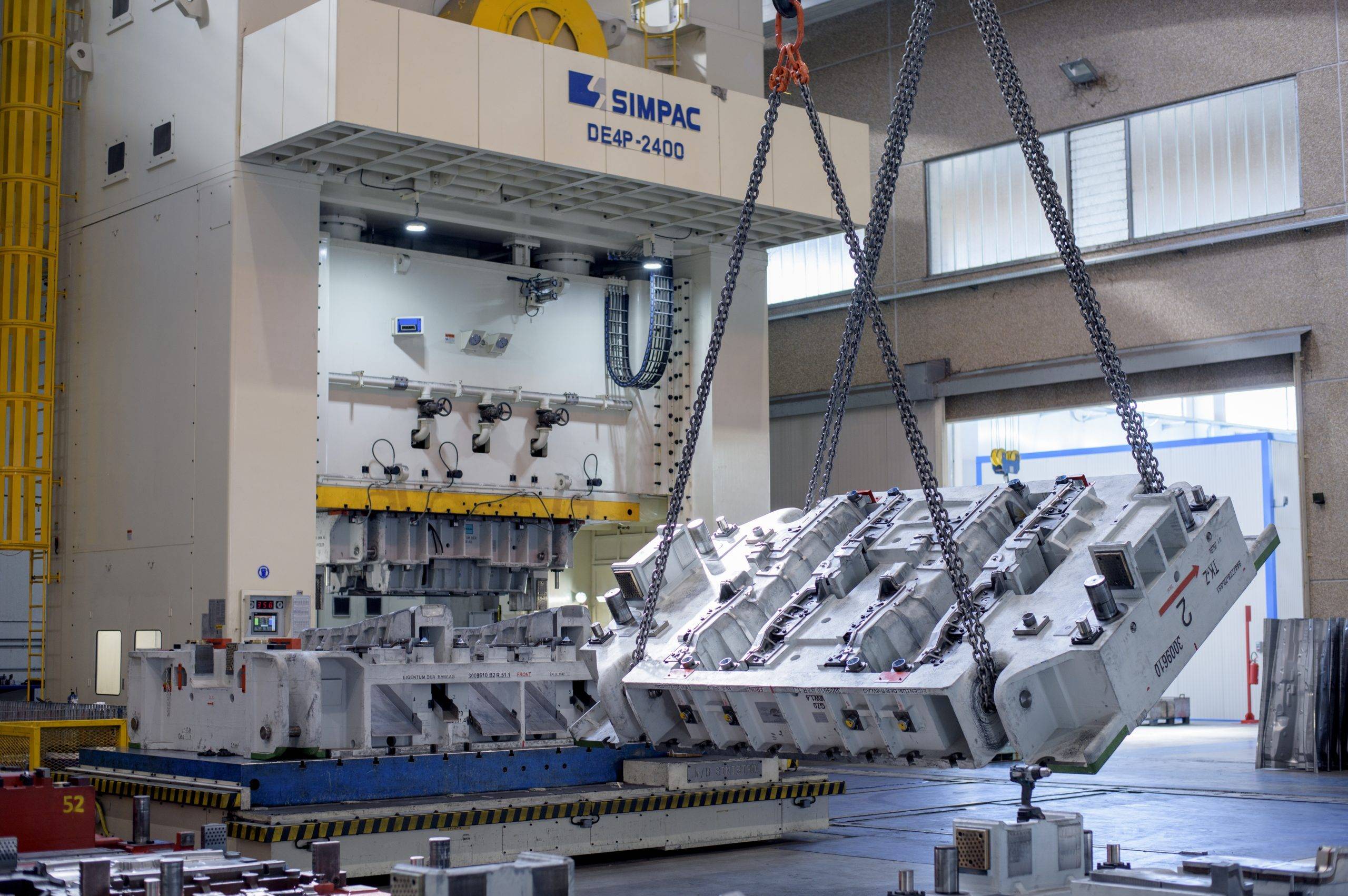
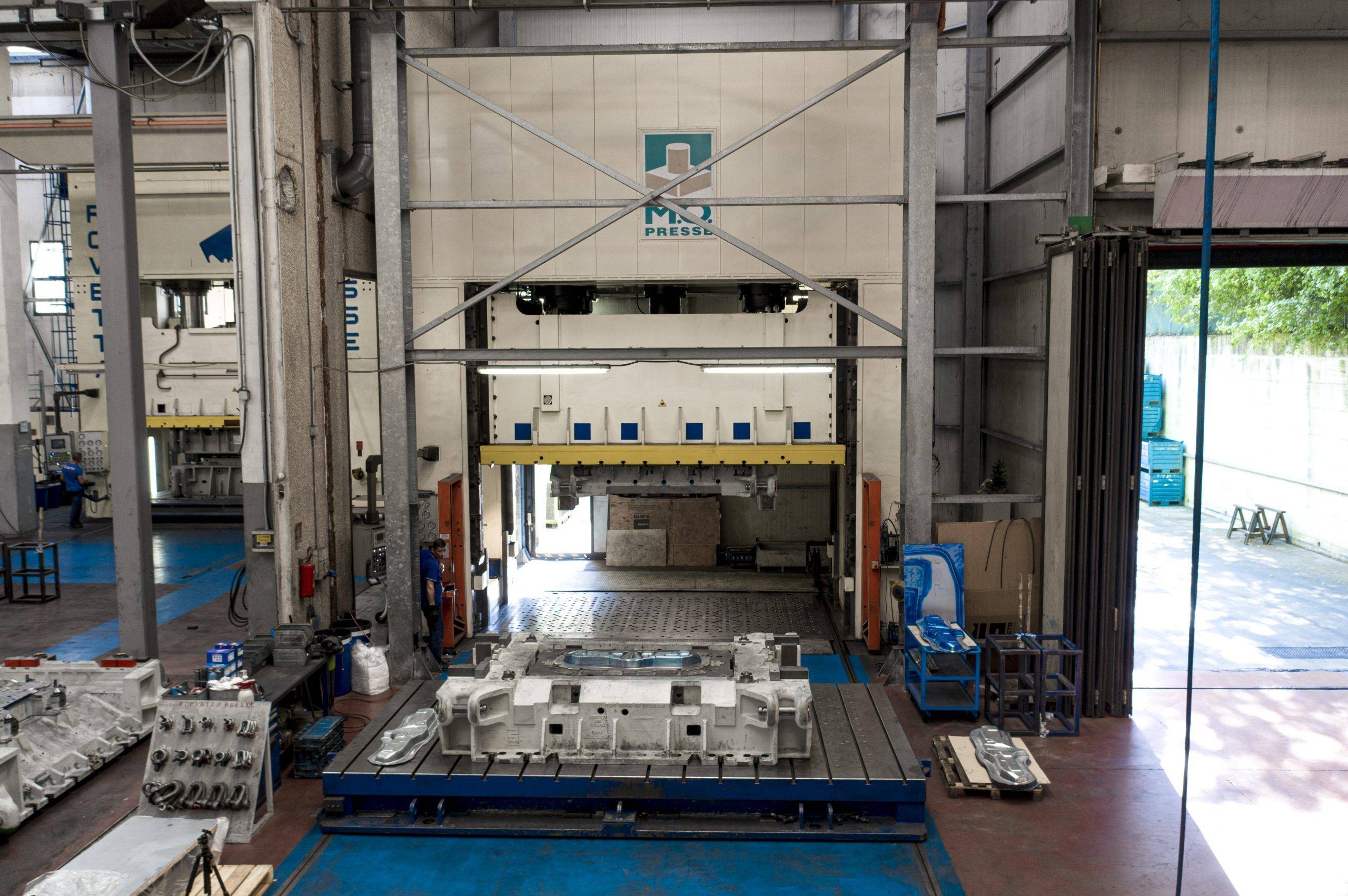
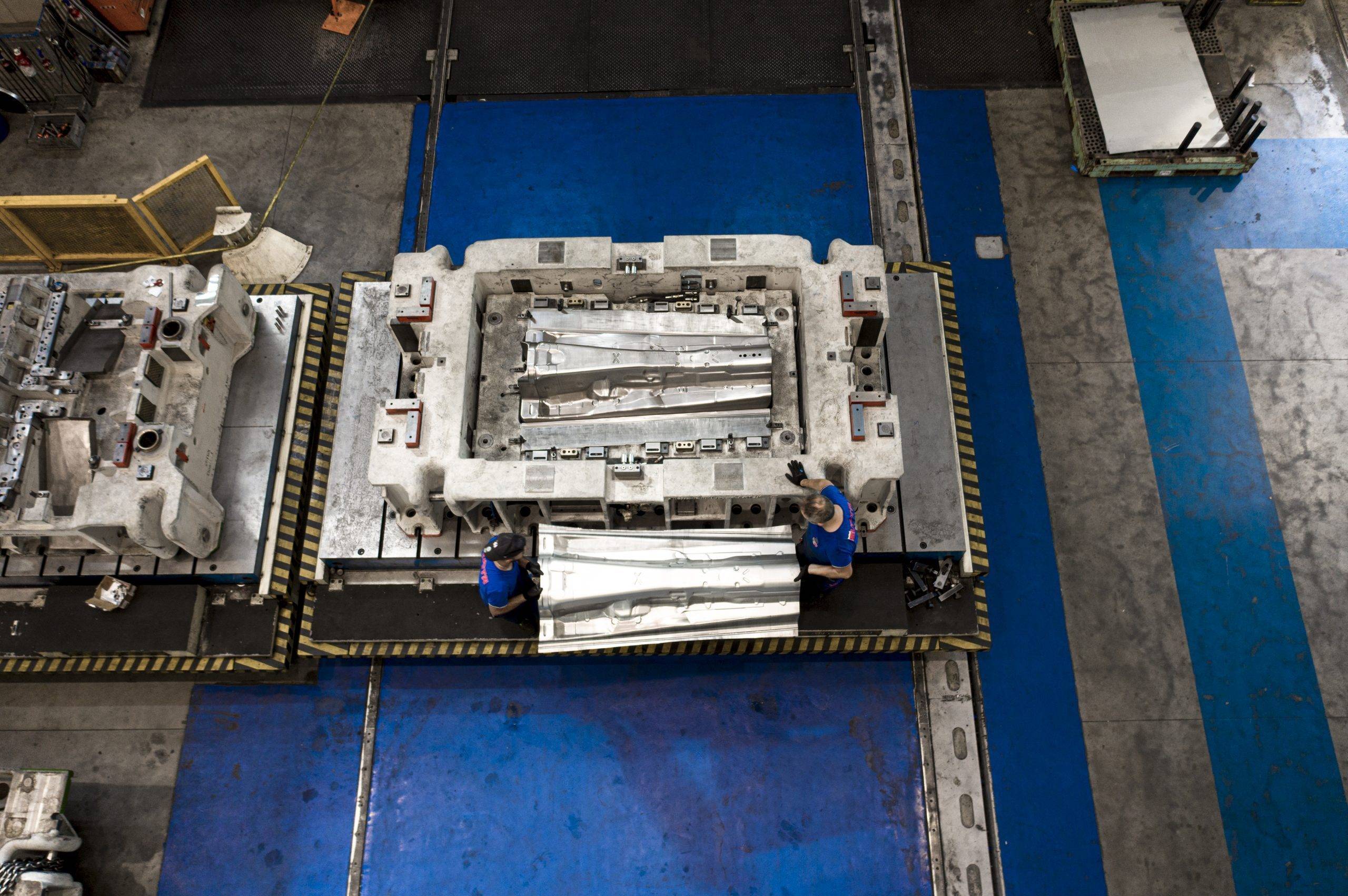
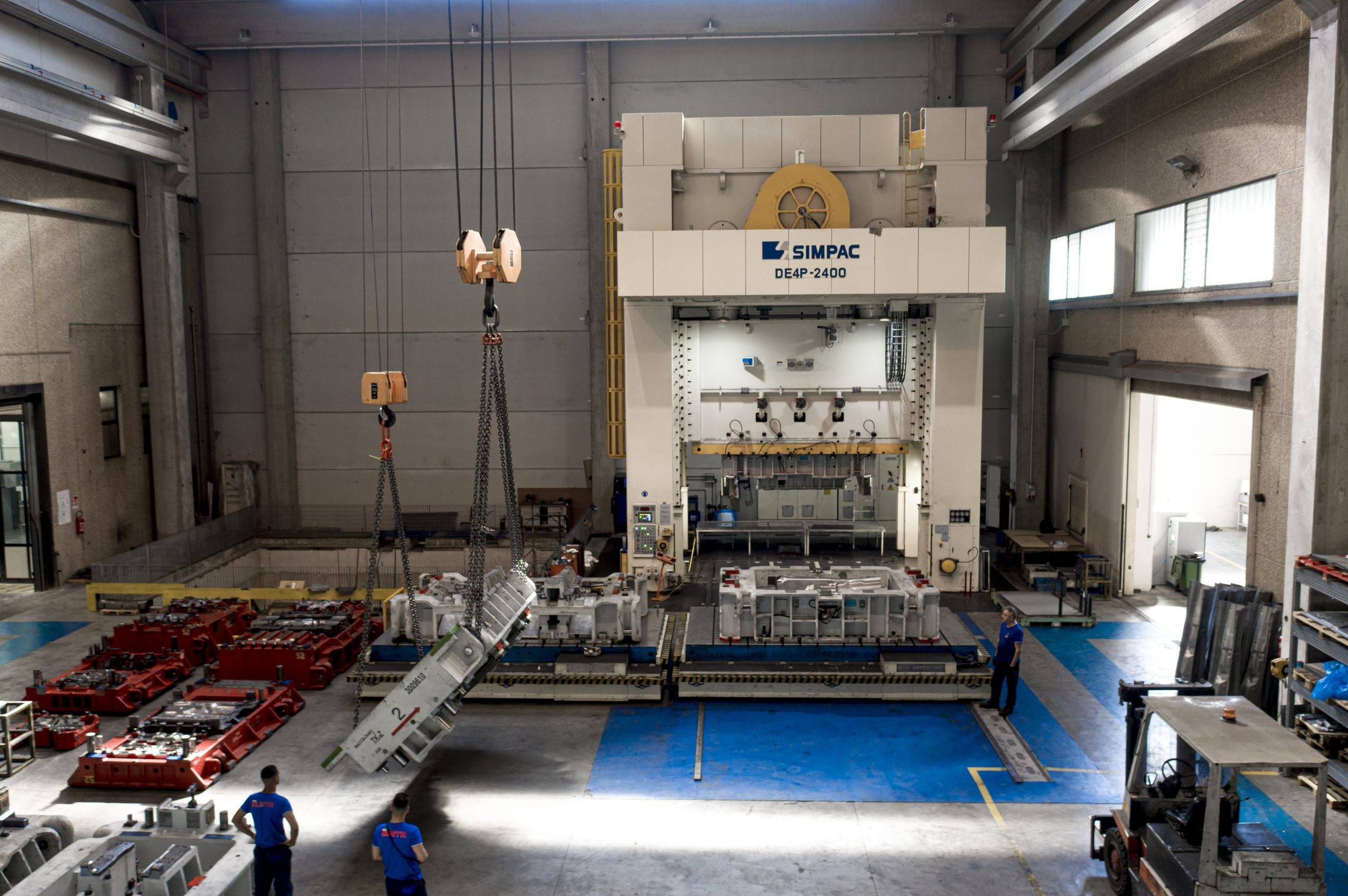
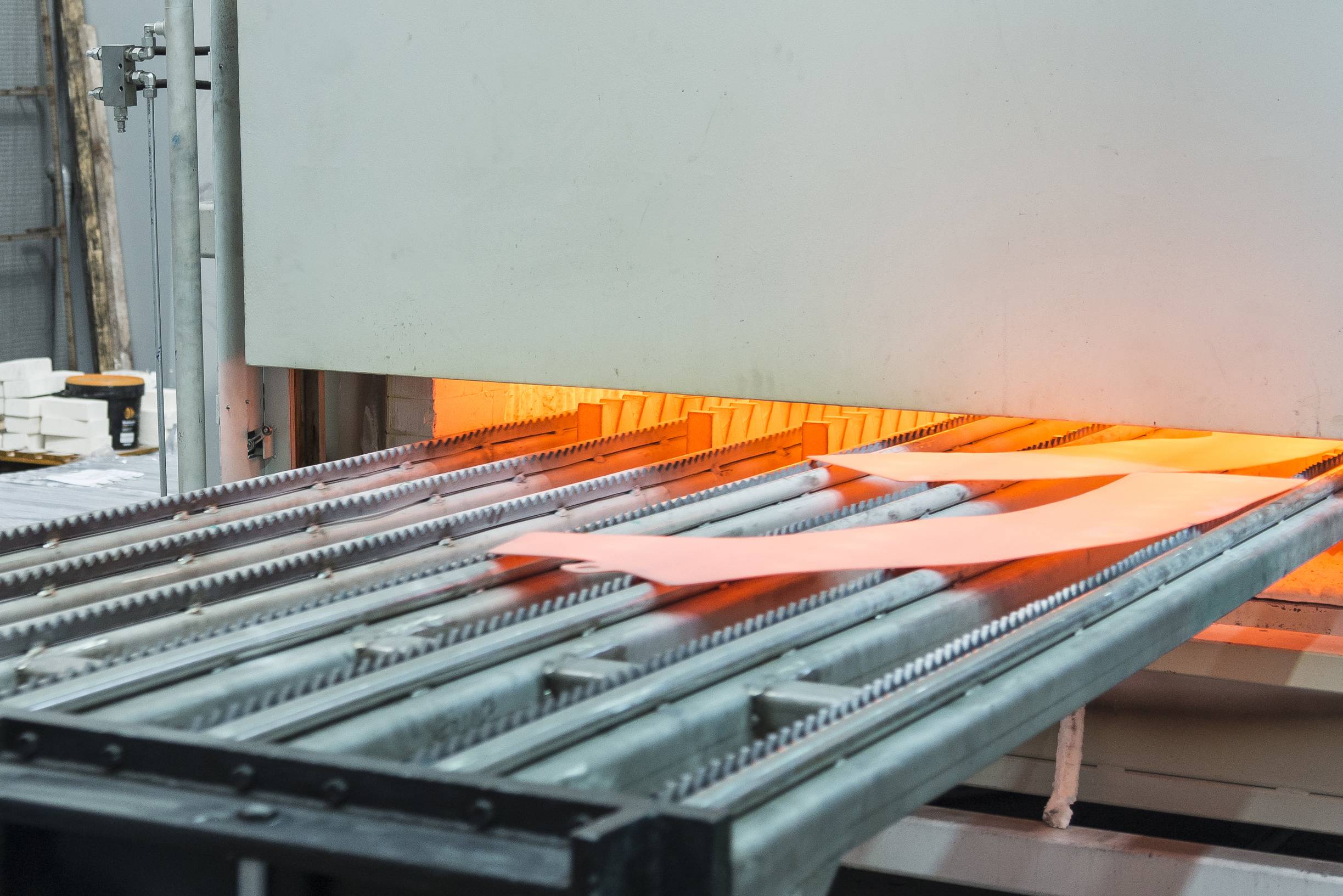
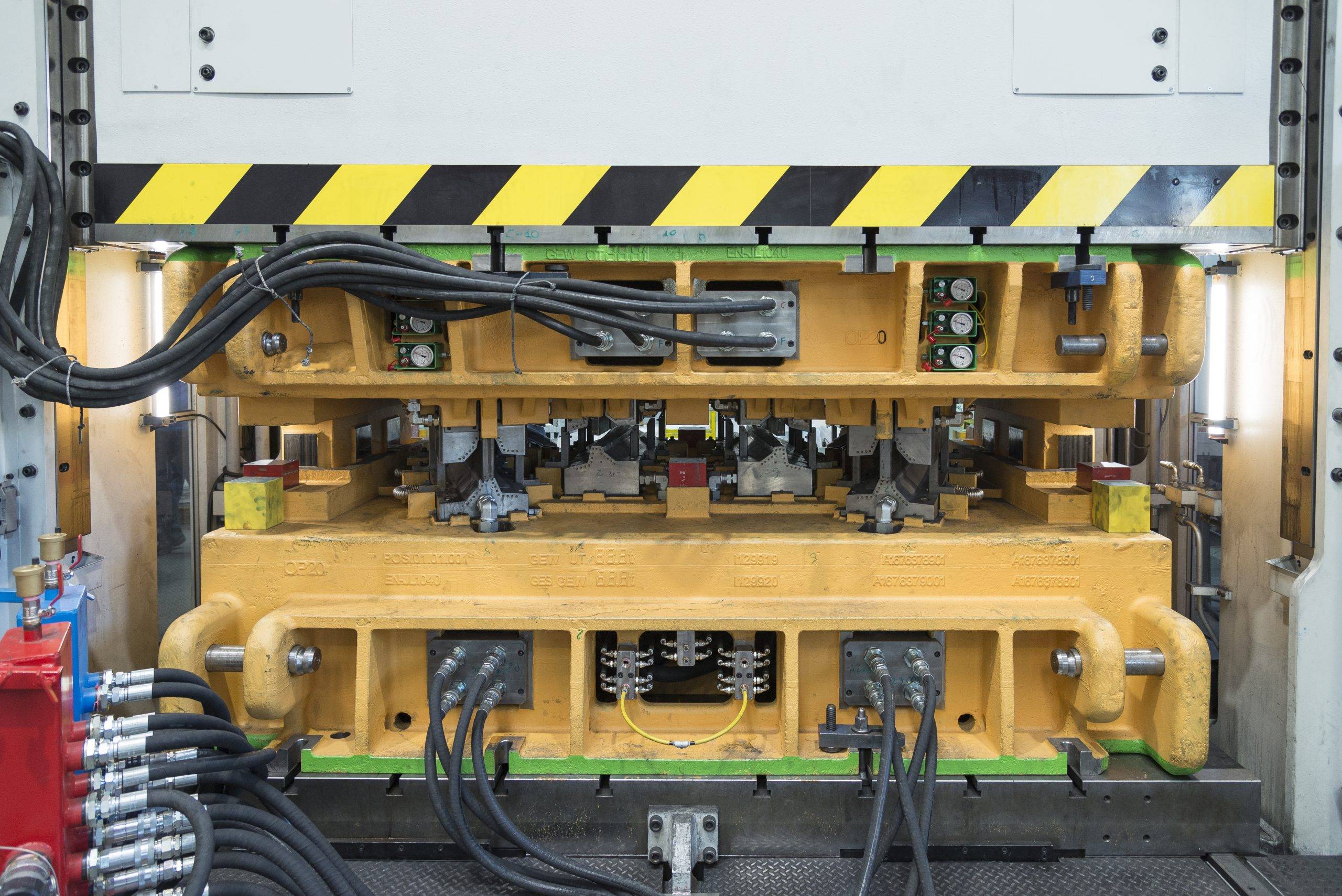
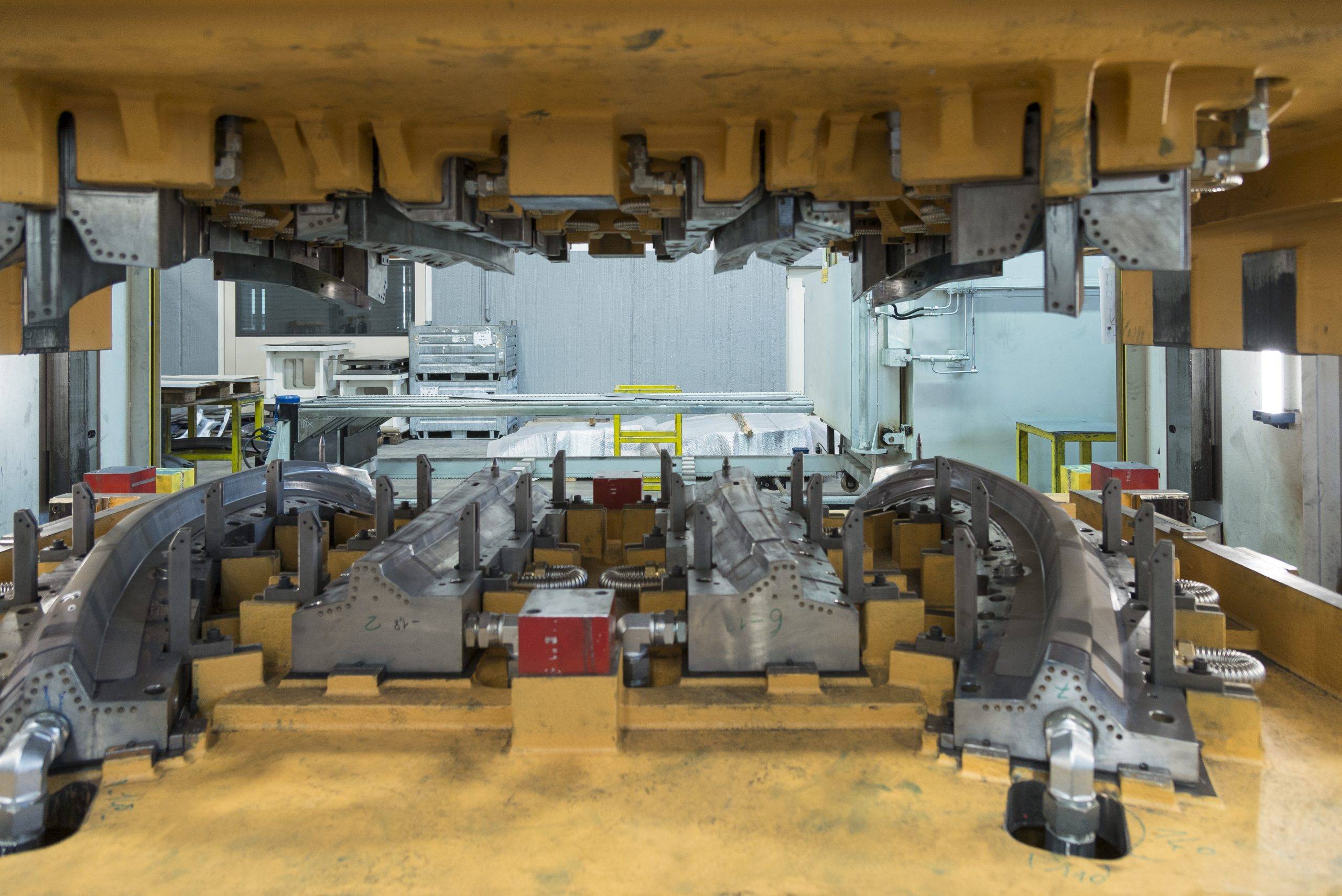
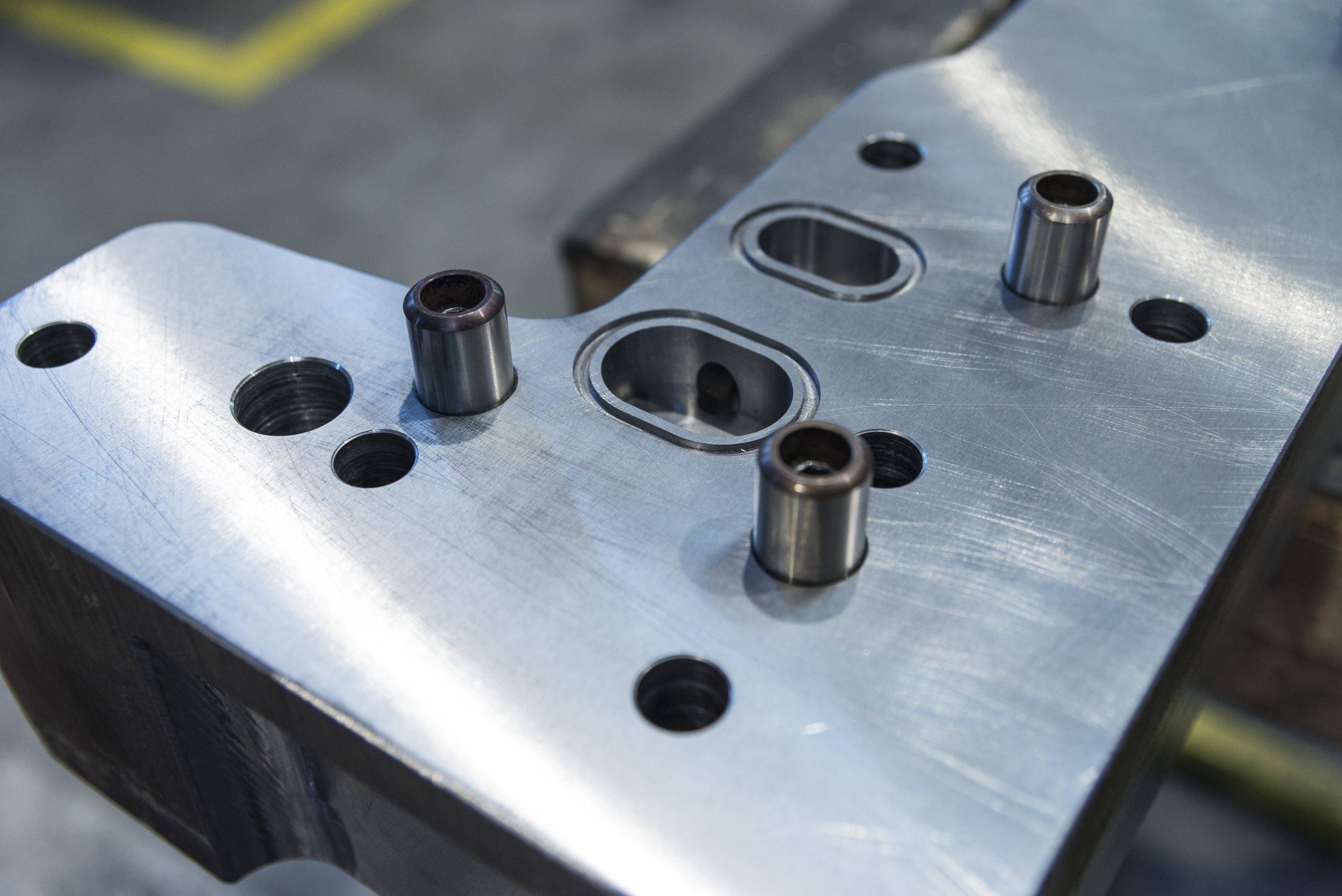
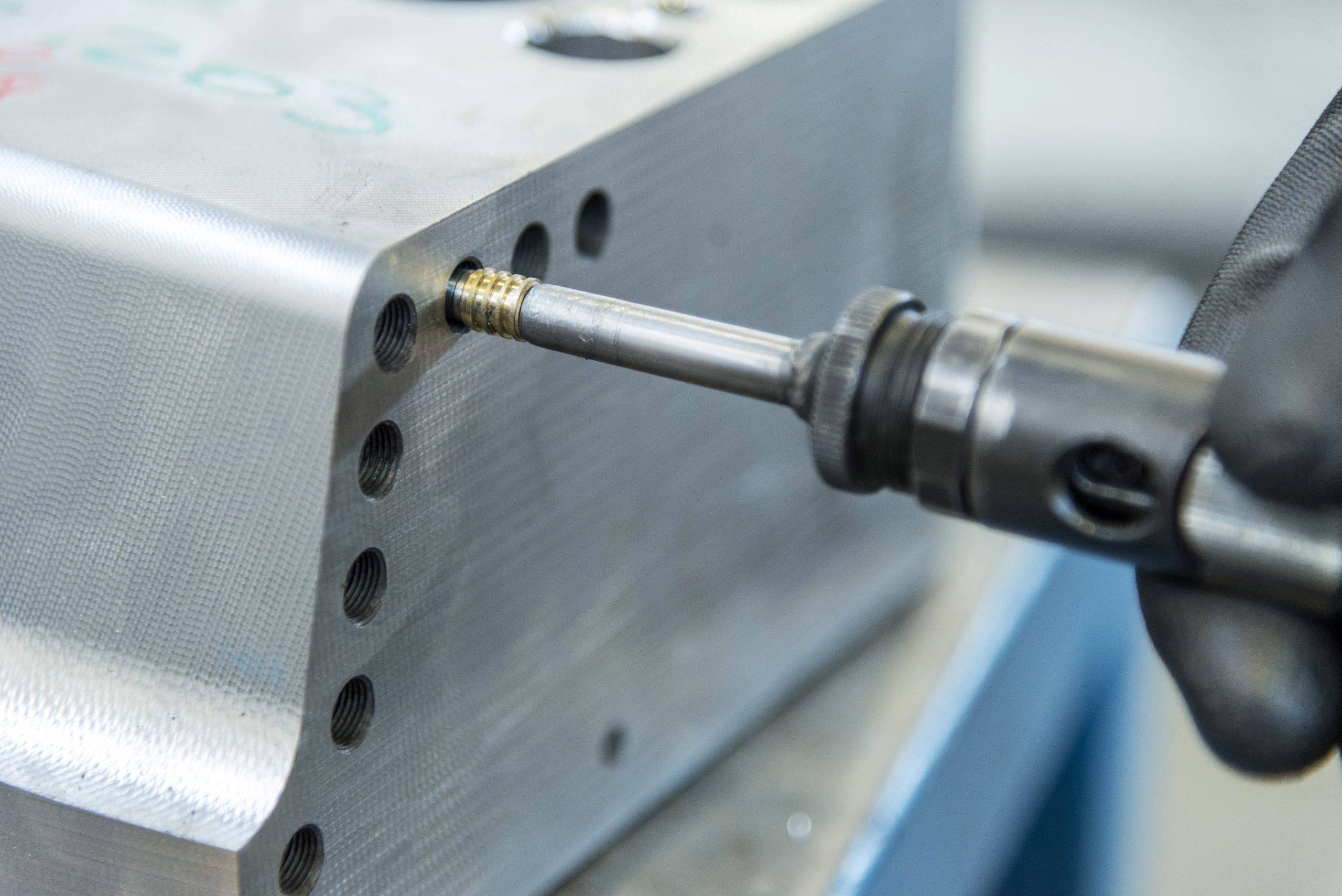
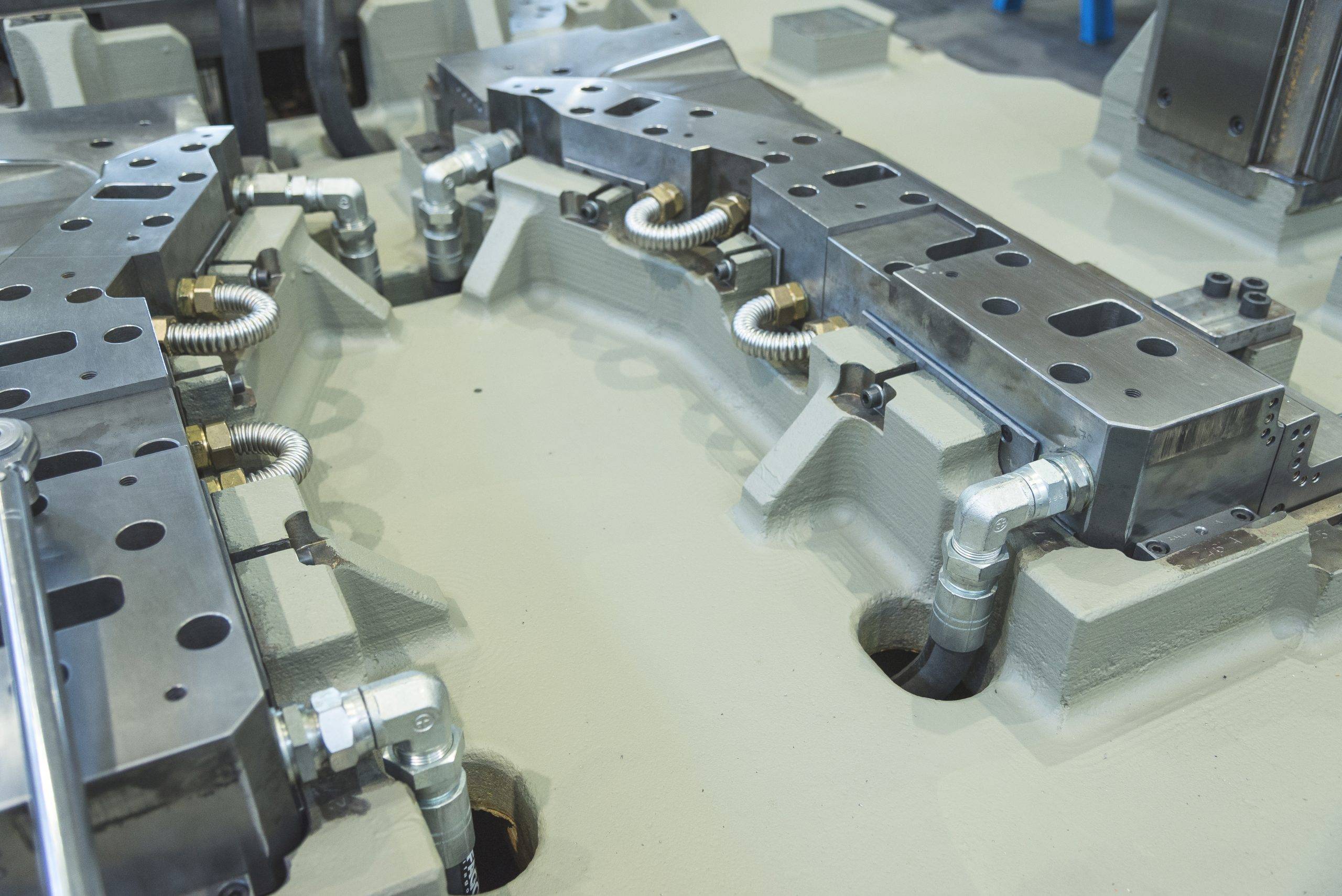
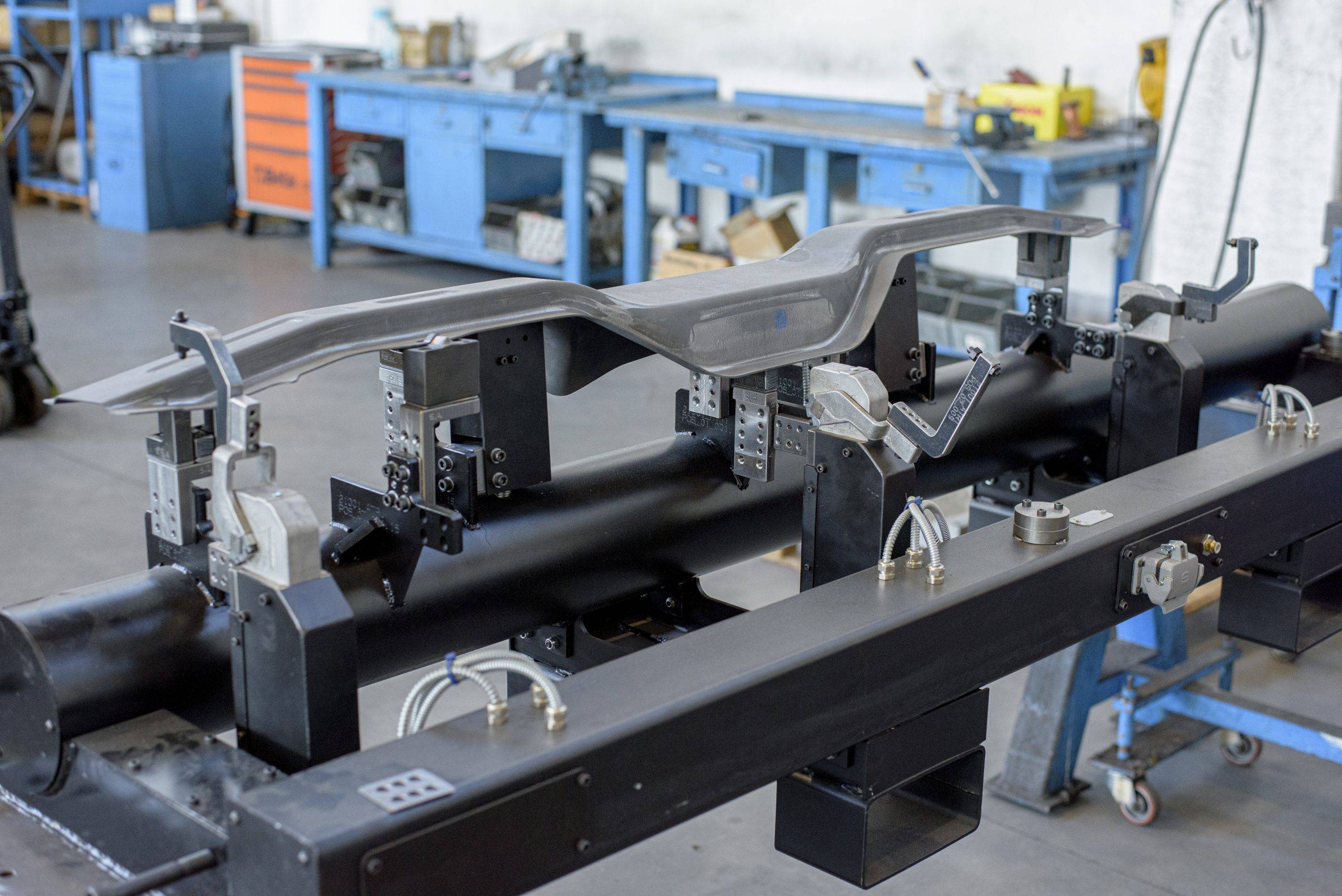
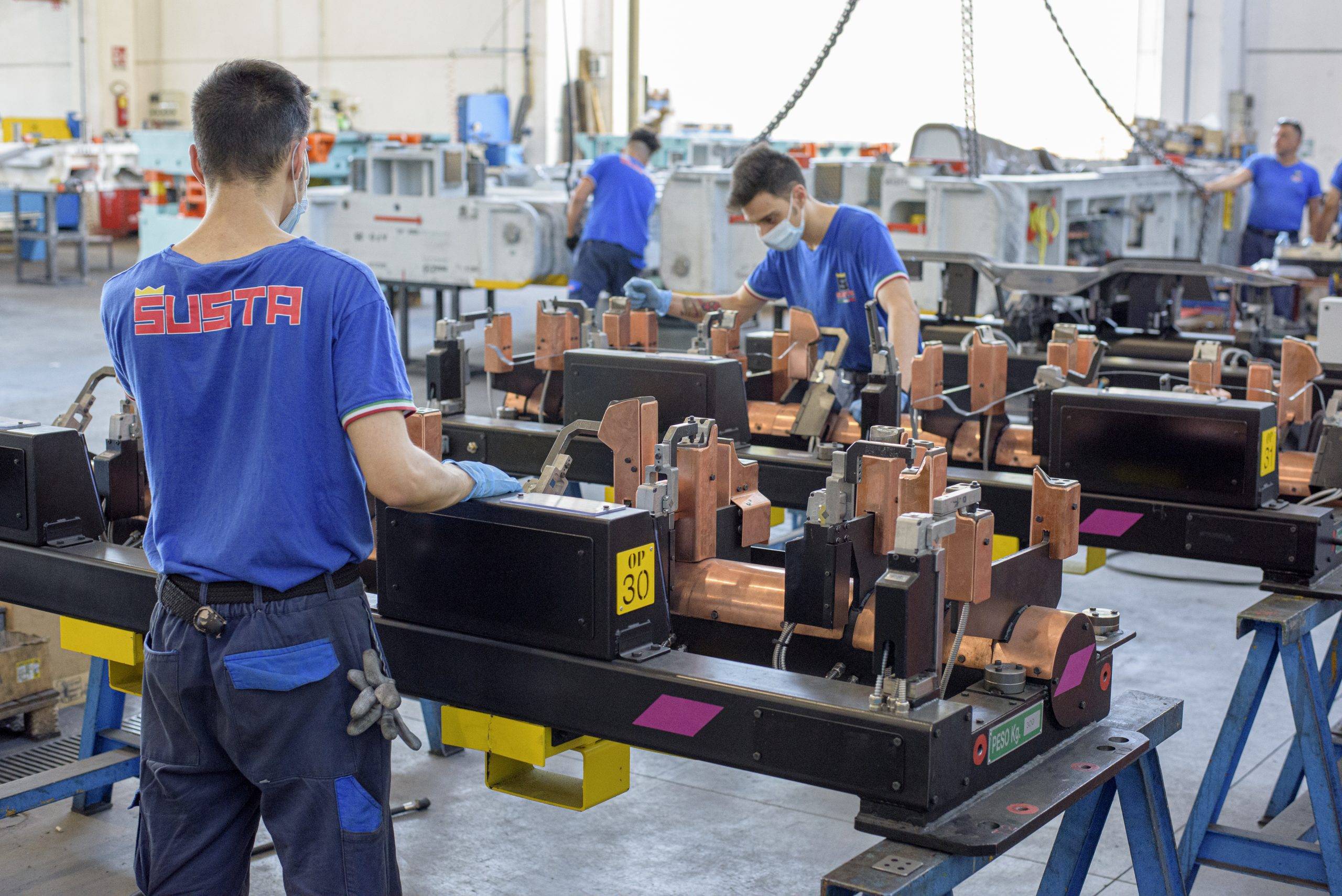
DIES FOR HOT FORMING
BREAKING NEW GROUND: A COMPELLING CHALLENGE
Hot forming is an alternative to cold forming: it is a path that opens up new challenges; a path that Susta has walked and continues walking to manufacture parts which need superior features of lightness and resistance to impact. The design and assembly of this kind of dies requires additional, special expertise. It is necessary in facts to pay great attention while machining the channels and cooling circuits, as these are critical for the functionality of the die itself.
LASER WELDING AND HARDENING:
CUTTING-EDGE TECHNOLOGY
Quality must be nurtured with investments in technology and knowledge. Being well aware of this, Susta has invested in a next generation welding and heat hardening laser machine.
The working area is 9000x3000x2500 mm, with rotary and turning table, maximum payload 1,1 T and a second turning table maximum payload 6,5 T.
The laser machine is equipped with a hardening head with laser diode and with head for powder laser cladding, both with power 6kW.
Moreover, the machine has a thermal camera available for temperature control, a camera for machining control – with possibility of adding a filter for viewing the areas being welded- and a process camera for controlling centring and welding flux.
An equipment which enriches the range of high value solutions the company makes available for its customers.
Benefits of 3D Laser hardening
Susta has chosen this machine due to the benefits the 3D laser welding brings to several processes.
Laser heat hardening – that takes place when the part is finished – grants almost no deformation; this way no geometrical tuning is needed.
Through the self-switching process of the material surrounding the processed area there is no need of cooling the part.
Laser hardening also allows a more precise and consistent result both in terms of required hardness and depth of penetration.
Another important feature of this technology is the possibility – given by the robot tooling – to modify the track width of the laser spot opening in it during machining, starting from a minimum of 6mm up to a maximum of 60mm.
Benefits of 3D Laser welding
Laser welding makes it possible to coat, fix or even make new parts by means of powder fill. This technology allows less distortions compared to traditional welding thanks to the low thermal input. It is also extremely versatile as it can be applied to all materials, steels and cast irons, both hardened (58-60HRC) and unhardened.
Laser welding also consents high precision in the applied layers, high speed and the possibility of varying the opening of the spot (laser diode?) from a minimum weld bead of 2mm up to a maximum of 6 mm.