Method
SIMULATION AND SOLUTIONS
Thanks to a highly skilled team made up of engineers and specialized technicians, Susta is able to manage simulation, method and die construction in-house with clear advantages in terms of both time saved and responsiveness.
Trained designers work with the best software for drawing simulation and reverse engineering to provide a complete package and meet the manufacturers’ needs.
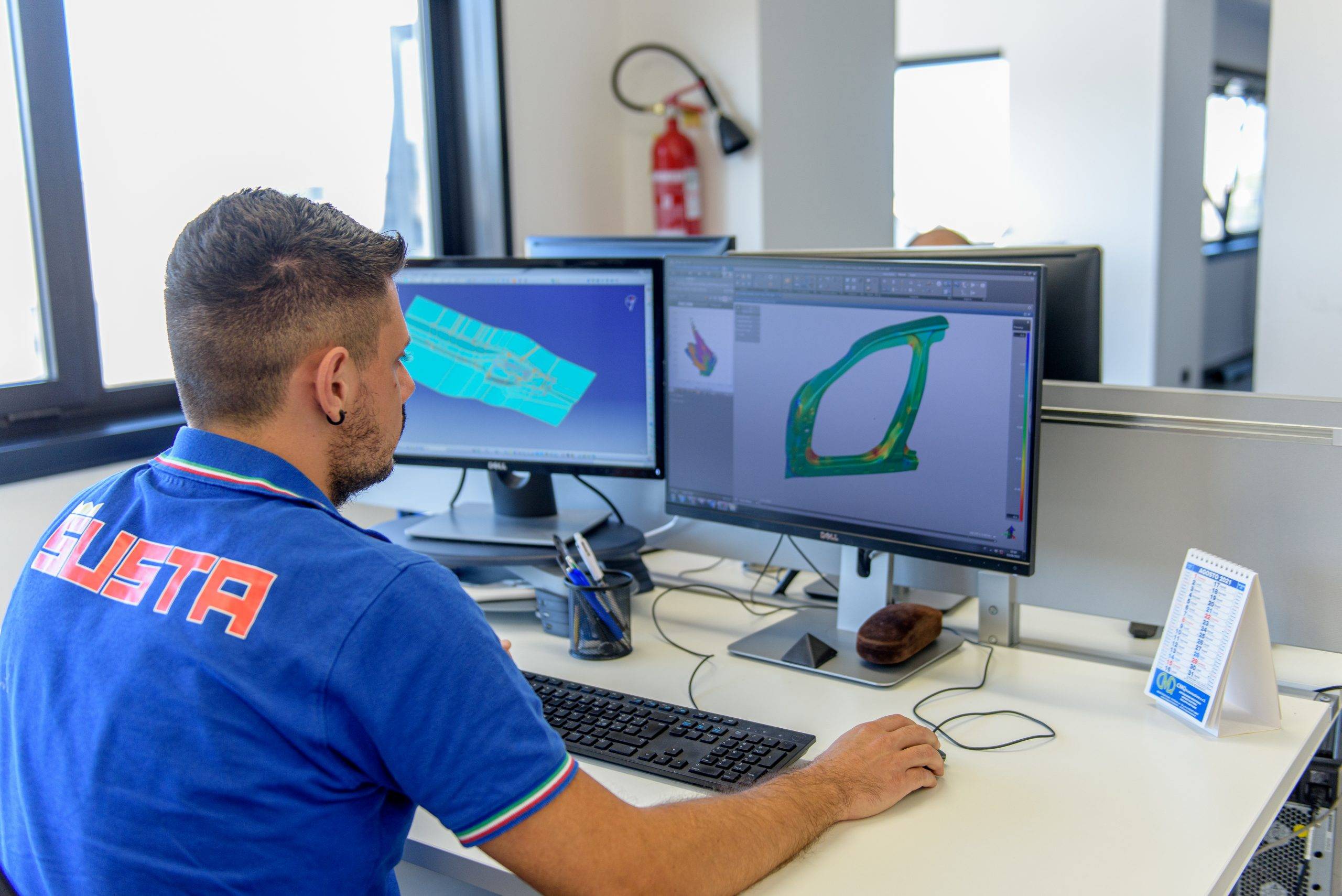
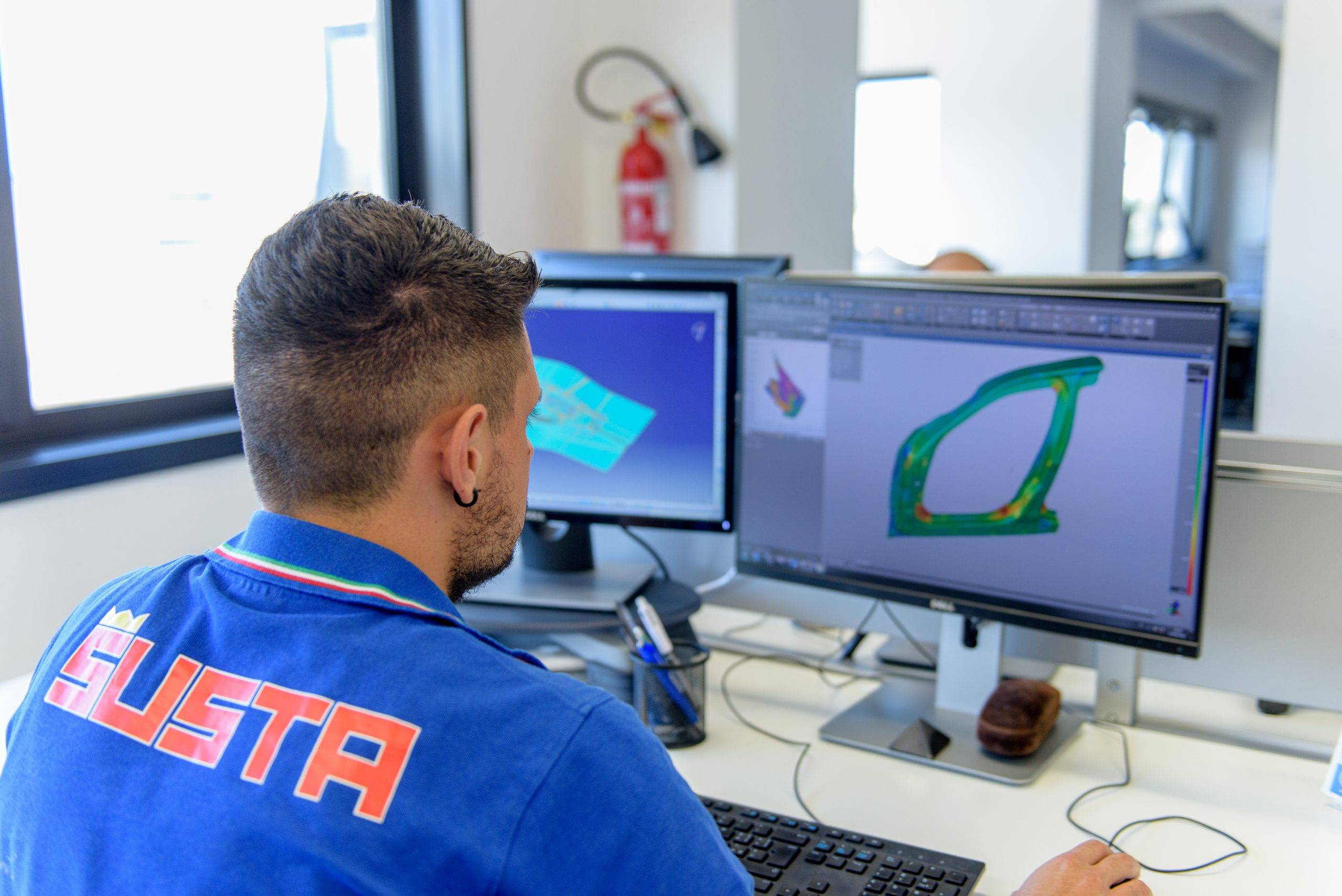
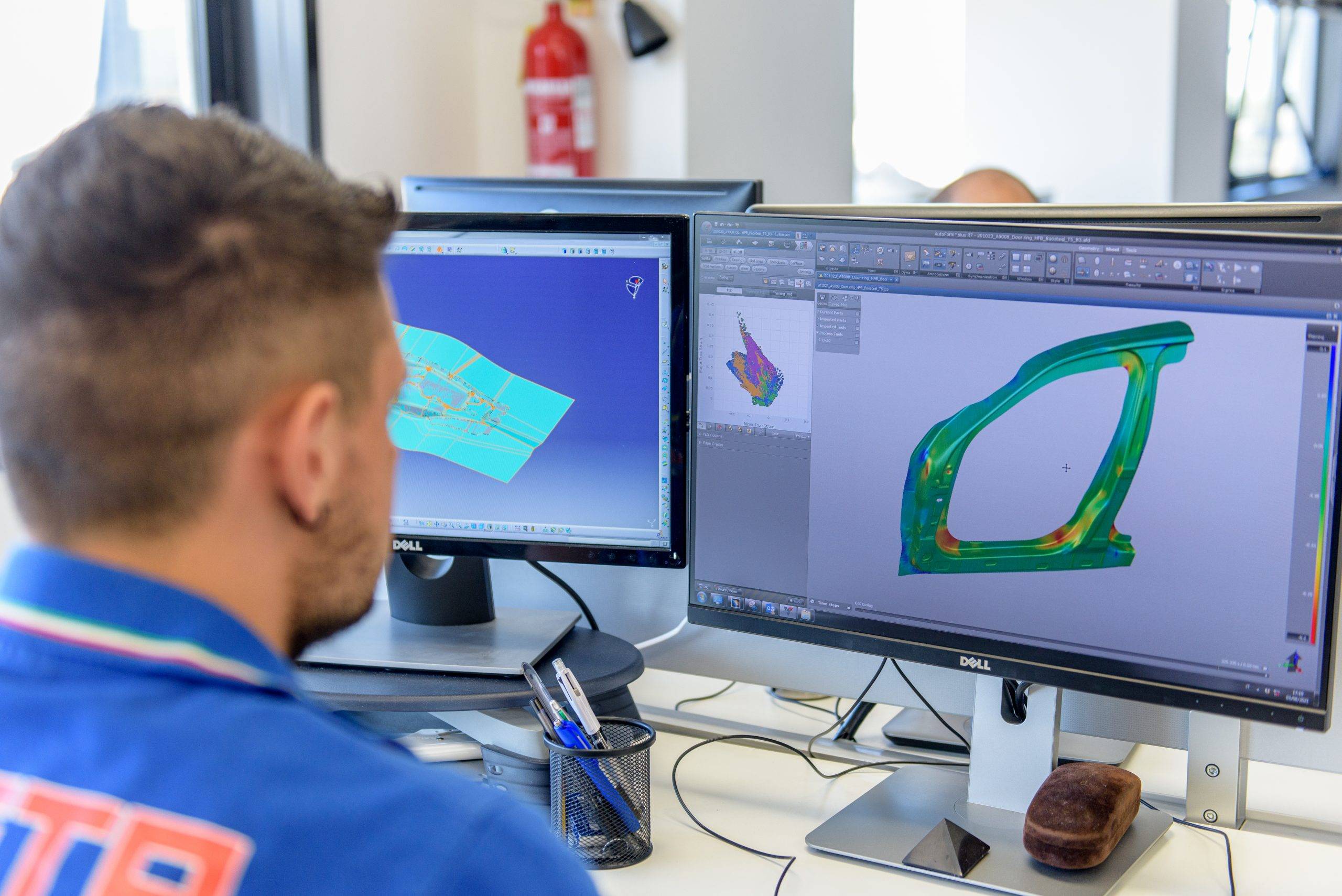

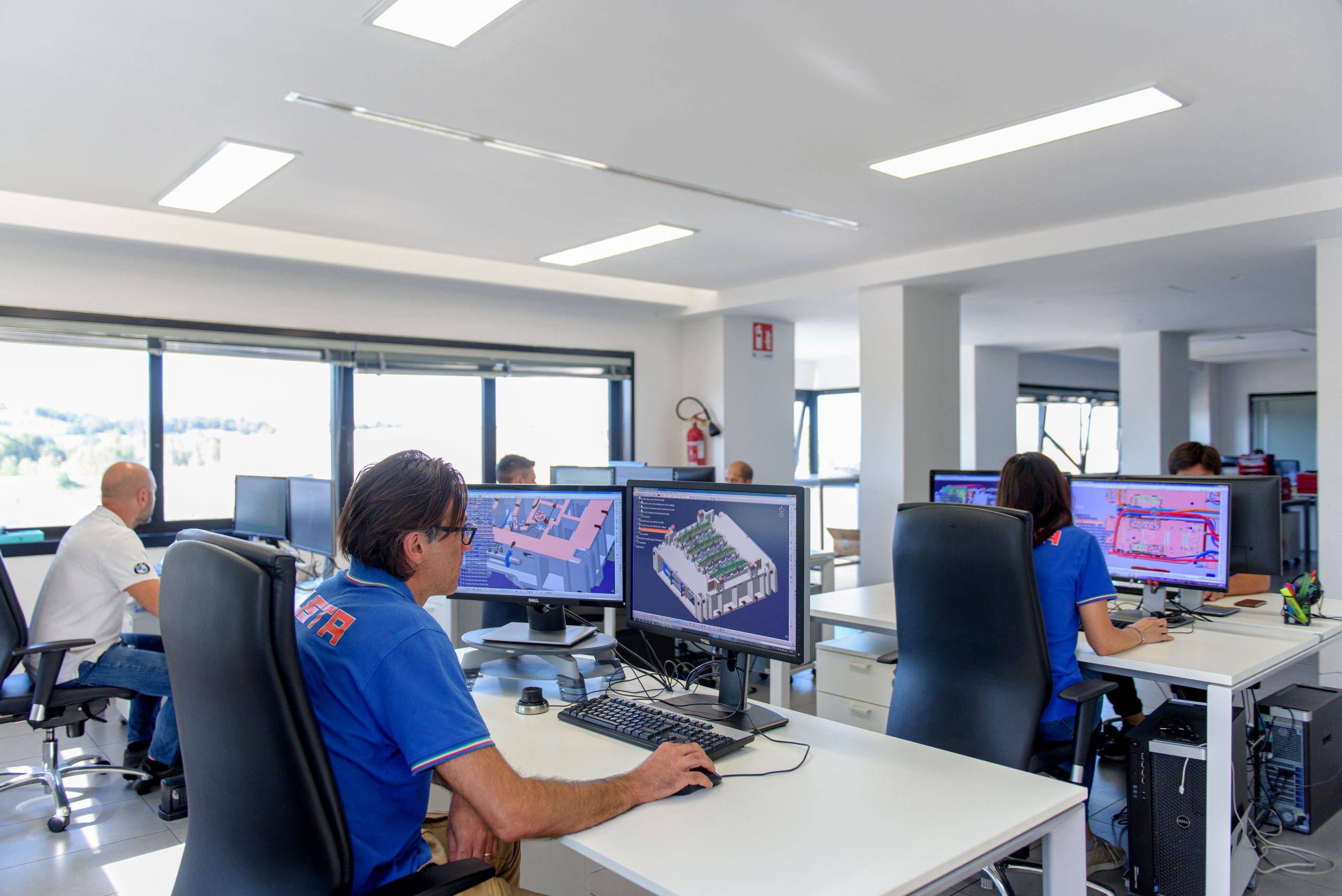
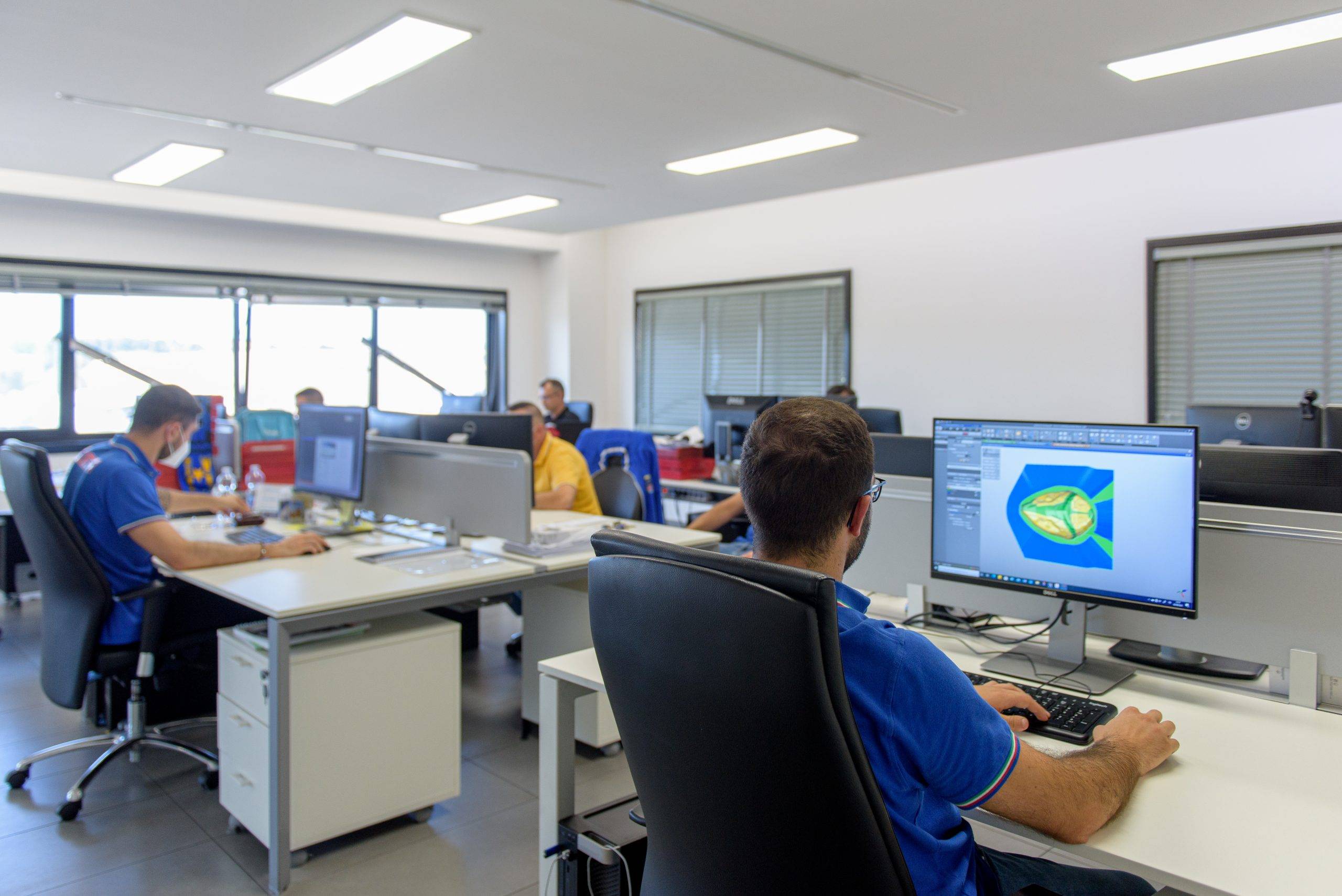

DESIGN
The exchange of information and the customer’s feedback are main points of Susta’s manufacturing process.
The executive project is processed using CATIA and Siemens NX and is shaped according to the standard agreed with the client. During all the steps of die design there is a constant exchange with the client: this enables to share the process in all its aspects and to answer all requests in real time with the most suitable and effective technical solutions.
MILLING
One of the winning features of Susta is the expertise of its personnel and the variety of its equipment.
To manufacture the parts that make up the designed die, on board programming of the milling paths of the machines with CAM software is carried out by our workers, who are millers 2.0.
For more complex machining and surface copying tasks our CAD-CAM team of 6 programmers gets involved.
Susta can count on more than 35 medium- and large-size milling machines, among them also state-of-the art simultaneous 5-axis milling machines.
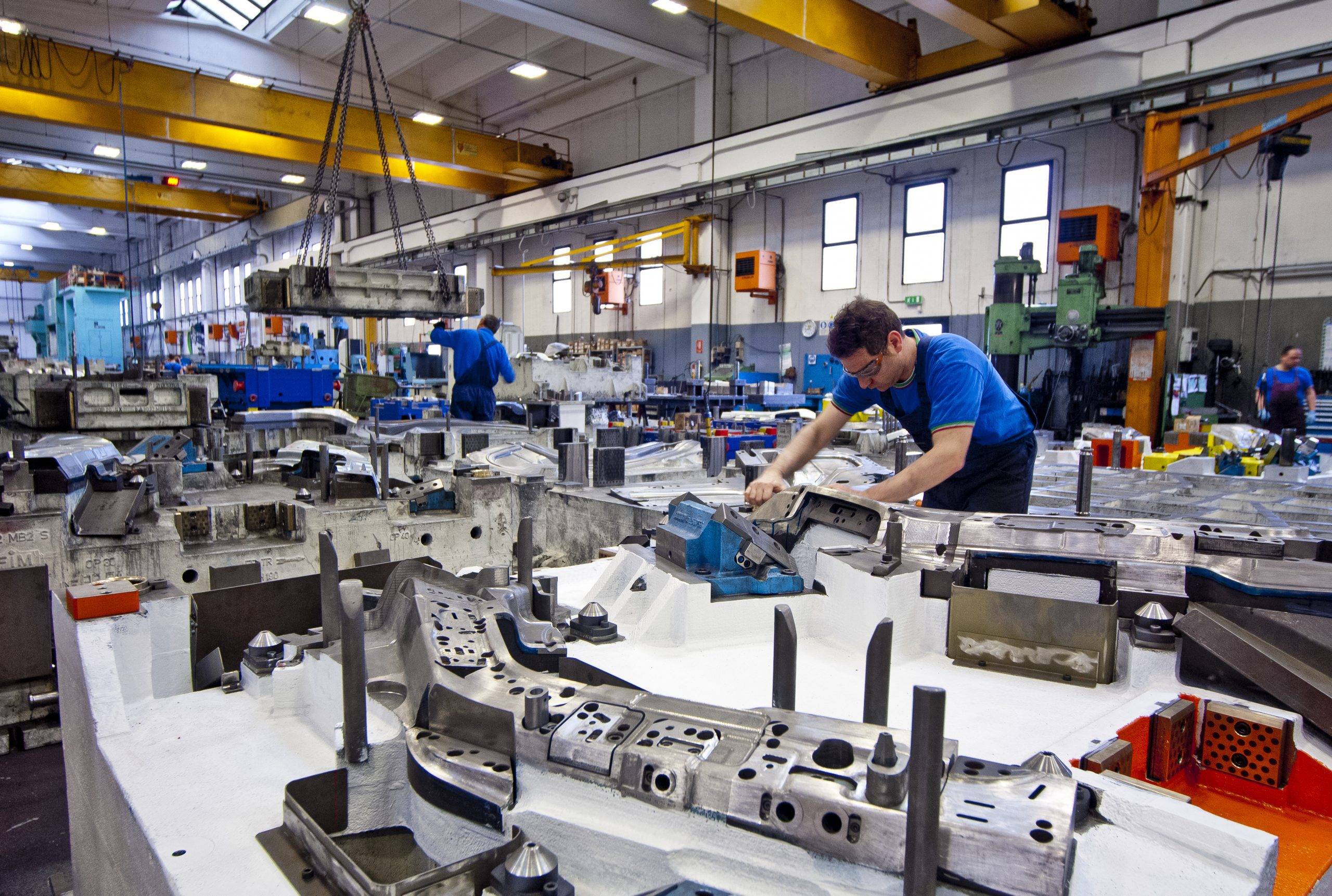
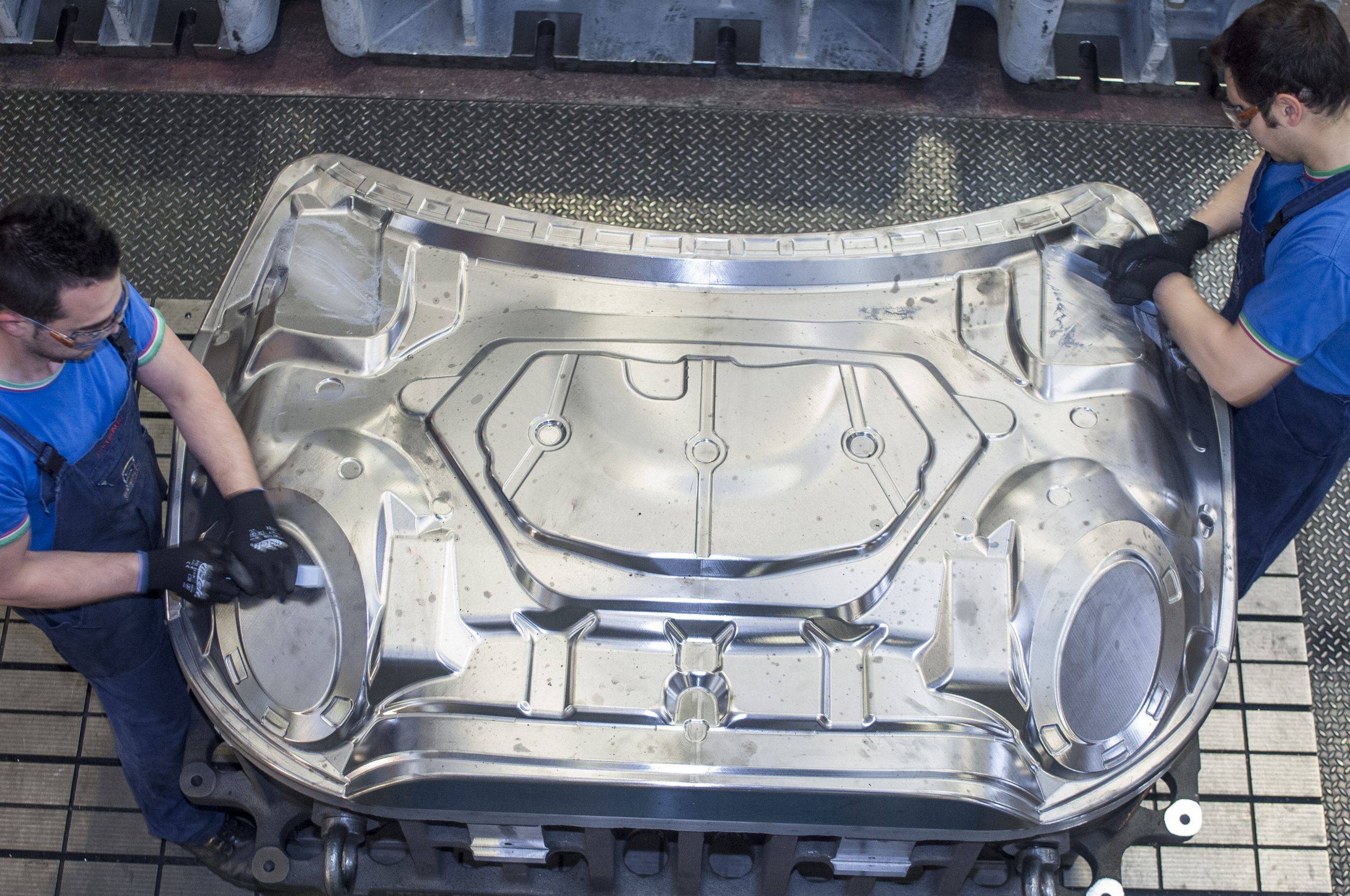
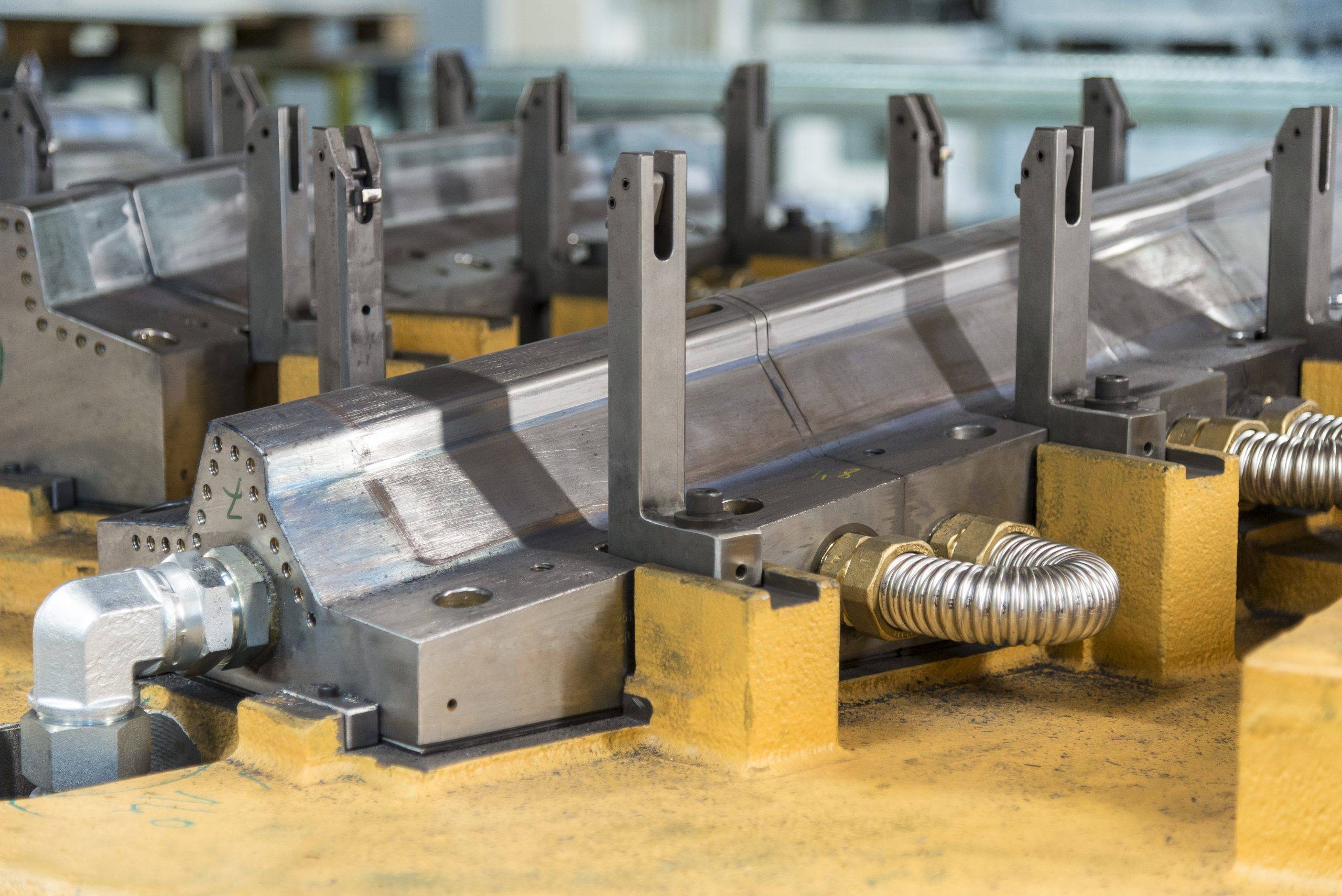
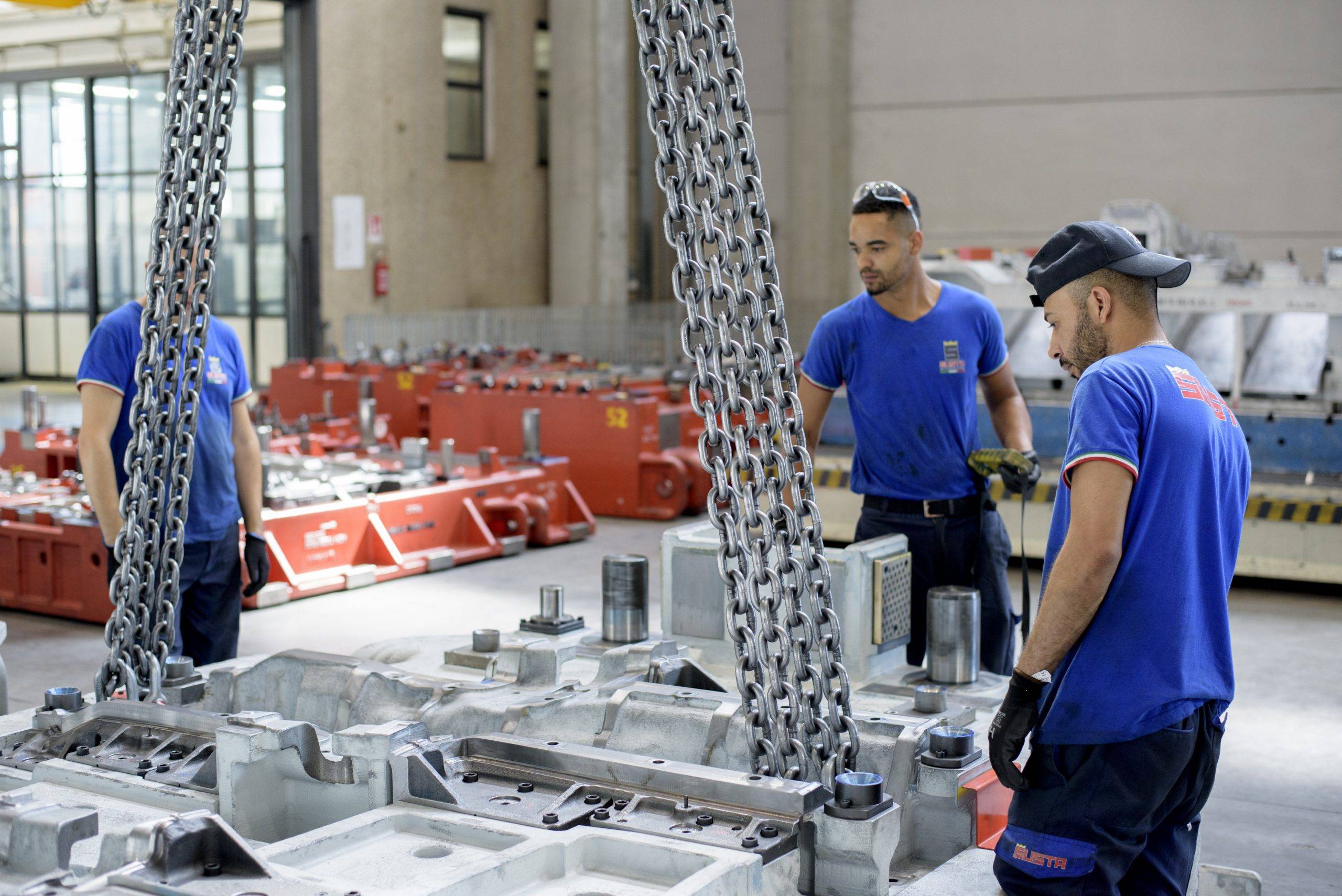
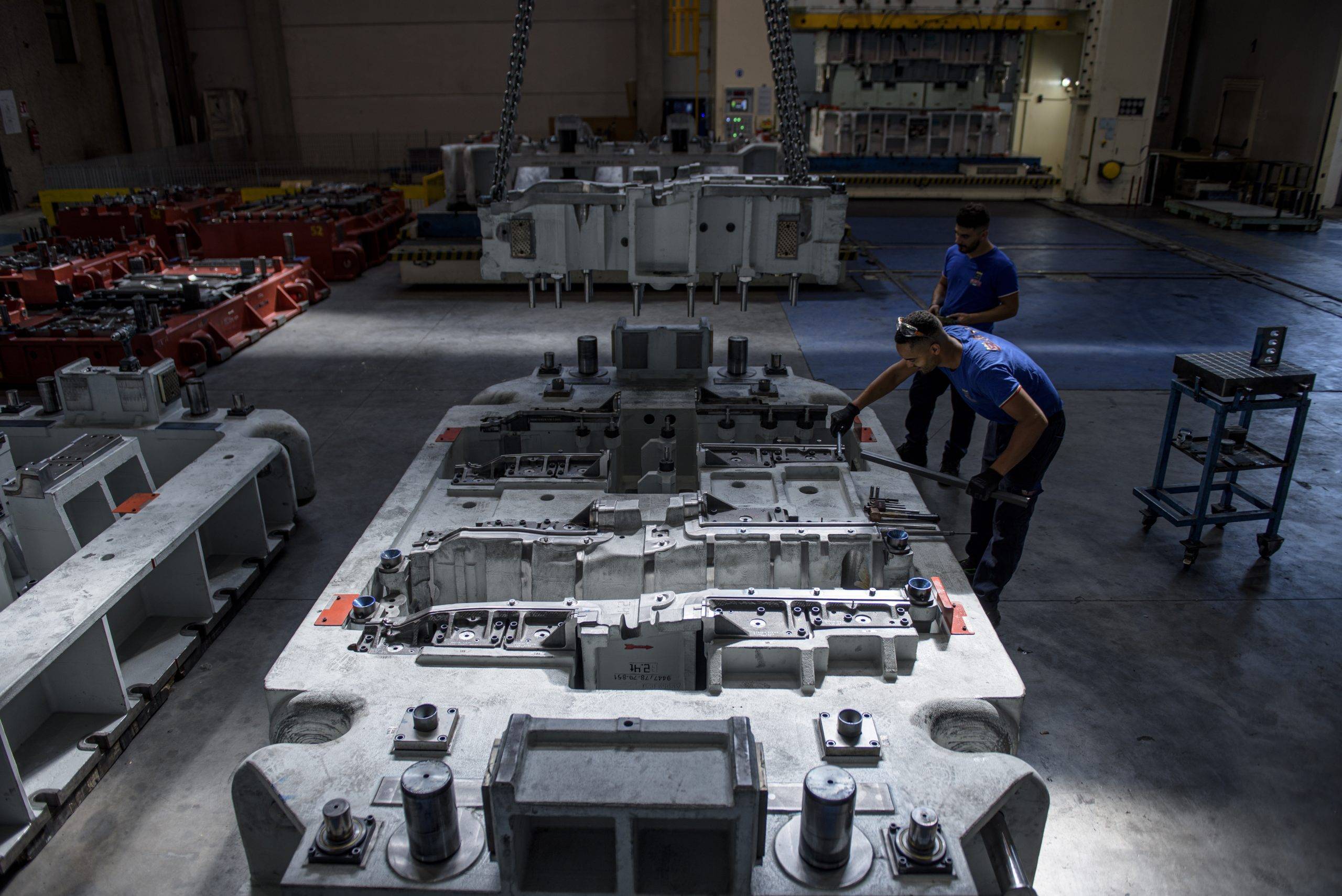
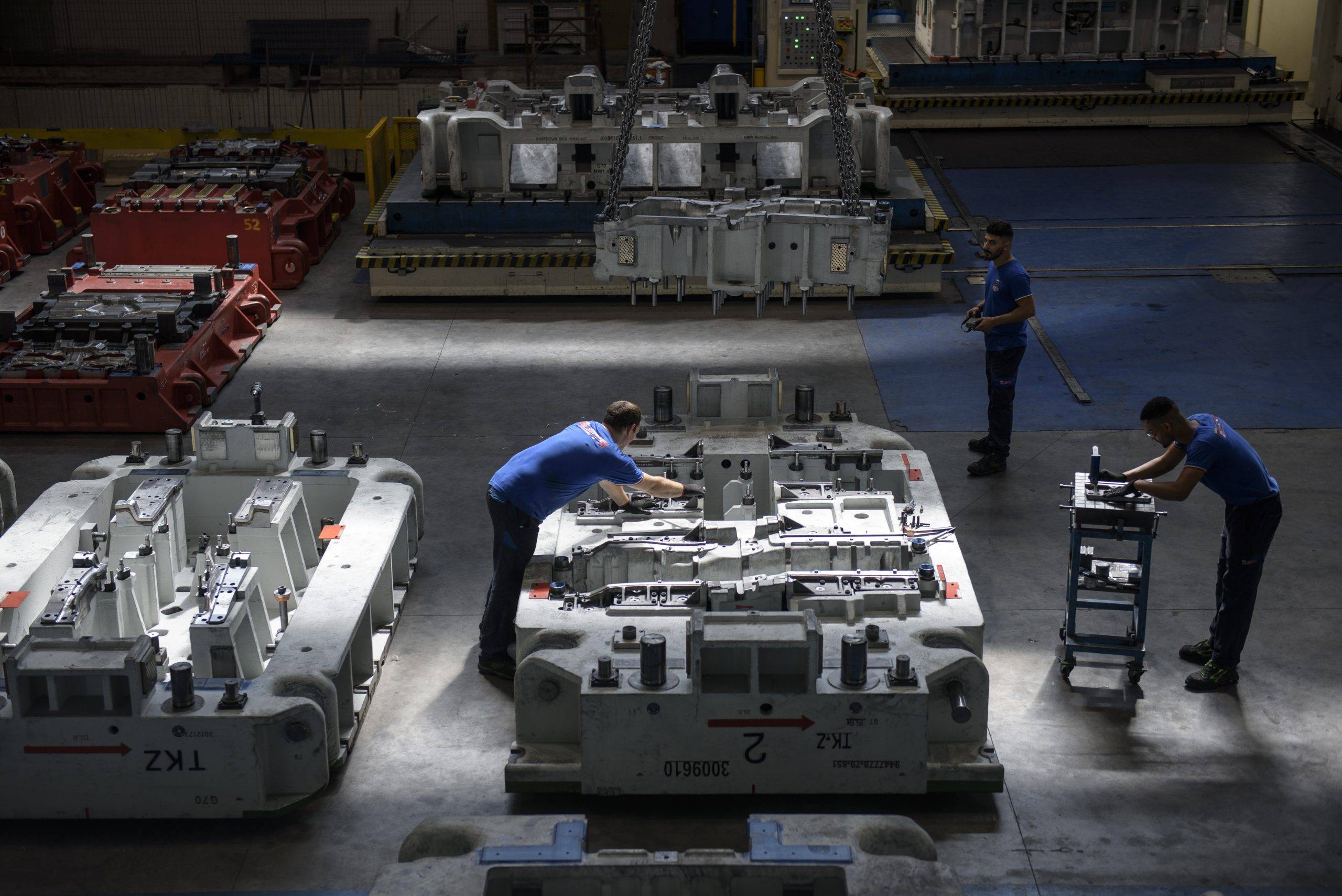
ASSEMBLY
The die is assembled in our workshop, where our teams of assemblers have at their disposal manual and CNC grinding machines.
Their experience and accuracy make it possible to work within the specifications provided by the client with excellent results down to the last detail.
At the end, the die is already up and running for set-up.
FINISHING
The finishing step is assigned to qualified and skilled technicians who finish the die to the finest detail: painting, electronical system and safety equipment. Now the die is ready for the try-out activities at the customer’s premises.
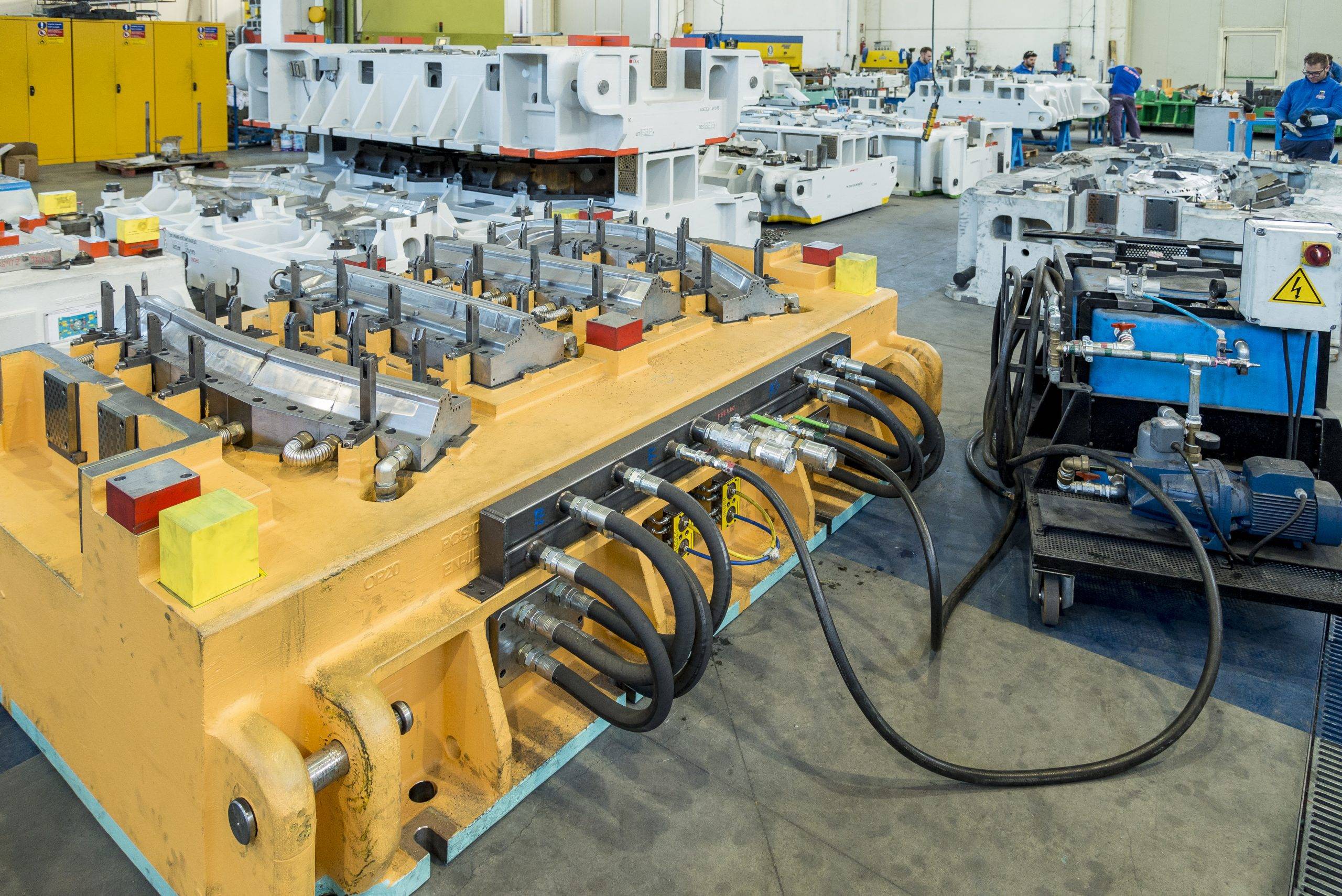
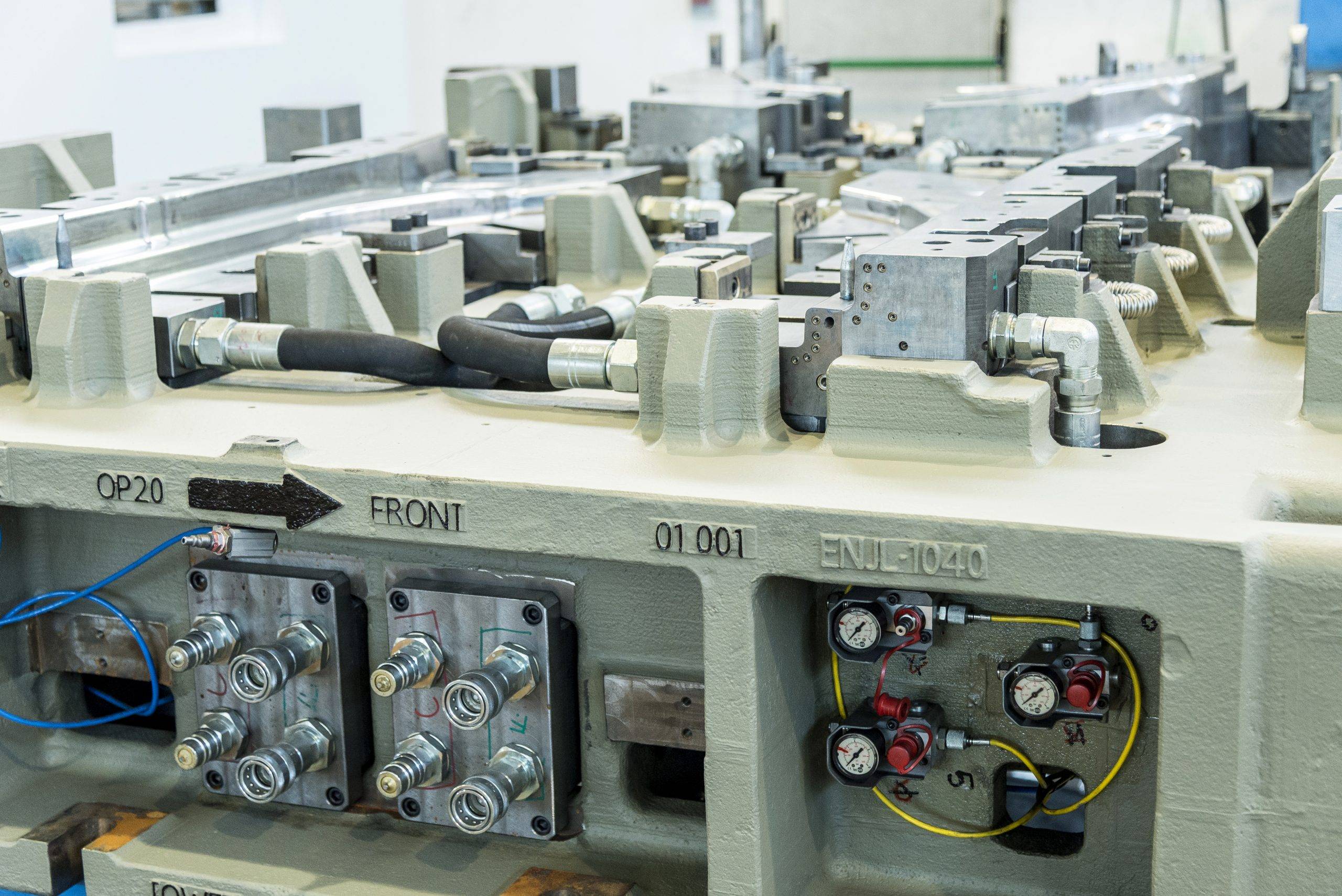
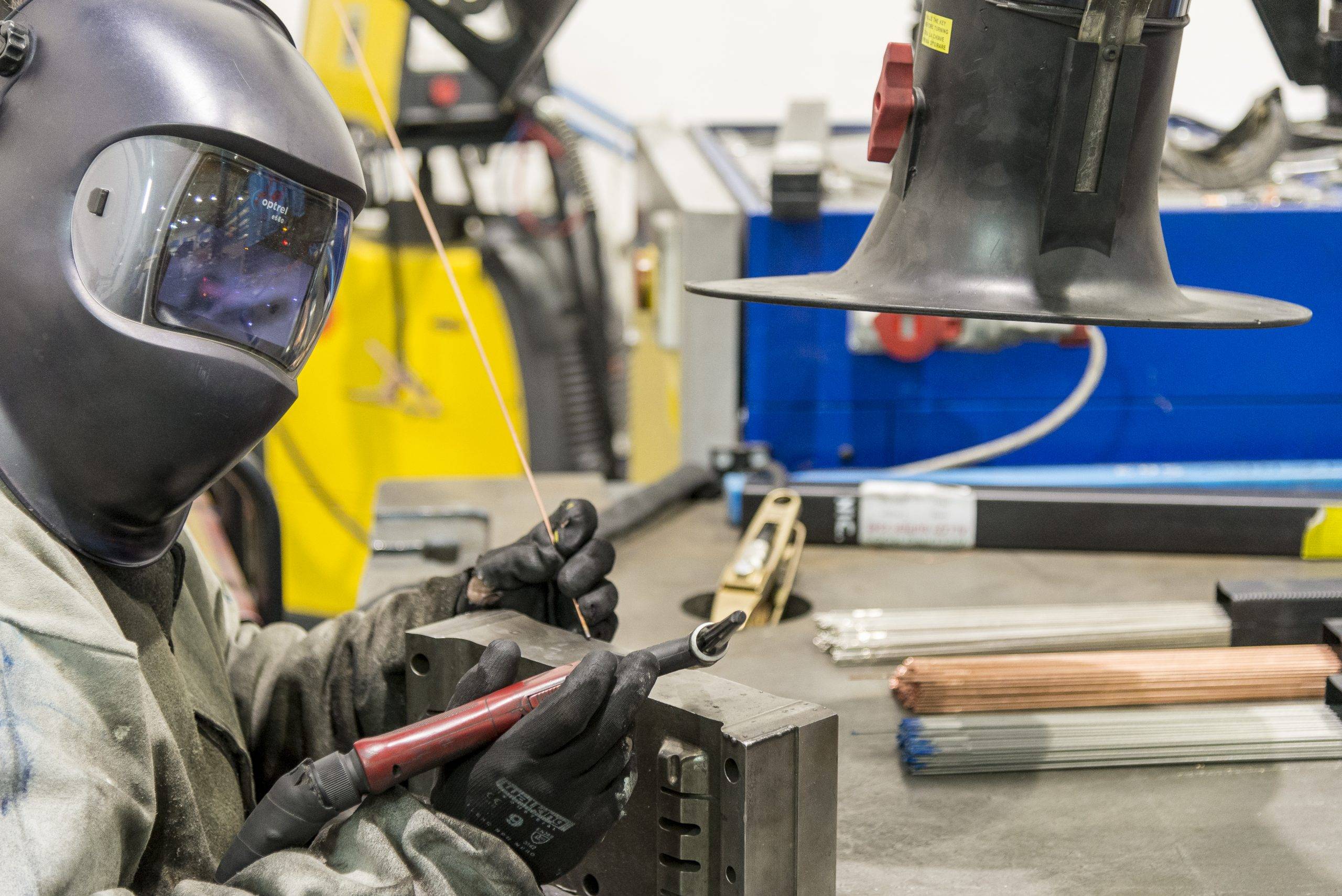
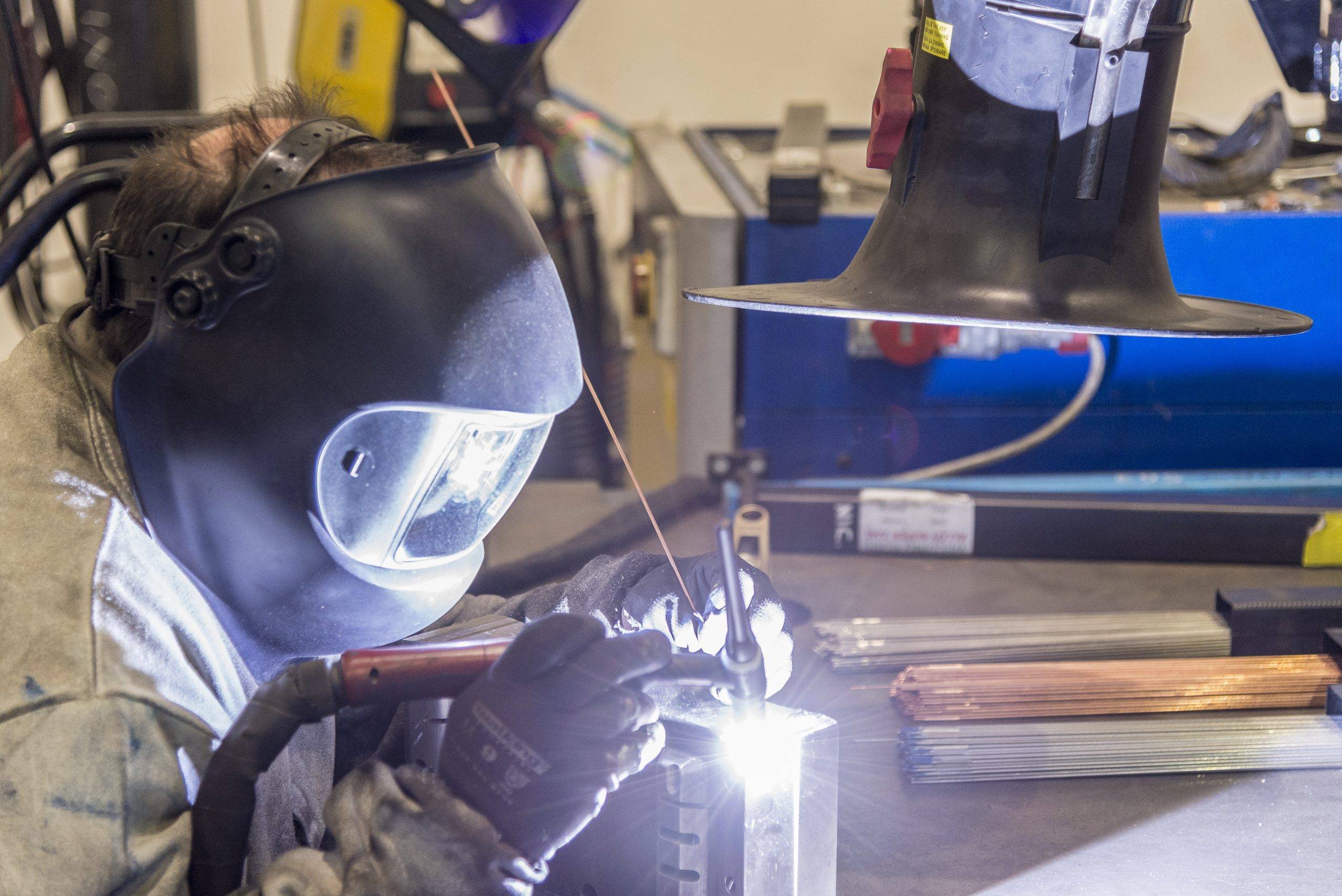
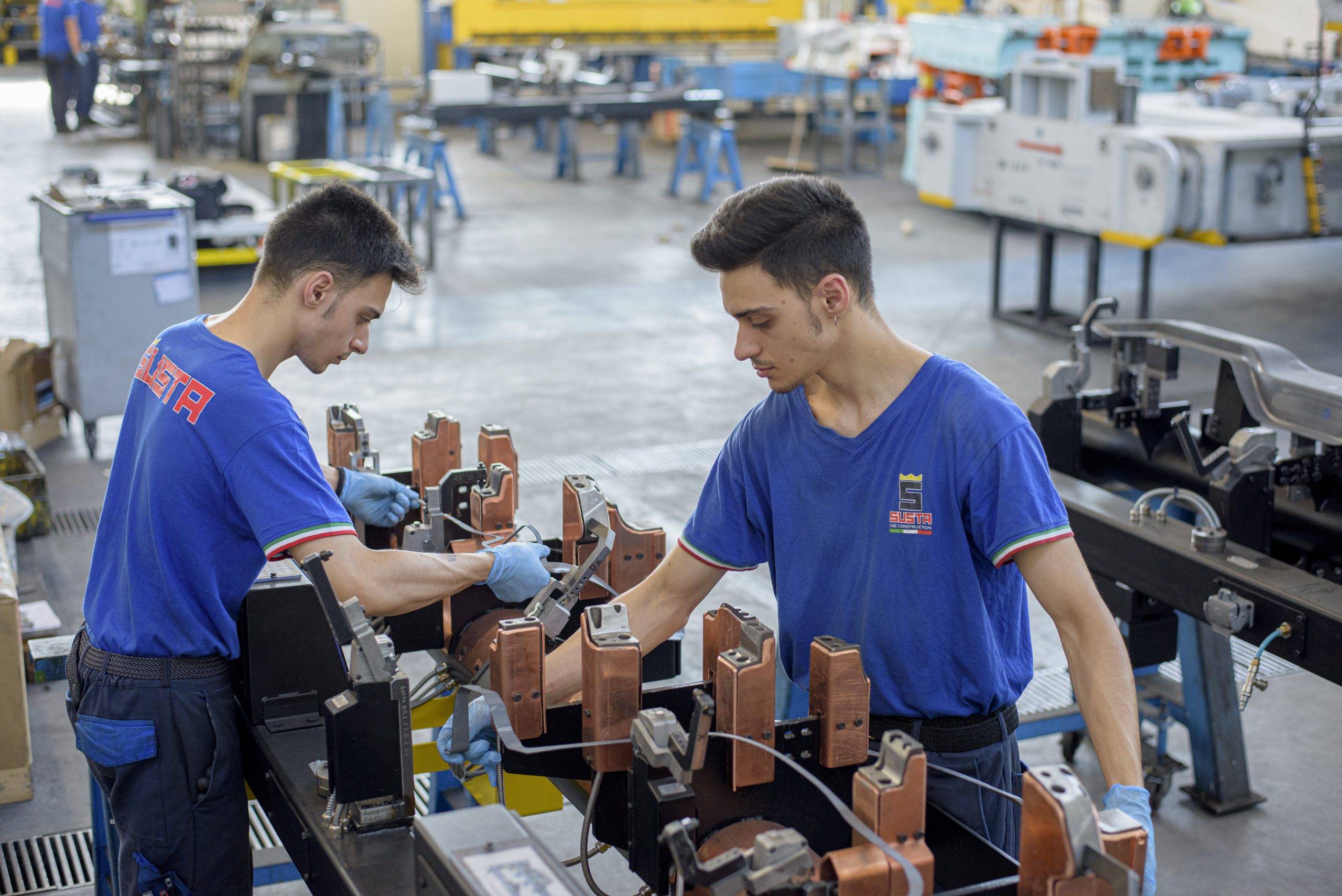
TRY-OUT & SOLUTION
The goal is delivering a functional die according to the dimensional tolerances the client requires. That is why the validation of the correct assembling and functionality starts in our workshop.
In order to cope with this commitment, Susta relies on a well-organized teamwork enriched by the Italian touch. The different professionals cooperate in checking and solving the most challenging steps to reach the best possible result, both in terms of matching with the required constraints and with the correct geometry of the part. The approach is based on a mix of technique, craftmanship and the typical Italian creativity.
The set-up phase consists in stamping tests with presses in conditions as similar as possible to the production at the costumer’s premises, until repeatable and in-tolerance parts are obtained.
The press shop can count on 8 hydraulic and mechanical presses with a maximal pressure of 2500T and table size up to 5000×2500 cm.
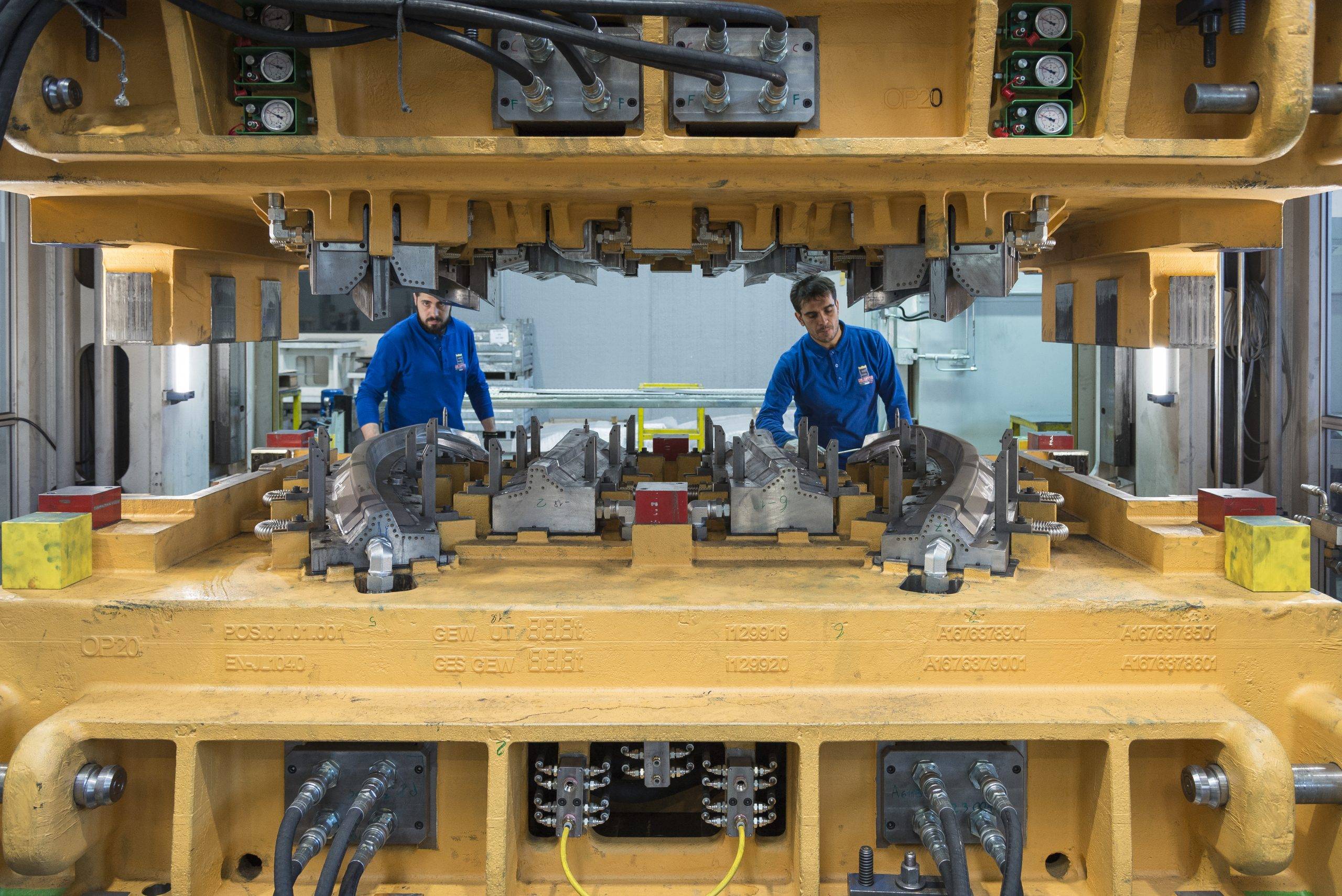
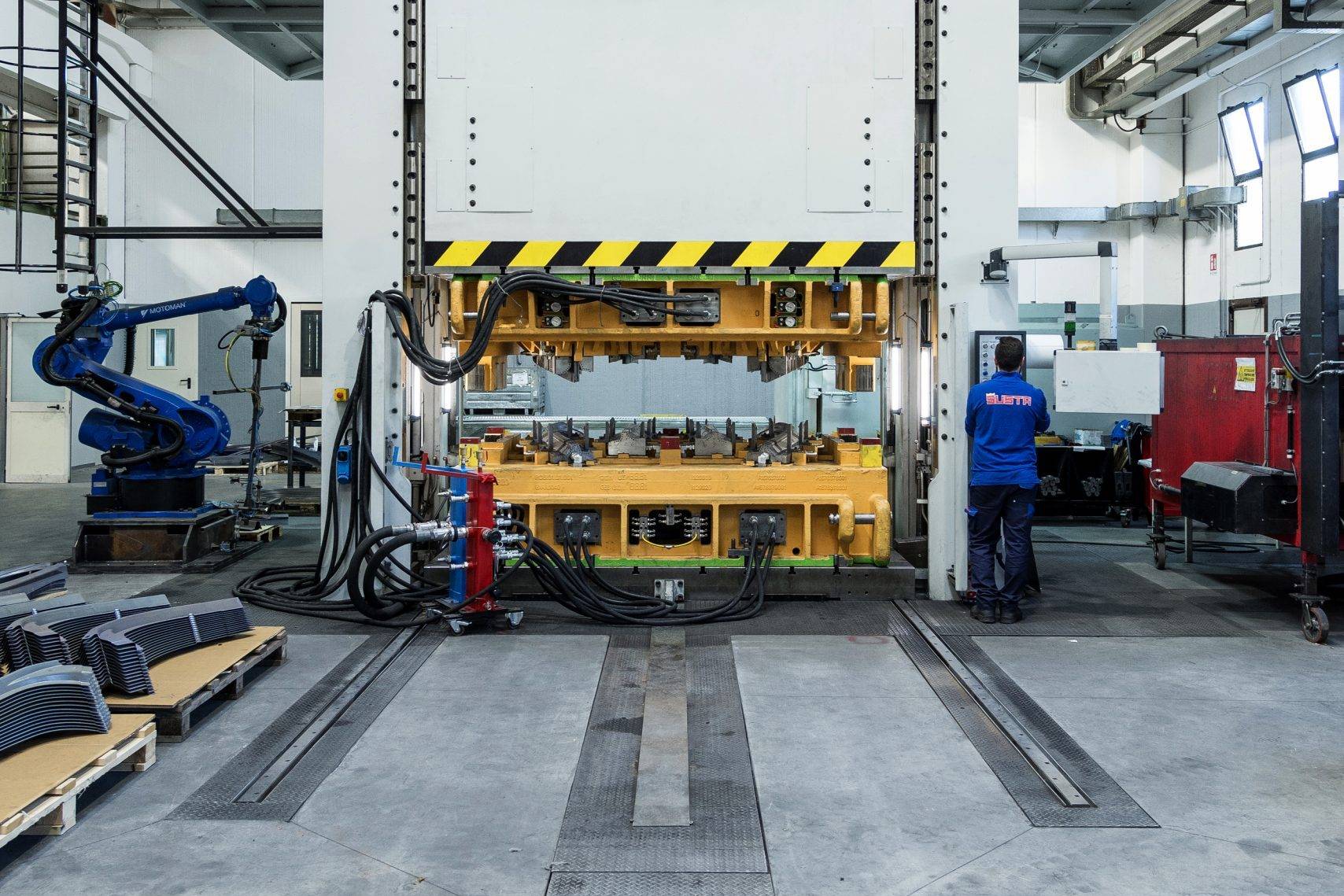
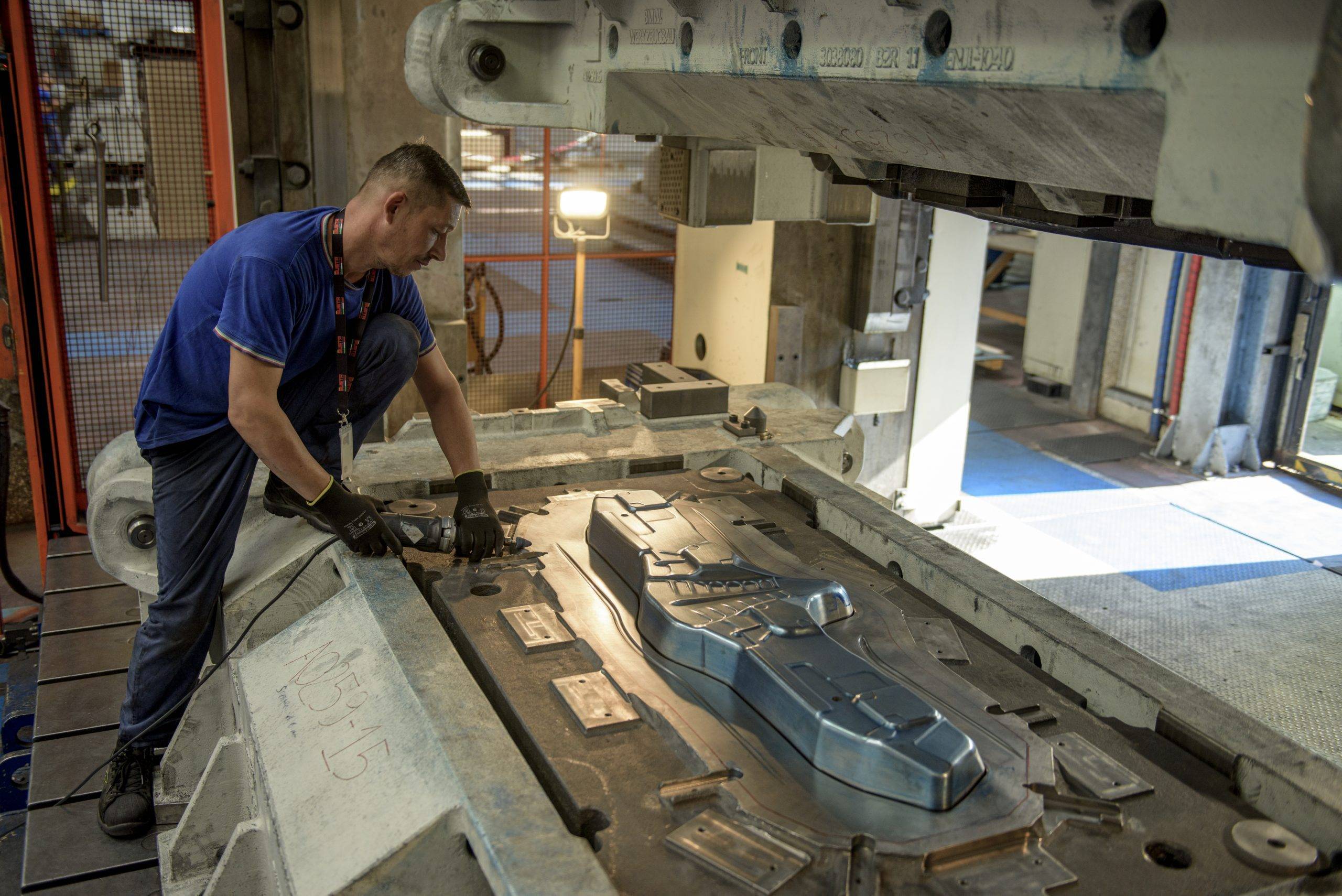
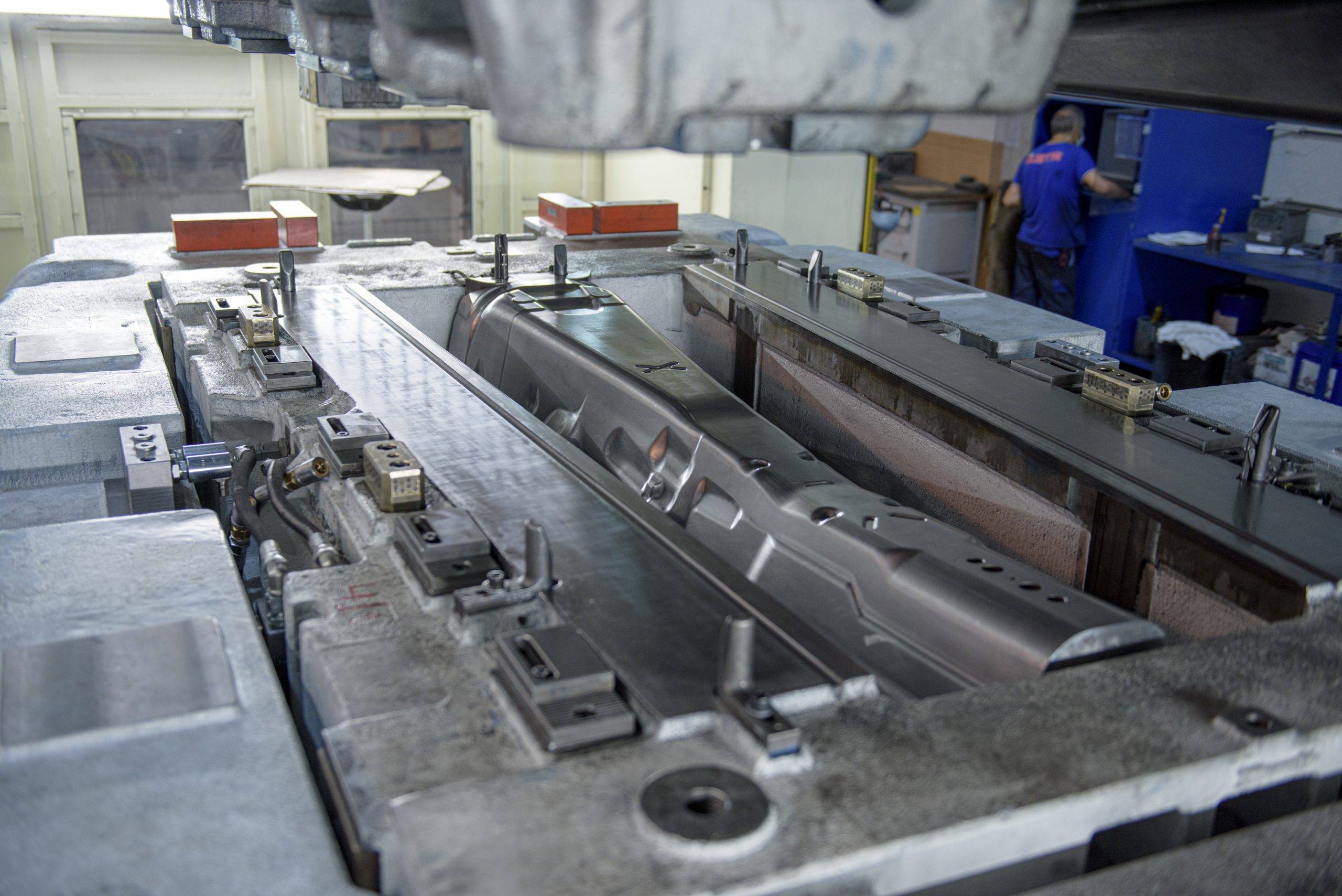
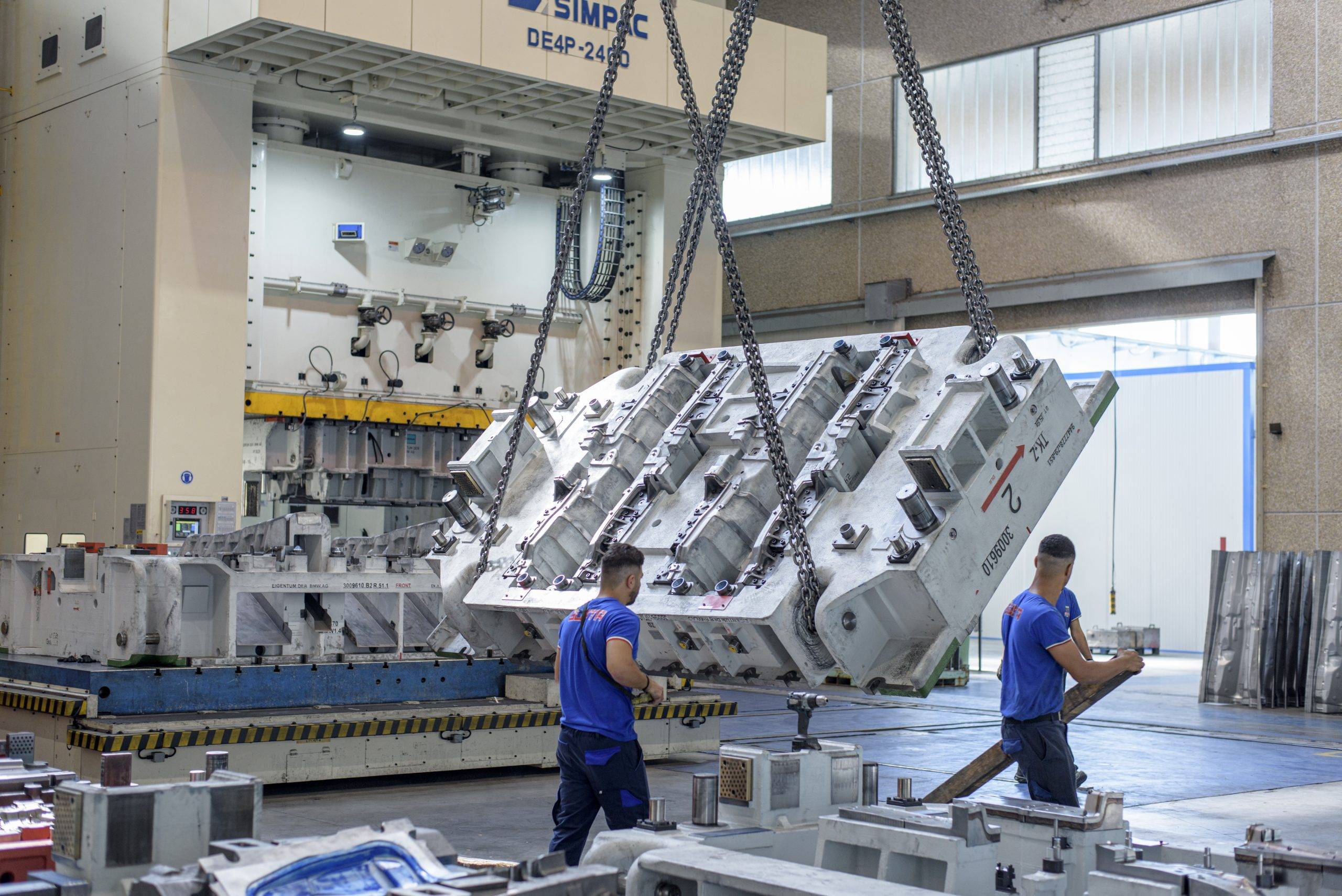
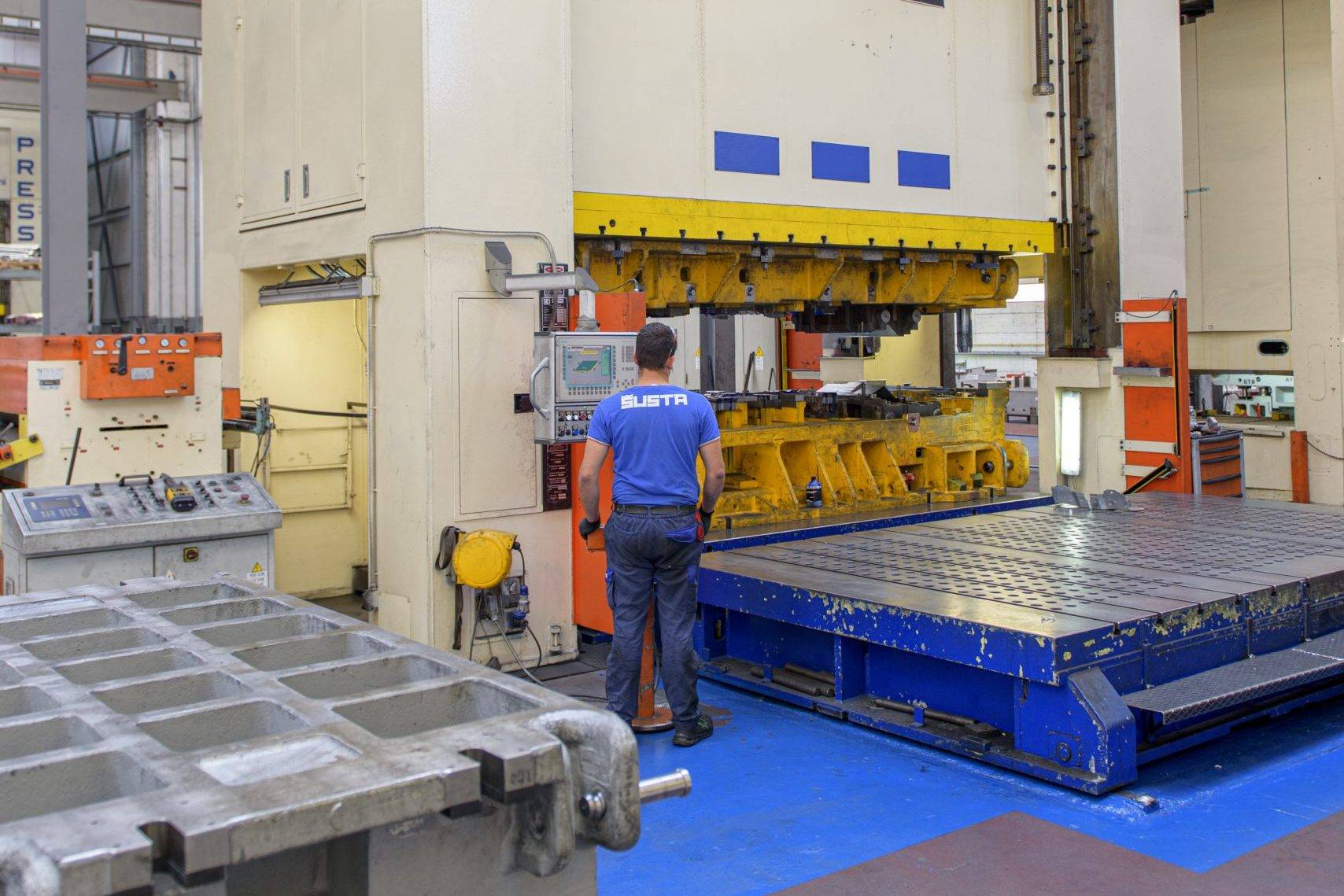
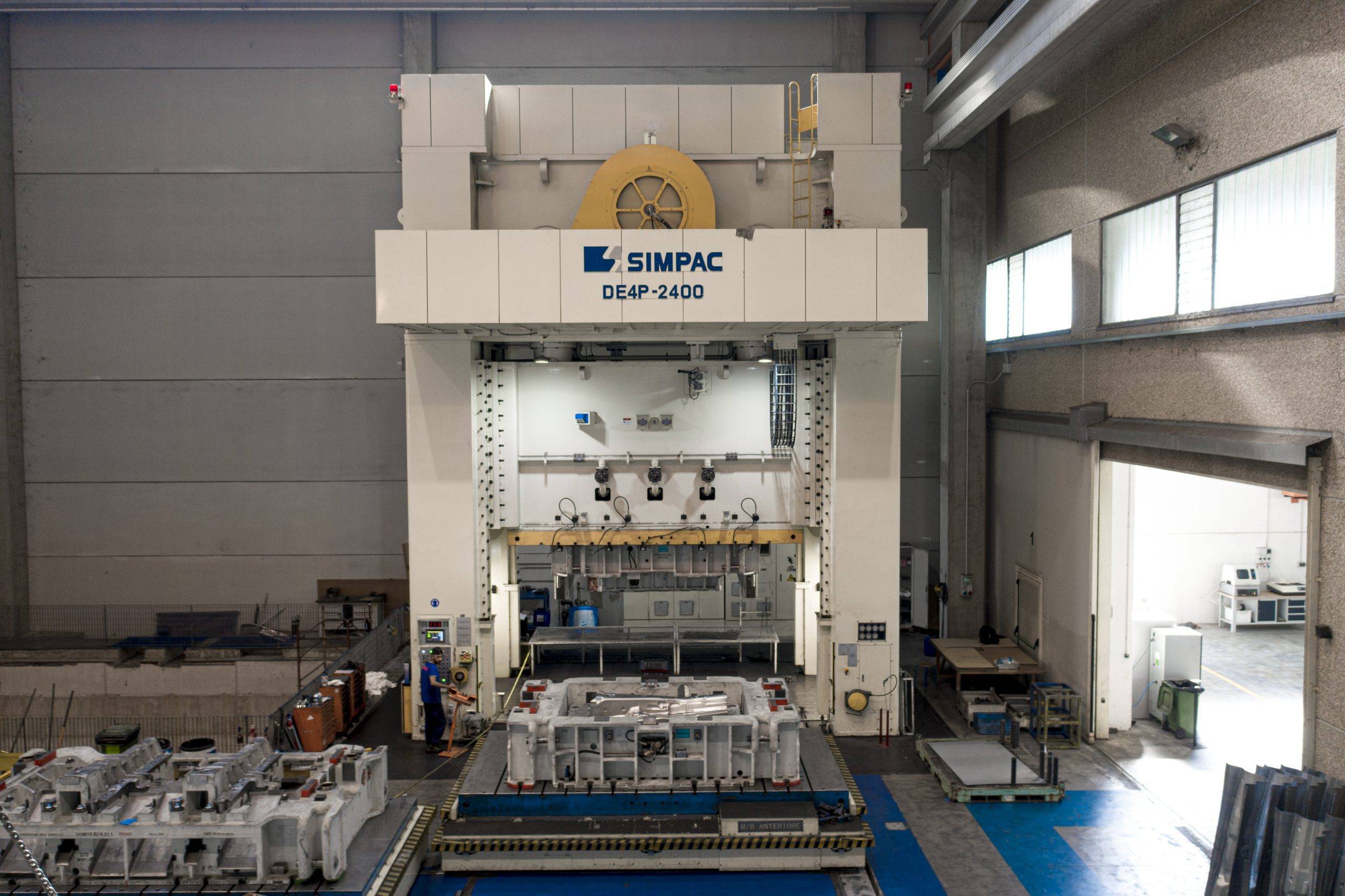
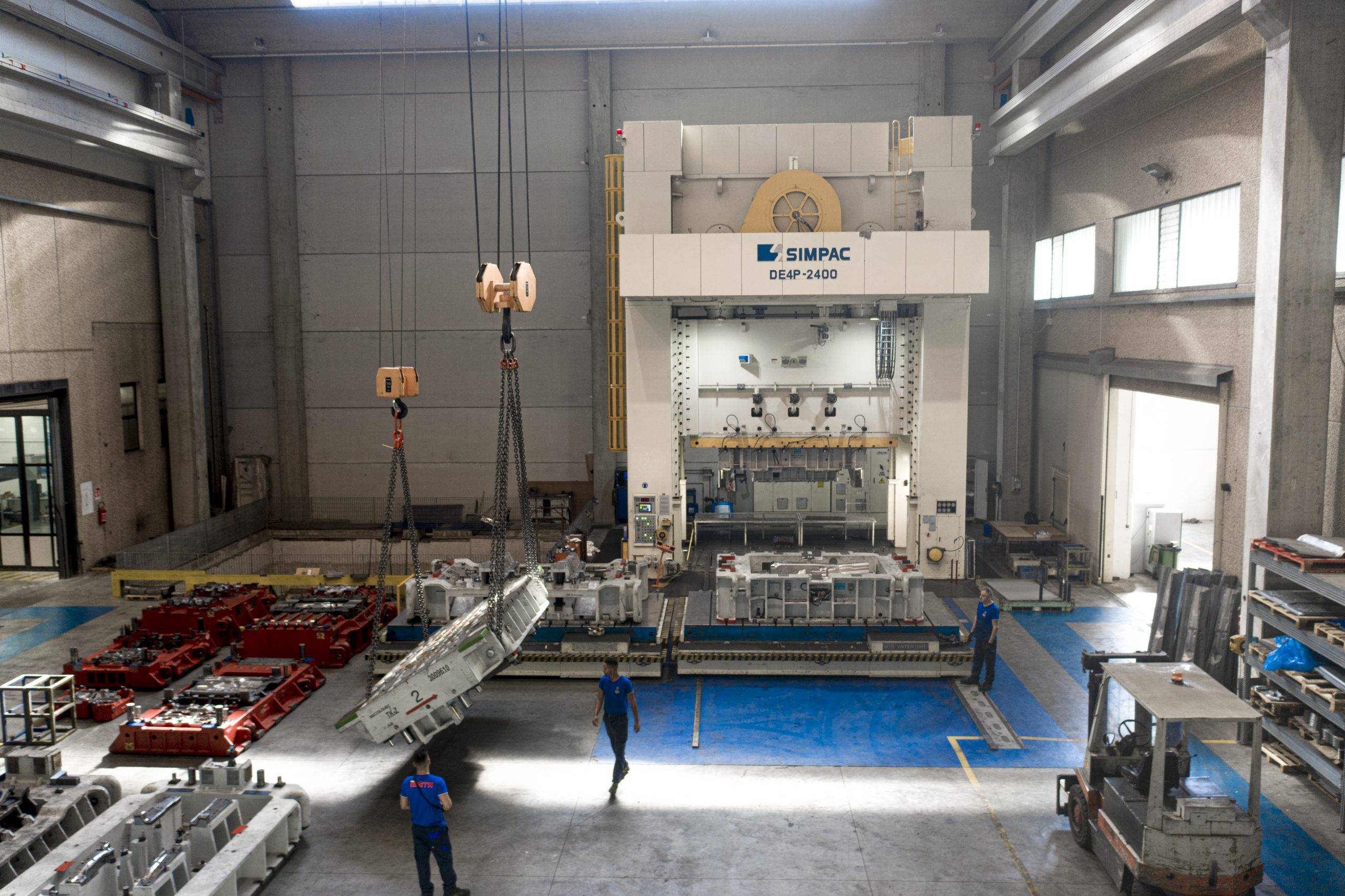
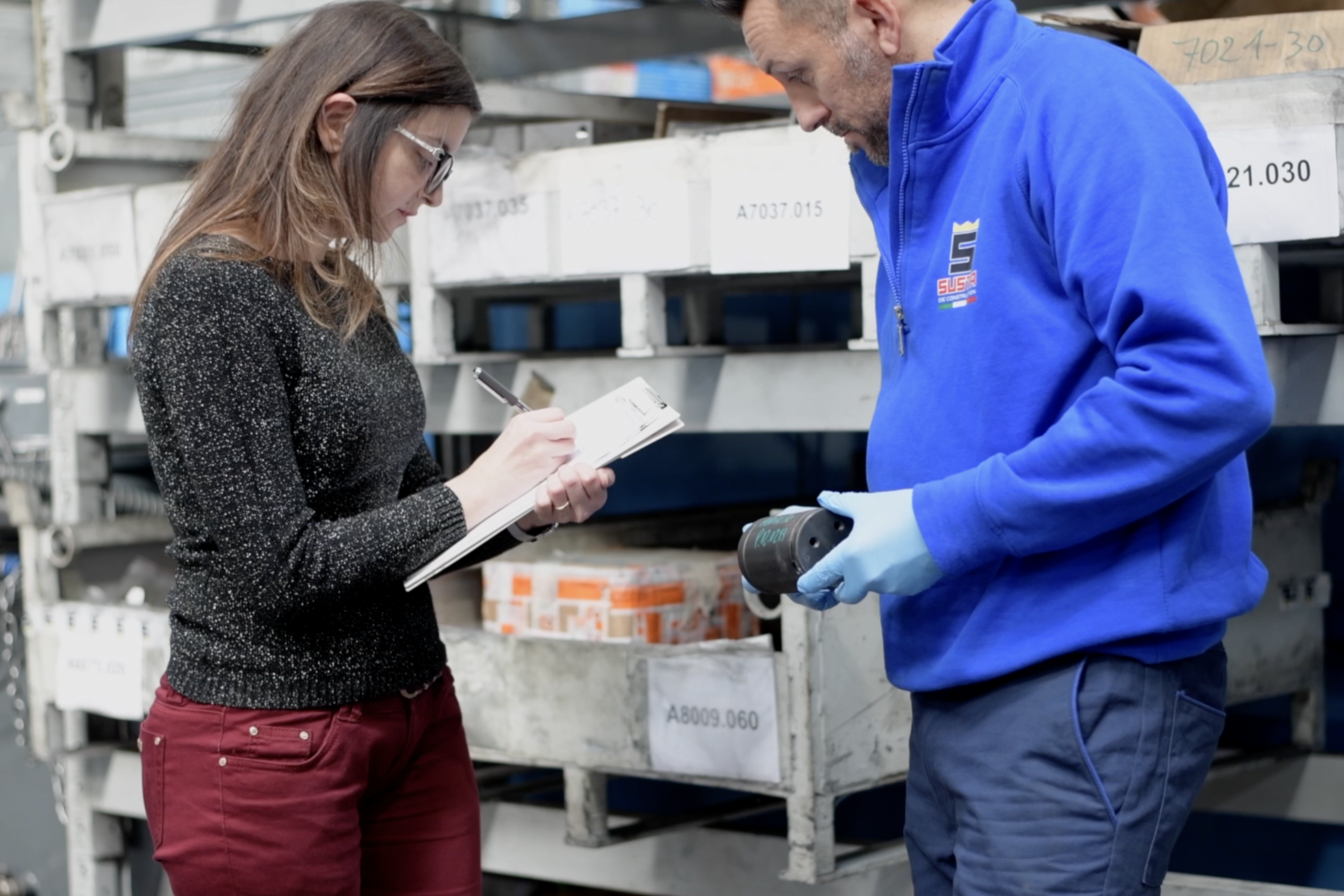
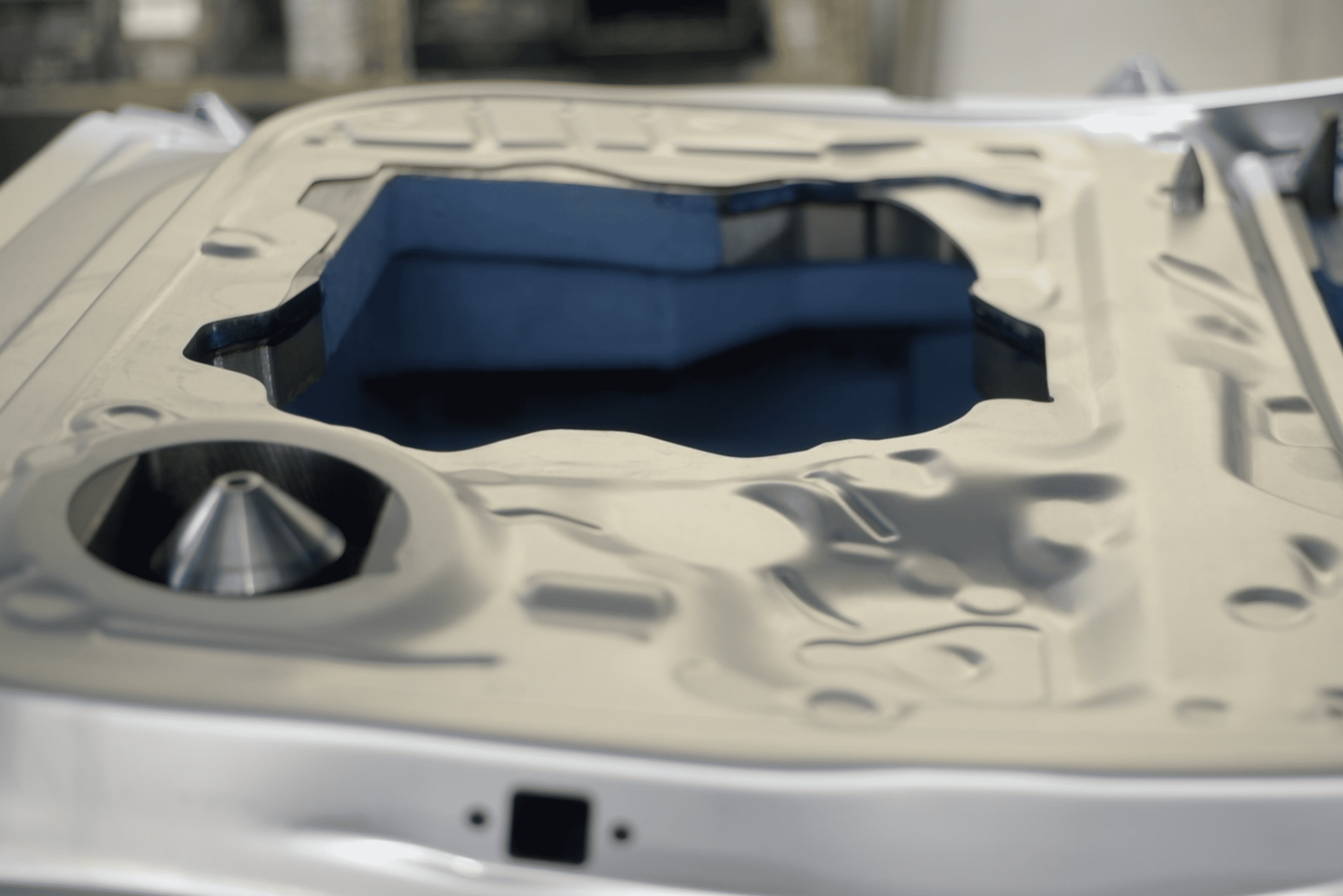
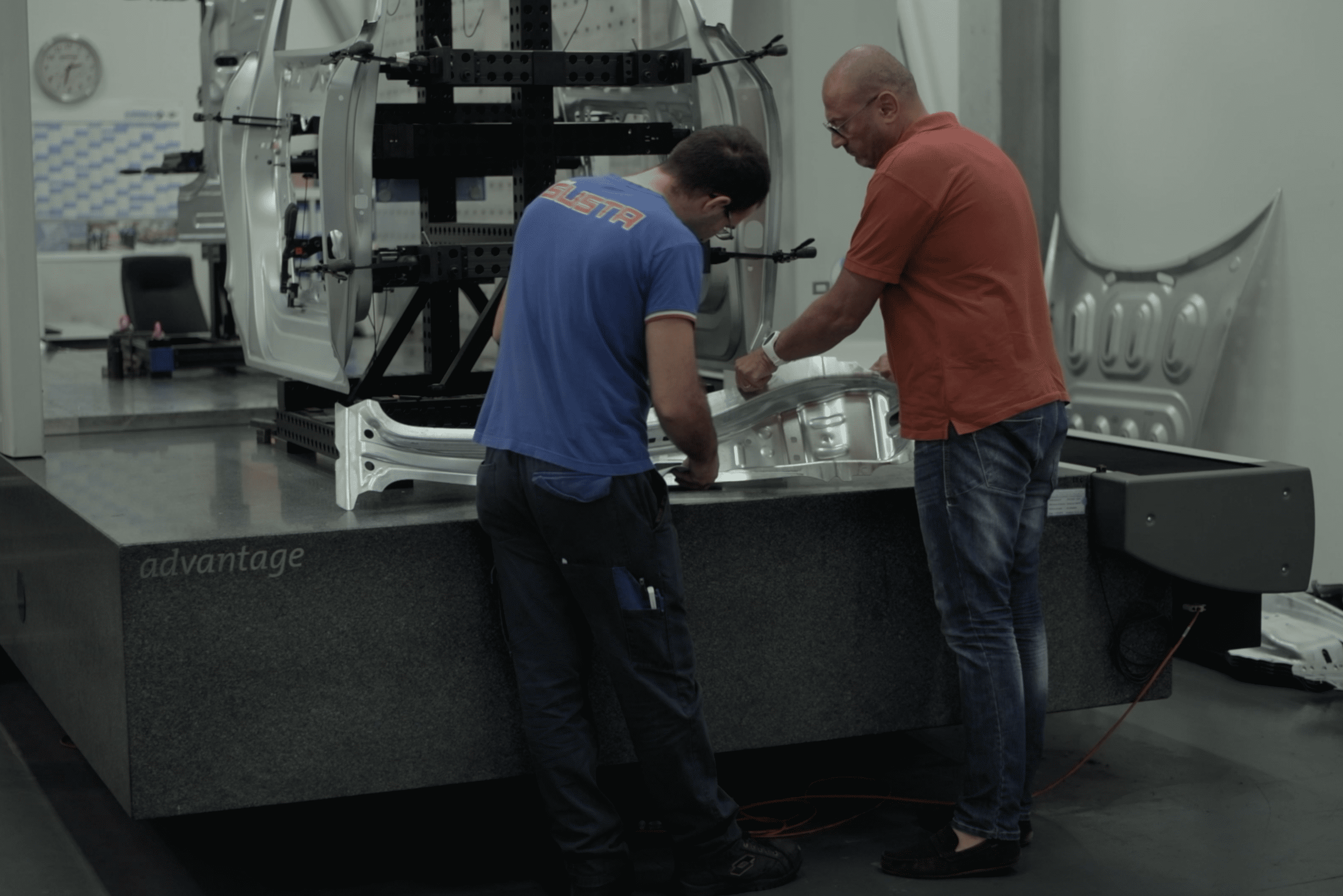
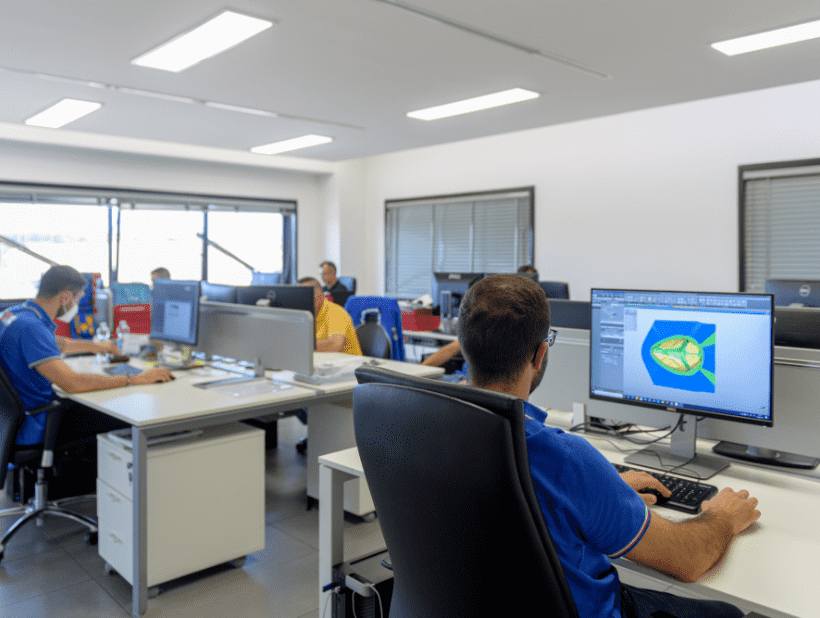
LOREM IPSUM
Lorem ipsum dolor sit amet, consetetur sadipscing elitr, sed diam nonumy eirmod tempor invidunt ut labore et dolore magna aliquyam erat, sed diam voluptua. At vero eos et accusam et justo duo dolores et ea rebum.
Quality control
Quality control activities on measuring machines are carried out in 2 work shifts thanks to qualified and constantly trained personnel: each part shall comply with the correct geometry and with precise dimensional characteristics.
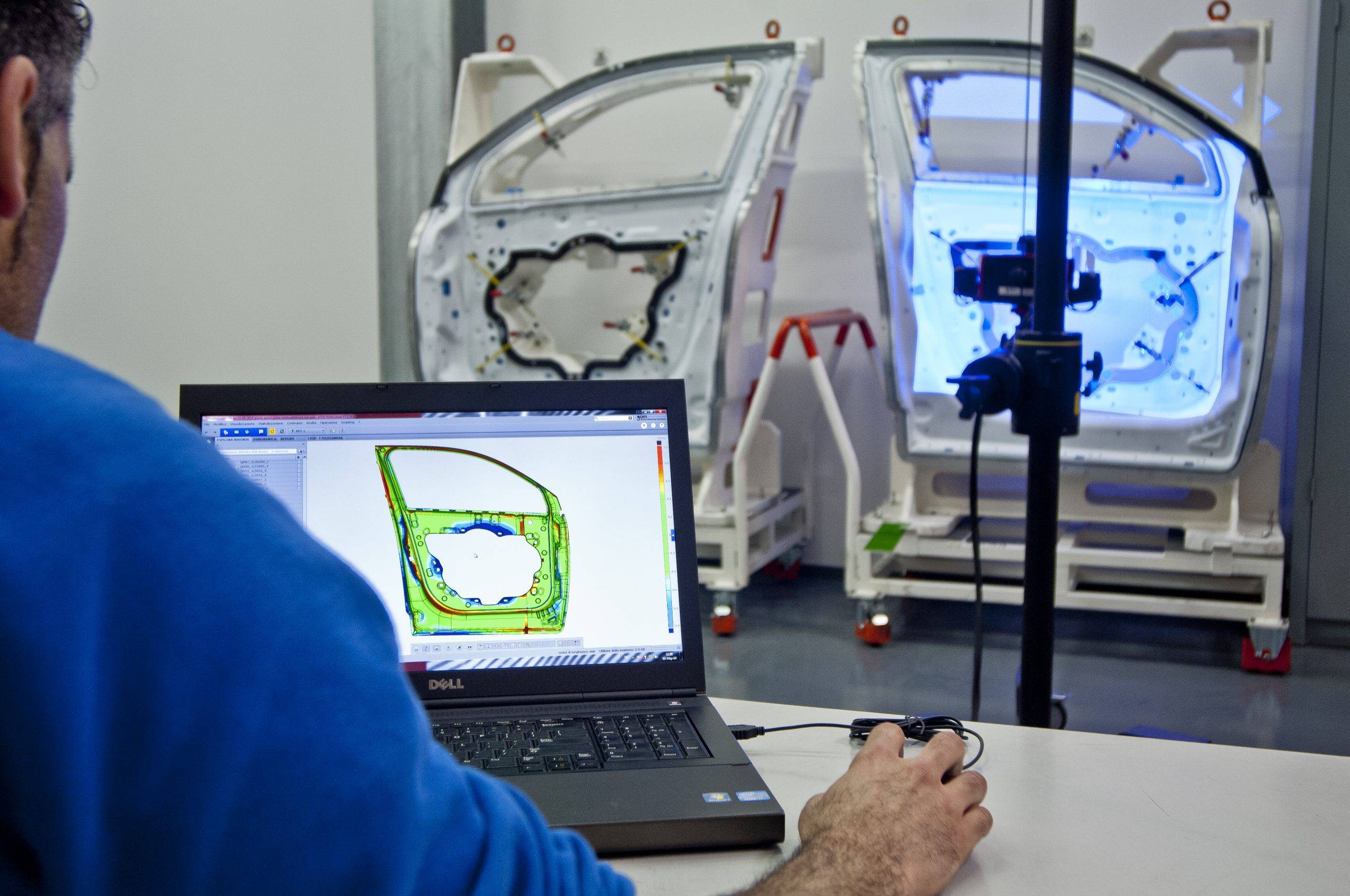
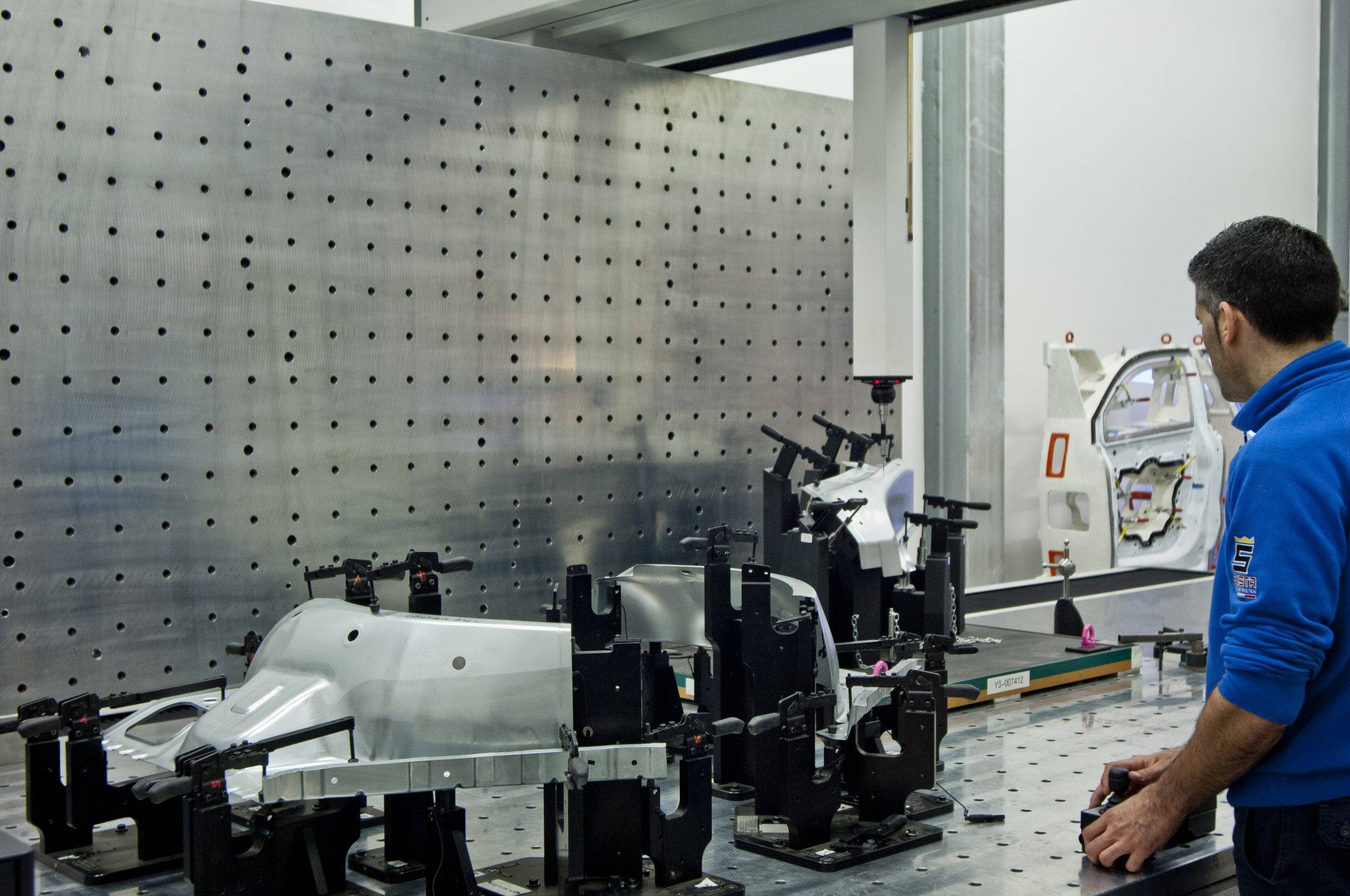
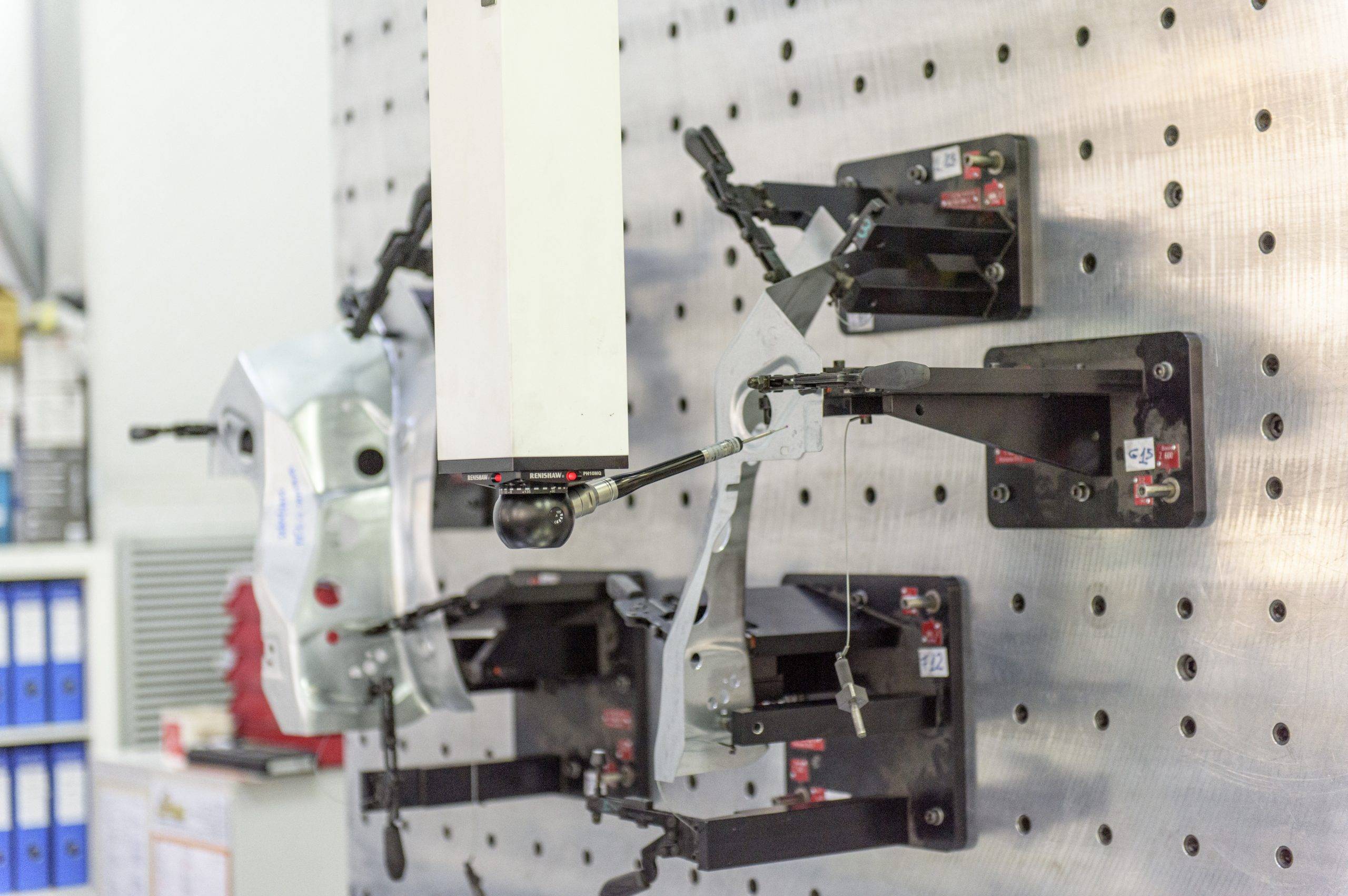
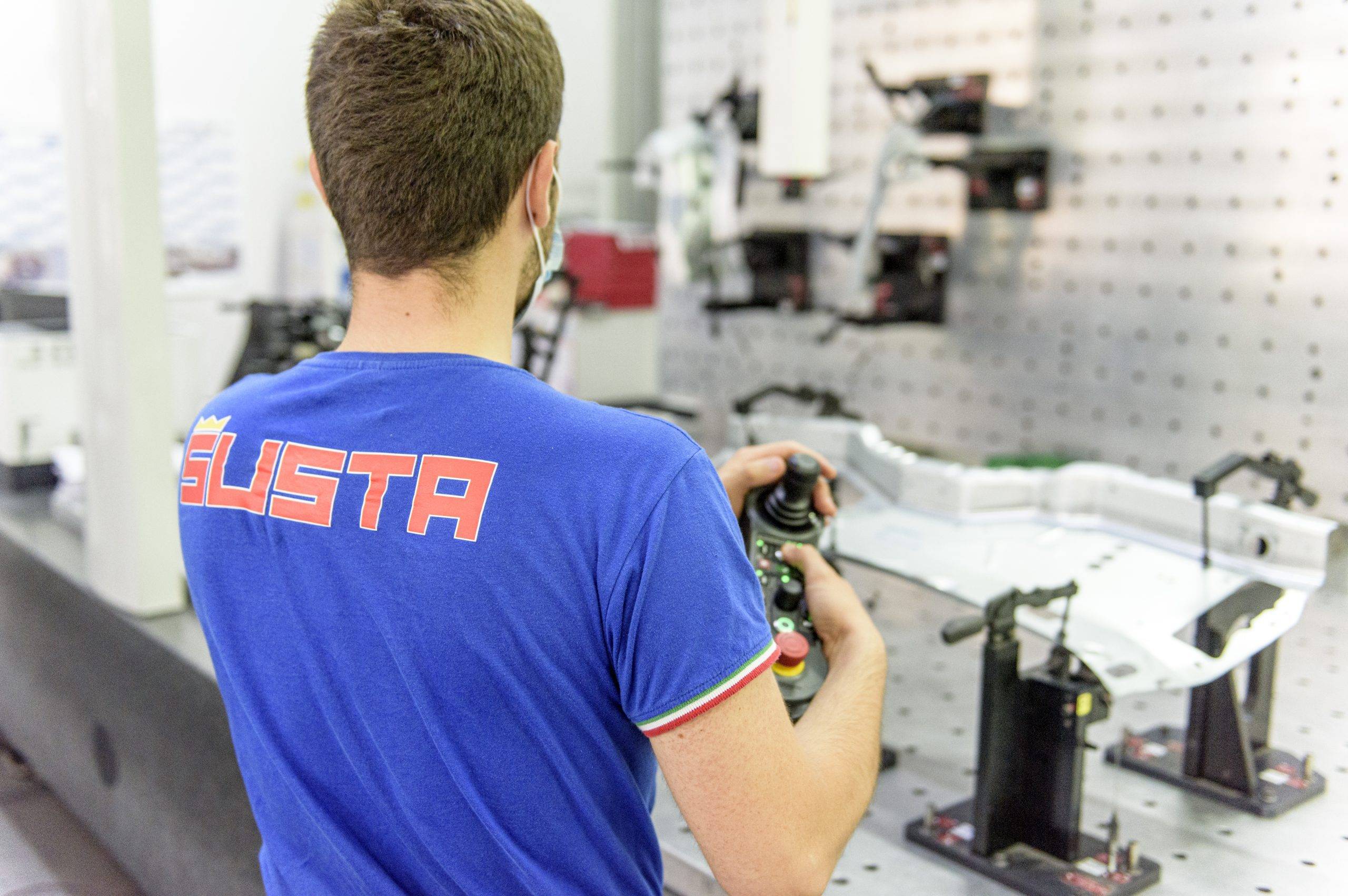
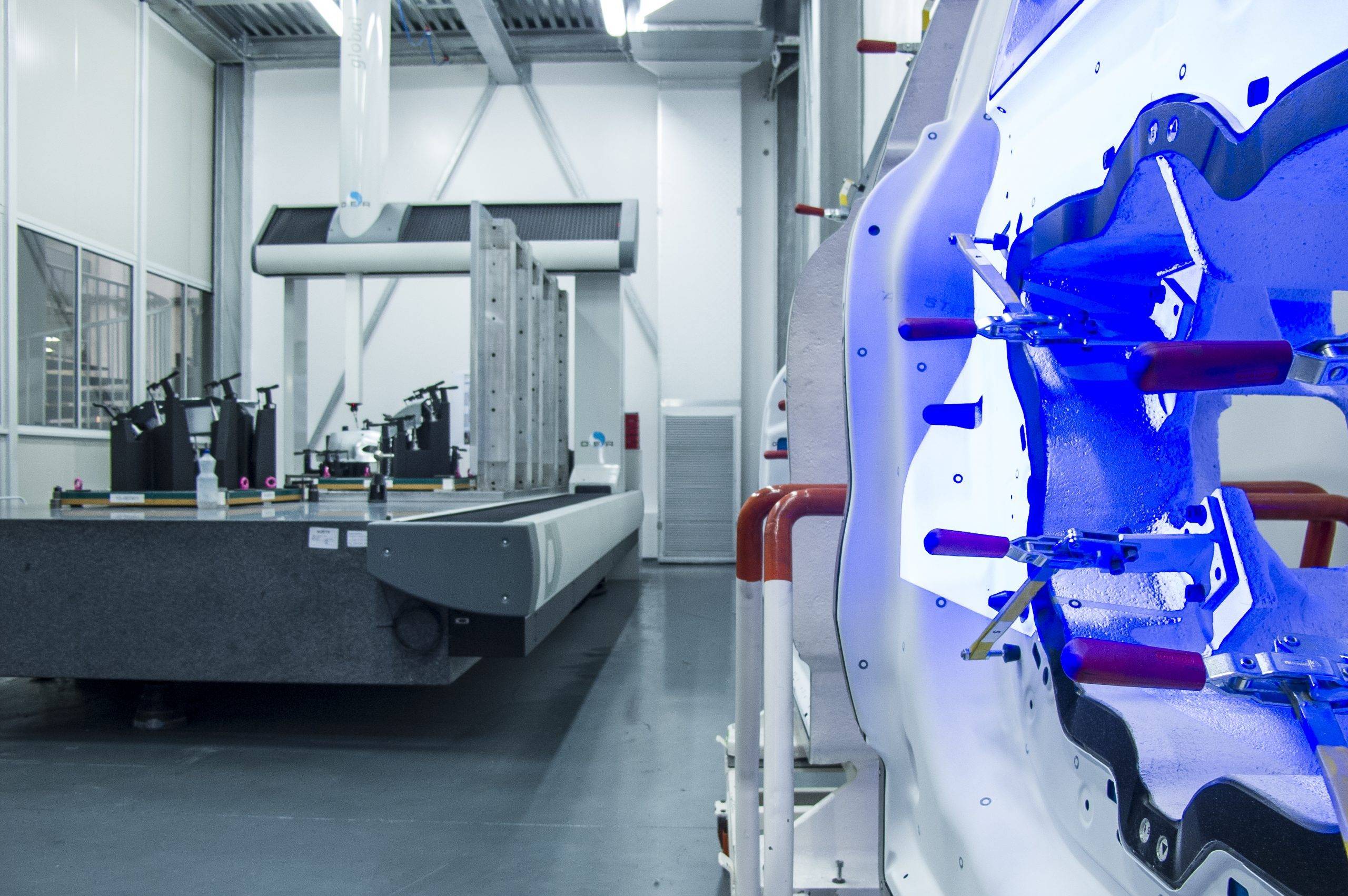
In Susta there are two metrology rooms with controlled temperature to check these features, both fitted with coordinate machines and photoscan, this one also used for reverse engineering.
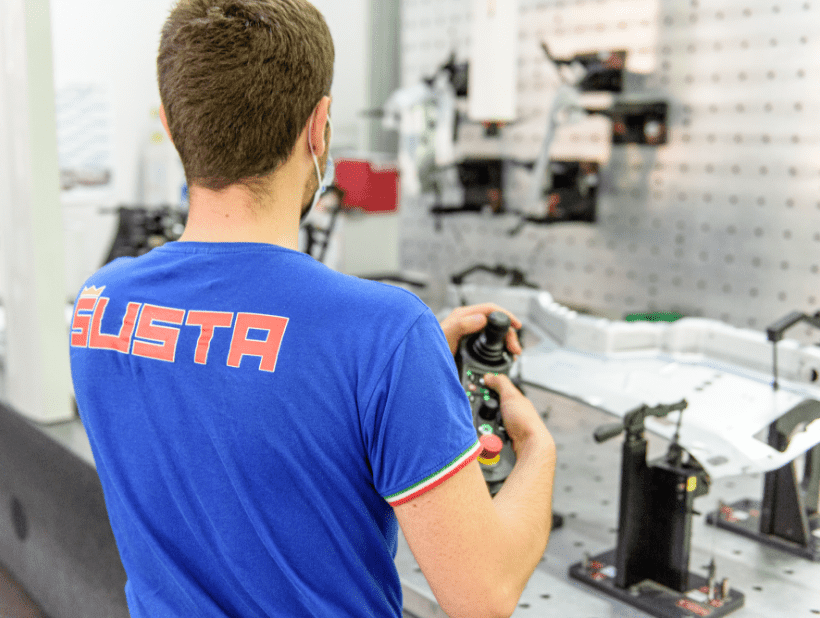
Commissioning
L’ultima fase è rappresentata da un momento di cruciale importanza, che sancisce l’efficacia e il valore di tutte le fasi precedenti: l’inserimento degli stampi presso la linea produttiva del committente.
Nell’ottica di massimizzare la qualità di ogni passaggio, Susta ha scelto di formare per questa fase squadre di specialisti nel collaudo che, grazie a comprovate competenze tecniche e linguistiche, terminano il lavoro presso gli stabilimenti di produzione del cliente. Per rendere più rapida e precisa la finalizzazione di questa attività, i team sono specializzati per ogni singolo cliente.
DIE COMMISSIONING IN THE CUSTOMER’S PRODUCTION LINE
The last step is a crucial moment that sets the effectiveness and value of all the former steps: die commissioning in the costumer’s production line.
In order to maximize the quality of each step, Susta has chosen to train several teams of commissioning specialists who, thanks to their proven technical and language skills, finalize the job at the costumer’s press shop.
For the most precise and quickest optimization of this activity, the teams are specially trained to match with each customer needs.
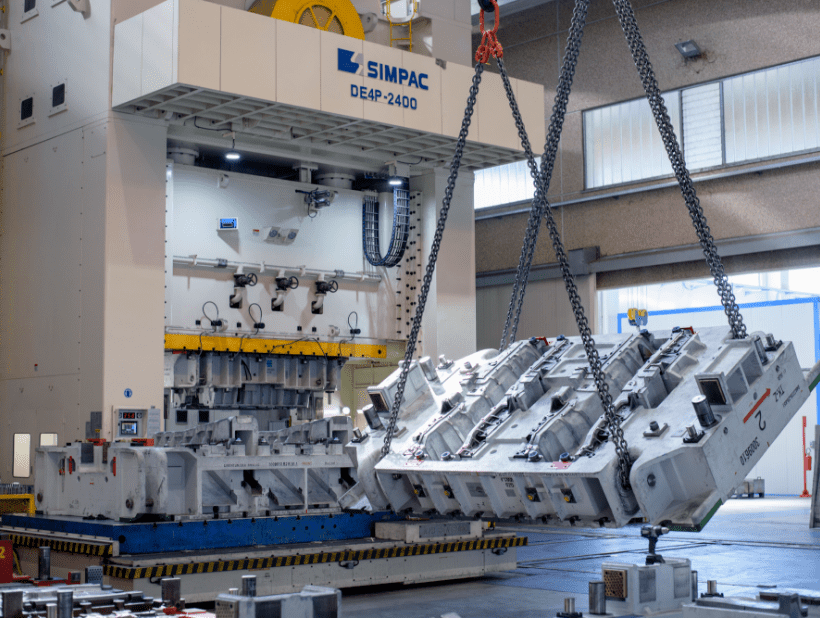